The formation of holes in walls, partitions, panel structures and other structures may be required for a variety of purposes. But even a small-sized mounting passage can cause a lot of problems during the creation process. Especially when it comes to solid-state building materials: brick or concrete. In working with soft surfaces, too, not everything is clear. In such cases, use a traditional hand tool for drilling holes. However, the workflow itself requires dexterity and care, as the risk of deformation of the areas adjacent to the processing site increases. One way or another, in each case its own nuances of drilling are assumed, which should be disassembled separately.
In what cases are drilling operations used?
Fields of application of technical devices and equipment for creating holes by drilling are quite extensive. First of all, we are talking about repair and installation operations, during which builders create channels for laying communications. Moreover, the sizes of such holes can vary from 1 to 20 cm. Small passages are necessary for cabling telephone lines, information networks, etc. Such work requires delicacy and high accuracy. Therefore, it is recommended to use an electric tool for drilling holes, which can be represented by a multifunction drill. Also, the need to create holes may be due to the laying of utilities. This group of installation activities includes the installation of water, gas, and heating systems.
Varieties of drilling tools
How diverse are the parameters of drilling drilling operations, the range of tools designed for their implementation is just as wide. The classic and most common type of such tools is the mentioned drill. She, by the way, also suggests several subtypes. For example, there are traditional mechanical drills, network and cordless modifications that can perform tasks away from the outlet. There are also groups of special tools. They are designed to work with specific hardware. For example, a beginner in the carpentry may wonder what is the name of the tool for drilling cylindrical holes in order to further insert round tenons? For such operations, a perk is used - these are center drills that allow processing even across the fibers.
A separate group of more powerful machines working with concrete. Manufacturers offer for such tasks and manual punchers, and massive units resembling machines. The features of such equipment include increased productivity and the ability to form large niches in the walls of any complexity. The tool for drilling holes in concrete can perform tasks thanks to special equipment, which is most often represented by diamond cutting elements.
Wood tool
In such works, a spiral drill is most often used in the configuration of a mechanical drill. With the help of such a set, it is possible to qualitatively process not only wooden blanks, but also plastic with thin metal. Depending on the requirements for the parameters of the hole, the appropriate drill size is selected.
In this category, several varieties of work items can also be distinguished. For example, spoon nozzles are used to obtain large diameter niches, and for small gaps, it is more advantageous to use screw or screw devices. Regardless of the type, a tool for drilling holes in a tree provides a special cutting pattern. The fact is that the cutting edges process the fibers of the material so that the particles formed with sawdust are discharged along the helical grooves and do not interfere with the further process.
Perforation as a type of drilling
It has already been noted that in construction most often requires the creation of holes with a diameter of several centimeters. Of course, there are exceptions. But perforation even involves working with a tool that provides accuracy of the order of 0.25 mm. In such operations, drills are used, the diameter of which on average varies from 4 to 8 mm. Perforation itself is one of the ways to create small, but difficult to configure holes in large numbers.
Usually a round one is used, but a rectangular processing pattern is also found. The target material is paper and cardboard sheets folded in bundles, and a tool for drilling holes of this type represents a separate group. Basically, special knives are used for such tasks, which differ in size, shape of the cutters, punching steps and other parameters. Used drills have a cutting edge on the outer edge. This makes it possible to make precise holes along the entire length of the channel.
Tool for metal
The creation of holes in metal workpieces can be performed by punching. Typically, such a tool is used in working with sheet soft material. For thick workpieces, special machines or electric drills are more often used. Often there is a need to expand existing openings or only the upper parts. Such recesses may be required to further tighten the camouflage bolts, screws and screws. To do this, either special drills with appropriate nozzles are used, or a countersink tool.

A feature of working with metal is the use of a machine vice, fixing the workpiece. For wood, such equipment is not necessary. So, the workpiece is attached between the jaws by rotating a special screw. If, in combination with a vice, a tool is used to drill holes in the metal in the form of a machine, then the fixing device can be fixed directly to the work platform. But that is not all. Some models of drilling machines include a set of locking mechanisms with convenient devices for adjusting the position of the workpiece.
Concrete drilling tool
In the processing of concrete and brick walls, equipment is used in the form of electric, hydraulic and other drilling rigs with impact effect. As already noted, the initial level of this group is a perforator. But also modern electric drills in some versions have the option of connecting impact. Another thing is that the power of such models will be sufficient only for a single execution of operations with thin walls. The most popular is diamond drilling of holes in concrete. The tool for carrying out such activities is, in essence, a machine tool to which an electric motor is connected.
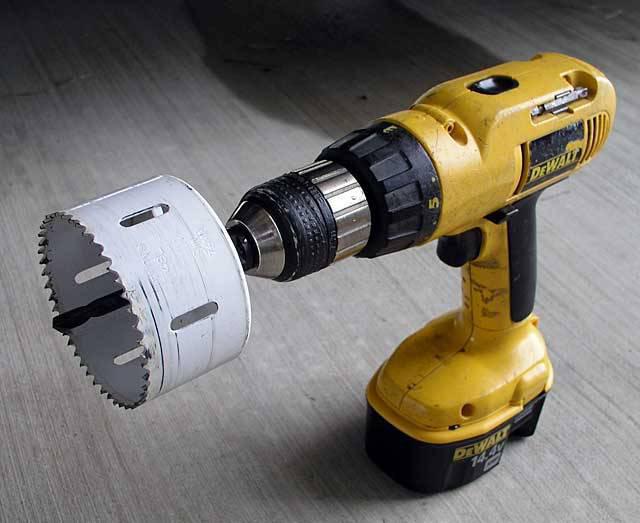
The features of such units can be attributed to three points. Firstly, it is a high-strength construction with a housing that ensures reliable installation of equipment in the place where work is performed. Secondly, there is a power drive, which determines the ability of by no means rather large cutting elements to perform complex drilling operations. Thirdly, these are crowns and drills, which in themselves are represented by high-strength diamond parts that require cooling during operation.
Diamond drilling technology
There are several varieties of drilling machines that implement diamond cutting technology. The most common electric drill. Its equipment includes two engines. Direct processing is carried out under the influence of about 3 thousand beats per minute. In this case, the second engine rotates the diamond drill itself, the speed of which is adjusted by the user in accordance with the requirements for the result. Depending on the crown used and the power potential available to the installation, the operator can expect to receive holes in the range of 30-160 mm.
Of course, such high performance characteristics also determine the corresponding investments that diamond drilling of holes in concrete requires . The tool, the price of which is 100-150 thousand rubles, can be attributed to the initial level. The middle and most common segment are installations with a capacity of about 2.4 kW, capable of forming holes of the order of 40-250 mm. Such equipment can be purchased already for 200-250 thousand.
Drilling instruction
Work begins with preliminary marking of the working area on which drilling will be carried out. Depending on the tool, the designation of the cut point can be done with a pencil, marker or using a core. Next is the preparation. At this stage, you should check the integrity of the housing, the reliability of the fixation of the working element. And if we are talking about an electric model, then it is necessary to evaluate the quality of the network connection. When the tool for drilling holes is ready for use, you can start the operation. Experts do not recommend exerting excessive efforts to ensure mechanical impact on the workpiece. Especially when it comes to wood.
Ways to prevent overheating of the drill
A powerful and productive tool, as a rule, is equipped with automatic means of supplying water to the cutting head. This allows you to protect the equipment from overheating and extend the life of the same crowns. However, the tool for drilling holes does not always provide for such technological solutions in the design. This usually applies to machines working with diamond elements that quickly enter the high-heat stage. In other cases, for example, when working with a hammer drill, it is recommended to separately provide a container with cold water. It will be possible to moisten the nozzle with the liquid as the work proceeds.
Tips for drilling different materials
In working with wood, it is worth using a mechanical hand tool in the form of a drill or rotor. Usually the emphasis is pressed with the left palm, and the operator rotates the handle with the second hand. In this case, the direction of movement is clockwise. As the process is completed, the pressure should be reduced, which will allow to form the most even cut along the edges. Work with metal is greatly simplified through the use of automatic machines. In this case, the user is only required to correctly install the workpiece in a vise and adjust the unit to the appropriate drilling parameters. The main work with diamond augers is in the preparation phase. Reliable fixation and adjustment of cutting elements is the main thing that requires a user a tool for drilling holes in concrete.
Types of nozzles for such equipment are very widely represented and differ in different ways. Therefore, it is important to determine this part of the preparation. Diamond drills exist in sizes from 8 to 16 mm in diameter. Depending on the requirements for the hole, this or that nozzle is selected. Further, the characteristics of the drill in terms of the ability to cut concrete are taken into account. Manufacturers produce such elements specifically for working with concrete brands M250-M500.
Conclusion
Work on creating holes is one of the most common operations in the process of household repairs. For example, drilling holes with a diamond tool allows you to get the channels in the walls necessary for laying the pipeline. Medium-power electric drills provide the possibility of networking for air conditioning, and high-precision drills allow you to organize thin lines of wiring. The tool for drilling is also used in other areas, including the production of products with perforations or the formation of technical openings in building materials.