The current source in the welding industry remains one of the most important components on which the efficiency and quality of the entire work process depends. This is especially true for methods that require the use of piece electrodes, by means of which an electric arc thermal effect is realized. The optimal solution for energy support in this case is a welding transformer - it is quite simple in its design, but at the same time a reliable and inexpensive source of energy supply.
Device device
A typical transformer is based on a metal core with thin wire windings (aluminum or copper). Windings have two levels - primary and secondary. Accordingly, one winding is connected to the mains, and the second provides energy to the electrode. The primary level is formed by two coils fixedly fixed at the bottom of the core. As for the secondary winding, then it is formed by a pair of coils, but also provides the possibility of its movement relative to the core. From the point of view of an external device, a welding transformer is a metal box that has a wide infrastructure for electrical connections. As a rule, the device also provides protection means, protection against short circuits and conclusions for connection with grounding elements. For convenient work with the transformer, the design also contains handles, ergonomic controls, and in the latest models, digital control panels.
Operating principle
It follows from the fact that the main task of such devices is to convert energy for subsequent power supply of welding working equipment. Once at the primary level of the winding, the original current is converted into electromagnetic energy, after which it enters the secondary winding. During this transition, the voltage index decreases. The action of this regulatory principle of a welding transformer is due to the design features of the coils. Since there are fewer turns on the second winding, when current flows into it, excess voltage is removed to the required value. In other words, ordinary mains current is transformed into a welding current. Of course, the magnitude of this correction is conditional, since there is no clear concept of the current required for welding. The operator can adjust the gap between the coils, thereby adjusting the characteristics to the desired value in accordance with the task.
Transformer Current
There is a direct correlation between the possibilities of heat treatment of metal products and the applied current strength. The thickness of the electrode is usually used as the calculated parameter. The average range is 5-10 mm. Such electrodes can be used in welding a power supporting structure with gratings, frames and thick rods. In this case, the current strength of the welding transformer can be 140-160 A. This is the optimal value for medium-sized operations, in which, by the way, not only power is important. For example, the same current level during operation of small devices with rutile electrodes up to 10 mm thick will not only provide power support for the thermal charge, but rather determine the stability of arc burning. In some cases, an increase in this indicator also contributes to the easy removal of slag.
Power transformer
The power range on average varies from 2.5 to 20 kW or more. What does this characteristic of a welding transformer affect? Contrary to popular belief, power in this case does not indicate the ability of the equipment to work with certain blanks. As noted above, performance is more dependent on current strength. However, the power determines the energy potential of the device in terms of the ability to service certain tasks with the connection of the current strength of a specific value.
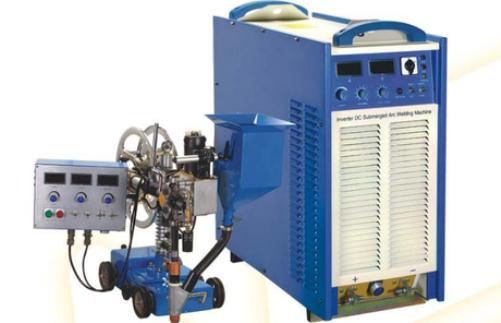
As an example, it is worth considering one of the most powerful professional welding transformers in the Russian market - TDM-402 from the Uraltermosvar enterprise. Its power indicator is 26.6 kW. It is thanks to this value that this converter allows you to work with a current strength in the range from 70 to 460 A. It is obvious that the requirements for voltage also grow - a three-phase network of 380 V. is used. What does this give in practice? The device allows you to work under intense loads with increased amperage in long time sessions. If we were talking about similar performance indicators, but with less power, then in the process of performing the same operations the equipment could overheat and, in principle, not maintain sufficient performance.
Voltage indicators
Roughly speaking, the entire assortment is conditionally divided into models operating from single-phase networks and devices connected to three-phase power supply lines, as is the case with the TDM-402 version. Accordingly, the former operate under a voltage of 220 V, while the latter operate at 380 V. It is obvious that a single-phase network is less demanding on power and covers the resources that are used in small operations. Such models are more suitable for garage and cottage work. However, there is an intermediate group of devices with a "floating" voltage. Welding transformers of this type can be connected to both types of networks. Moreover, this feature is important for ordinary users, and for specialists. It is not so much about universality, but about the advantages that it gives the opportunity to work from different sources. For example, if there are two networks, the owner of the device with nominally small characteristics will benefit from connecting to a 380 V network, since against the background of a balanced load distribution there will be no power surges. As for the owners of professional equipment, in their case, connecting to a single-phase network will be more profitable when working at minimum workload.
Load duration
The load duration coefficient (LO) indicates the ability of the device to work for a certain period of time without the need for shutdown. Shutdown refers to a forced break associated with overheating or electrical overloads. The welding transformer load duration is a percentage that represents the fraction of the working time from a 10-minute interval. In other words, how many conditional minutes can a particular device work without stopping out of 10 minutes. The range of PN varies from 10 to 90% depending on the model.
But is it possible, in principle, to pay 100%? Should I look for such devices? This is impossible, and even high rates from 70-80% are considered by experienced welders to be a marketing ploy, since in any case, work in overload conditions will sooner or later lead to malfunctions in one or another part of the structure.
Functions of modern welding transformers
Manufacturers of this equipment seek to think through ergonomic control systems, which provide extensive means for setting and adjusting operating parameters. The basic function of this type is the ability to smoothly adjust the AC power using the controller on the user panel of the welding transformer. The same applies to the choice of the active phase of the voltage - 220 or 380 V. For convenient monitoring of the current state of the working process, indicators of overheating, operating temperature and overvoltage are provided.
Features of professional transformers
This type of auxiliary welding equipment is designed for increased loads, and not only electrical ones. Several levels of structural protection are incorporated into the designs of such devices, which prevents the ingress of dirt, dust, and sometimes water, although in principle it is forbidden to use such devices even in high humidity. As for electrical indicators, they are expressed in the ability to connect to three-phase networks and wide ranges of current settings. For example, the welding transformer "TD-500" nominally operates at 500 A, but in practice, the adjustment can reach 560 A. On the other hand, the base level does not fall below 100 A, which limits the possibility of using the unit in small welding operations. The disadvantages of industrial converters include massive construction and high energy consumption.
Features of universal transformers for welding
Most of the welding work is carried out using electrodes, the thickness of which varies from 2 to 10 mm. This is especially true for workshops where welding is used to fasten metal elements of various sizes. The best choice for supporting such tasks would be a universal device. In the process, a welding transformer of this type will be able to provide high-quality penetration with thin materials and make connections of thick billets without overstating capacity and energy. What is still important in such models is the variety of accessories, the set of which also focuses on the production of welding in various conditions. At a minimum, such kits include holders, grounding aids, slag brushes, and even personal protective equipment.
Transformer Pros
It is possible to organize welding work without a transformer, but in this case obvious advantages will be missed. The main one is the possibility of not only convenient, but also precise adjustment of the current strength, which is very important for those who regularly face the need to connect metal parts. Moreover, a high-quality welding machine-transformer has high resistance to various loads, and its efficiency is about 80%. Also, such an assistant is more profitable in terms of energy consumption than most of the alternative solutions for manual welding.
Cons of transformers
Like any transitional link in the process, a third-party current converter in welding has many disadvantages. Among them are organizational costs, arc instability and high requirements for the qualification of the welder. The percentage of sprayed melt also increases, which also necessitates the completion of stripping in the working area.
Can I make a transformer with my own hands?
The problem is basically solvable, but it is important to keep in mind that the maximum voltage for improvised devices is not more than 50-60 V, and the current strength at a maximum rarely exceeds 160 A. There is nothing complicated in the assembly itself if the master knows about the basics of radio engineering. The main task is to make coils with two windings and choose the correct magnetic circuit. For coils, it is advisable to use copper wire with a cross section of the order of 4-7 mm2. Do-it-yourself magnetic core for a welding transformer is preferably done as a core of electrical steel - plates with a thickness of 0.4-0.5 mm are suitable. This task can be facilitated by taking a finished core from an old transformer. This part is usually stored ready to work. Then it remains to connect the system. The first winding, as in the case of the general circuit, is sent to the network, and the second is located nearby. Further it is necessary to provide isolation. It is undesirable to use a winding PVC film as a dielectric. Lacquered or fiberglass is best suited for this.
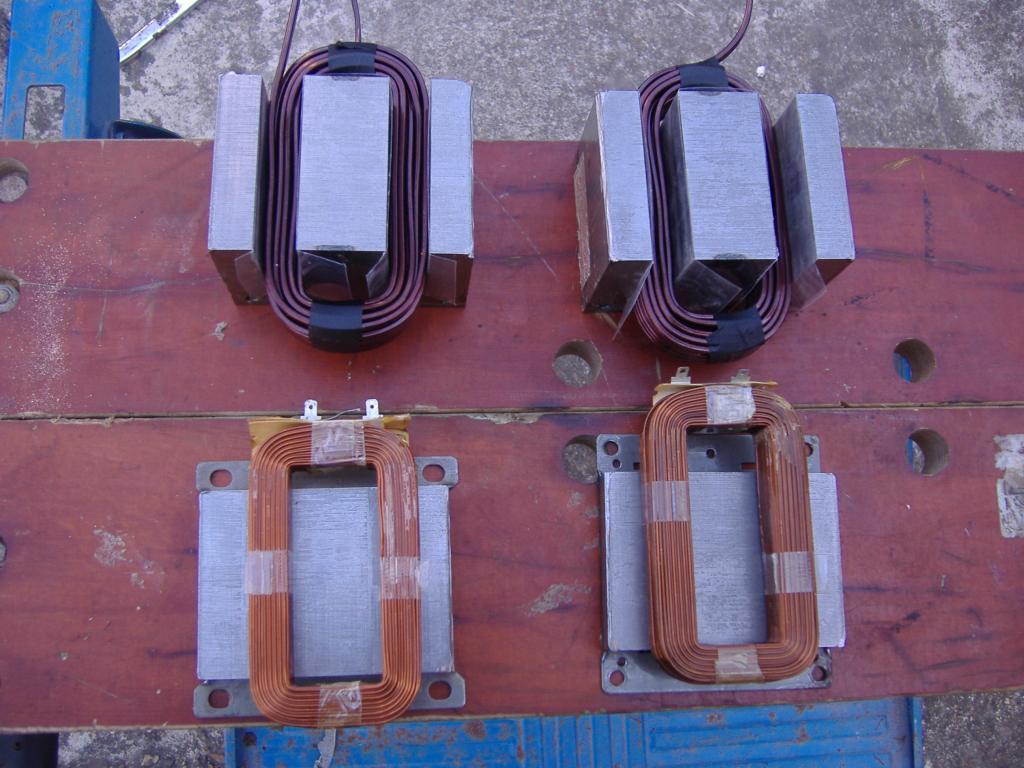
Conclusion
A correctly selected transformer according to its characteristics will be a good help in any welding production. Today, especially domestic equipment of this type retains the principles of ease of management, technical and structural simplicity and versatility. A typical example of this is the same welding transformer "TDM-402", which is inexpensive compared to foreign analogues - about 60 thousand rubles. Given the operational capabilities, this is a perfectly acceptable option. Of course, there are many other worthy offers on the market of the same class and functional level. Moreover, in each case, it must be borne in mind that the transformer still requires the contractor to have certain skills in the welding industry. This requirement distinguishes it from the inverter.