Sliced veneer - a noble, refined material that has found itself in the manufacture of furniture and decoration materials. In the framework of this article, we will thoroughly and thoroughly understand all the features of this material, the properties that it possesses, and also affect the specifics of its production and use.
general information
Sliced veneer - a material of natural origin, obtained from solid wood by processing on modern planing machines. The thickness of the veneer varies from 0.6 to 2.5 mm. Most often it is used for the production of finishing materials, furniture, doors. If you had the opportunity to personally observe objects trimmed with veneer, then you probably noted their sophistication. This is a unique material, endowed with many advantages, which we will definitely tell about below. You can call the veneer planed premium material, because the best tree trunks are used for its production. Not all raw materials can produce high-quality veneer. But the list of species of trees from which veneer is made is quite wide: oak, ash, maple, alder. There are more valuable conifers: larch, cedar, fir. But within the framework of this material, we will touch upon precisely the veneer planed hardwoods, which endow the material with a spectacular texture and unprecedented strength.
Raw material selection
For the production of veneer, only selected trunks without knots and flaws with the correct arrangement of wood fibers are used. Of particular value is veneer obtained from natural growths of wood. They are endowed with special properties that have already been appreciated by many modern designers. Today, planed veneer is widely used in Russia. The use of high-quality raw materials in a sufficient variety of breeds allows you to get a rich color palette, due to which the scope of use of the material is significantly expanded. After veneering, the product acquires an exceptional noble appearance. Veneer is not only externally effective, it is endowed with those properties that other materials cannot boast of, first of all, strength and wear resistance. If all the intricacies of the production process are observed, it will be possible to obtain high-quality, durable and effective externally material.
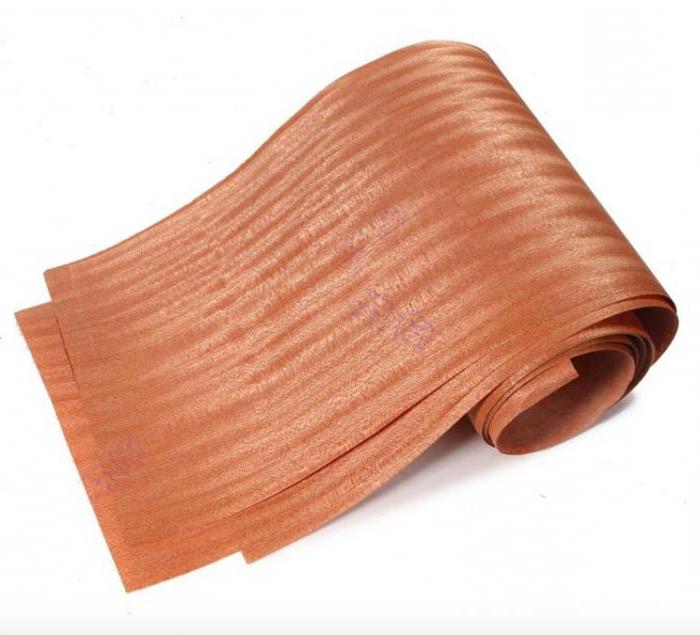
It is noteworthy that from the feedstock up to 75% of the material is obtained, which allows you to keep very affordable prices for it. Although, in truth, there are also elite varieties, the cost of which reaches tens of dollars for each square meter.
Production Features
The manufacture of sliced veneer allows the use of various types of wood, but most often it is hardwood: oak, maple, ash, beech. If we talk about the production itself, then it is carried out by several methods:
- planing the board along - in this case, it is possible to maintain the integrity of the wood fibers and remove the veneer in a single even layer;
- planing the board across - this method involves damage to the wood fibers, which allows you to get veneer with a rough surface.
It must be admitted that the first method is especially popular. To begin with, the selected board is calibrated to the required size with the help of modern equipment, then it goes through the soaking procedure until the required humidity level is reached - an important stage of work that requires strict observance of the basic principles and rules.
After all conditions are met, the direct planing of the prepared boards begins. The cyclic installation drives the workpiece in a circle, each time cutting off a thin layer of veneer from it. After the “haircut”, each layer is placed in a drying chamber, where it is dried to a moisture content of 6-8%. Modern equipment allows producing up to 10,000 square meters of veneer per month. You can rest assured: the quality of the material will pleasantly surprise you, even impress.
Advanced European equipment, by the way, allows you to dock individual veneer strips into a single sheet without a visible joint. Large-format sheets are created exclusively from the veneer of one series in order to obtain a uniform surface at the output.
Quality checking
If you decide to start production of planed veneer, GOST and other regulatory documents will allow you to comply with the basic requirements. The cost of sliced veneer is determined based on the slot of timber, the number of flaws. But the acceptance is carried out by a specially trained qualified specialist. Specialists primarily pay attention to:
- appearance - is determined visually, deficiencies are identified after checking compliance with the basic parameters of GOST;
- conformity to sizes - measurements are taken at three points located along the length of the sheet at least every 25 mm in relation to each other; To determine the main indicators, a special tool is used - a thickness gauge;
- humidity level;
- roughness;
- waviness.
The moisture level, roughness and waviness are determined based on the requirements of GOST.
Features of storage and transportation
Slicing veneer allows you to get high-quality, refined and externally noble material that requires particularly careful handling. In production, sheets are sorted by type of veneer, grade and stacked in bundles. Each pack contains at least 10 sheets. A bundle is bandaged only in one place, if the length of the sheets does not exceed 1 meter. Longer material is tied in two places to eliminate the likelihood of a fracture.
Veneer transportation is allowed only in covered machines and containers. If you use the container, you can not use special packaging veneers. But it is extremely important to ensure that packs with veneer do not bend - for this they should be laid in a special way. It is necessary to store the material in compliance with the temperature regime from -50 to +40 degrees indoors and with a relative humidity level of up to 80%.
Specifics of use
Sliced veneer of oak, ash, maple and beech is currently used as the top layer in the manufacture of furniture, doors and other carpentry. This is an excellent finishing material with which you can transform any interior. The veneer bends perfectly, so it is suitable for finishing uneven curved shapes. In addition to all of the above, planed veneer is actively used in restoration work. With its help, it is possible to make exclusive plasters, boxes, exclusive souvenir products.
How accessible
Given the specifics of production, the level of selection of raw materials, it is difficult to hope that veneer is a budget material. Nevertheless, through the use of modern equipment and advanced technologies, it is possible to maintain its relative availability. Want to make a difference? Go to the door factory or the nearest door store. Surely, with all the presented variety, your attention will be attracted to precisely the finishes of natural veneer - they look exceptionally, and they will serve for a dozen years with careful use.
To summarize
As part of this material, we examined all the features of the production of natural planed veneer, paying attention to all the details. Definitely veneer is a great opportunity to transform any interior with the help of furniture items trimmed with it. We strongly recommend that you pay special attention to it if you are looking for a more affordable alternative to the array, but are not ready to put up with the neighborhood of low-quality synthetic materials.