Artificial marble has the hardness inherent in natural stone, is easy to process, which allows you to give the product the desired shape. Artificial marble is warm, pleasant to the touch, has a high resistance to wear. The main advantage is that its production can be carried out at home, it is enough to carefully study the manufacturing technology of an excellent substitute for natural marble from concrete.
Concrete stone
Facing stone is natural and artificial. Artificial is a material obtained from concrete. Its appearance is not much different from natural stone. Production technology is different. Depending on this, the following types of artificial stone are distinguished:
- Agglomerates.
- Ceramic granite.
- Artificial stone made of concrete.
This article discusses the latter form.
Using faux marble
This material is most often used for exterior cladding of buildings. It is used as an alternative to ceramic tiles for bathrooms, flooring, the manufacture of countertops for kitchen tables, sinks and sinks, steps, decorative fountains and sculptures, bank, office and bar counters, fireplaces and many other items. Fireplaces serving as a center of comfort in the house are decorated with such material, and recently - a sign of prosperity and luxury. Artificial concrete marble, wherever it is applied, is a sign of exquisite taste.
Fake diamond. What is its popularity?
Decorative concrete, artificial marble, colored concrete, artificial stone, decorative marble is the same material, the basis of production of which is a cement-sand mixture, which is characterized by high qualities. Products from it have a highly artistic appearance.
Thus, marble made of concrete has found the widest application in the construction and facing works.
Features
Marble is a special natural material that gives grandeur and beauty to any building. Recently, it is often used in the interior of a house. But natural stone is expensive, not everyone has the opportunity to purchase it. Therefore, experts have developed a technology for the production of artificial marble from concrete, the appearance and quality of which are identical to natural stone, which has the following advantages:
- Finishing tiles and decor elements made of artificial marble are used for external and internal decoration of premises and structures.
- This stone does not burn, does not conduct heat and electric current. Therefore, it is widely used as a finishing material for heating radiators, ovens, stoves, etc.
- It has high resistance to household chemicals, including acetone, gasoline, alkalis and acids. This is due to the structure of the material and gives the artificial marble resistance to shock.
- Products made of it do not rot, do not exfoliate, resist pollution, and are easily washed even with plain water.
- Durability.
- Such marble is a waterproof and highly environmentally friendly material. It does not emit harmful substances.
- Artificial concrete marble is several times lighter than natural marble. When working with it, there is no need to further strengthen the surface on which it is laid.
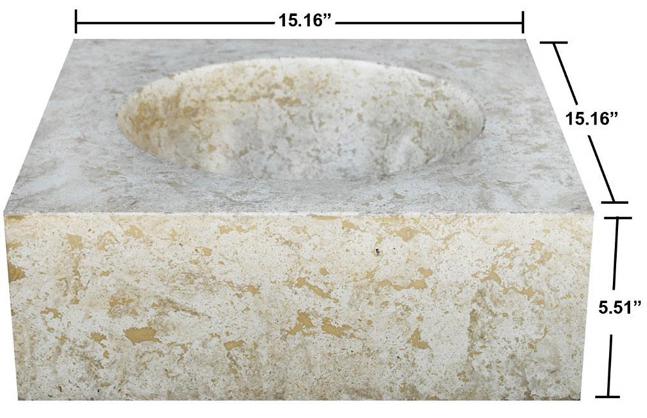
- A variety of appearance. You can realize incredible fantasies in stone by experimenting with colors.
- Manufacturability. This means that it is easy and simple to get marble from concrete artificially.
- Relatively low cost.
Materials
To make marble out of concrete with your own hands at home, you need to stock up on:
- Fine sand.
- Cement. It is better to use the M500 brand.
- By water.
- Pigment. Oil paint is suitable for this purpose.
- Plasticizer, which is added to concrete to increase its characteristics.
- Forms for pouring a solution into them. It is better to use special polymer. If you canβt buy them, any plastic ones will do. Molds can be made independently by bonding plastic panels.
- Plastic wrap.
- Vibrating table for compaction of the solution. Then the material will be more dense. But if you plan to make marble from concrete once, you can do without it. The mixture is shaken manually.
Types of concrete mix for the production of artificial marble
- Cement and sand are mixed in equal weight proportions. This mixture is used for baking brick and foam blocks.
- One part of the cement is mixed with two parts of sand (by weight). Facing tiles and decorative products are made from this mixture: window sills, steps, balusters and much more.
- A mixture of one part of cement and three parts of sand (by weight) is used to produce tiles for sidewalks, curbs, basement slabs.
Marble manufacturing technology
After preparing all the necessary materials, you can safely get to work. The production of marble from concrete begins with the preparation of the mortar. It should be kneaded in a ratio of 1: 3. The best filler is fine pebbles. Although you can use other additives: expanded clay, ceramic chips, pumice.
Technology marble concrete provides the following steps:
- Dye is added to the finished solution. The procedure for stirring it does not require much zeal. On the contrary, a heterogeneous mixture with characteristic stains is more like marble. You can conduct an experiment and add paint of different colors to the solution. This stage of the work is creative; it opens up endless possibilities to express your imagination.
- After staining the solution, you need to shake it or put it on a vibrating table, if you have one.
- Next, the solution is poured into molds and covered with a plastic film. To increase the strength of the material, it should be reinforced, for which wire is embedded in the spilled solution.
- After the marble obtained from concrete has hardened, it is removed from the molds and the surface is ground with an angle grinder with diamond disks. The surface becomes smooth and resembles natural marble as much as possible.
DIY marble made of concrete
- We fill the polyurethane form with one part of dry cement and two parts of fine-grained sand, after sifting it.
- Add small pebbles, marble chips or some other filler. We mix everything.
- Next, we take a few dyes and gradually add to the dry mixture. Thus, the added pigment will allow you to get different spots, streaks, stains, dots. The dye should be 1% by weight of the dry cement mixture.
- Add water: 0.2 parts by weight of the dry mixture. First, pour in 80% of the liquid volume, and mix everything. Add plasticizer at the rate of 1% of the mixture, mix again. After half a minute, the solution will acquire plasticity and βfloatβ. After that, pour out the remaining water and mix. We cover the forms with a mixture of polyethylene and leave to harden. Marble made of concrete, the production technology of which was tested at home, is ready.