Not so long ago, in the field of domestic housing construction, the technology of fixed formwork began to be mastered. It involves the construction of a foundation on the basis of lightweight materials that are not removed after installation, unlike the classic timber formwork. The most common method is the device of fixed formwork made of polystyrene foam. For the foundation of a thermal home, this is the optimal solution that improves the thermal insulation and shape-forming qualities of the structure. But there are also negative factors in the application of this technology, which will also be discussed below.
Fixed formwork design
If in a traditional wooden formwork, the base performs only a temporary solution-retaining function, then expanded polystyrene forms vertical partitions, into the niches of which concrete is poured. The average wall thickness is 5 cm, and the distance between the individual structural elements reaches 15 cm. As for the height of the formwork of the foundation of this type, it can vary from 50 to 250 cm: it is important to keep in mind the possibility of building walls. Even after completion of the foundation of the device, the panels can be carried out to the roof by the principle of a designer. But this decision should be provided in advance in the project, since special jumpers are selected for it at the level of the grillage, where the overlap and foundation converge.
From the point of view of insulating properties, fixed formwork serves as a thermos. For this reason, houses at such a base are also called heat-saving. The design of polystyrene foam formwork itself is notable for its good sealing, but there is a drawback to this. It consists in the need for ventilation channels to prevent the accumulation of condensate, which negatively affects the state of the cement mortar. On the other hand, the need for additional insulation of the foundation is completely eliminated.
What is expanded polystyrene?
This is a type of composite building material, the shape and parameters of which are specially adapted to the requirements of fixed formwork. In other words, these are the elements from which the mold for pouring foundation concrete is formed. They can be made in the form of blocks, plates with perforation or large-format panels. All varieties of parts are combined with similar technical and structural capabilities.
Here it is necessary to understand what is polystyrene foam for the foundation in functional terms? This is a structural element that provides a strong reinforced frame and performs a number of insulating tasks. The increased durability of the structure retaining the concrete form is achieved by jumpers or screeds that bring the parallel frame elements together. Moreover, in each masonry, a technological gap is provided for communications.
Pros and cons of expanded polystyrene
The material is quite technologically advanced and specially oriented to use as a formwork element. This purpose causes a number of attractive operational factors, such as:
- high heat and noise insulation qualities;
- lack of need for additional reinforcement of the structure due to columns and metal bandages, since expanded polystyrene itself is quite durable;
- a variety of form factors and sizes makes it possible to implement a variety of structural variations when creating the contours of the strip foundation;
- ease and speed of construction.
It is worth noting that the formwork for the base of polystyrene foam has weaknesses, which are especially evident against the background of other products designed for the same tasks:
- The material is sensitive to moisture, therefore waterproofing measures are mandatory. The same applies to vapor permeability.
- Hardware and mounting elements that do not correspond in format to the originally provided factory holes and grooves cannot be inserted into the polystyrene foam structure.
- Some modifications of expanded polystyrene support combustion.
- There is evidence that the material may be destroyed by rodents.
- High price. The average price for 1 m 2 of polystyrene foam in the form of blocks is 700–1,000 rubles. The thickness of the walls can be from 5 to 10 cm.
If we talk about alternatives to expanded polystyrene materials, then these include cement, chip cement, foam and wood-fiber products. They are also available in a variety of structural and dimensional formats, but have other technical and operational properties.
Installation of formwork for polystyrene foam foundation
The structure is formed by assembling block or panel elements on the site prepared for installation. Throughout the process, it is important to observe the correct position of the walls vertically and horizontally - for this, a building level is used. Elements should be laid out starting from the corners by means of nozzles on the reinforcement. It is important that the same position of the grooves is maintained throughout the vertical - horizontal reinforcement will be placed in them further. Also, for the purpose of local power bonding, screeds for plastic formwork are used. They connect the two sides of the panel, forming a hollow box in which it will be possible to lay communications. The groove system, in turn, seals and fixes technological joints, eliminating the possibility of seam divergence and the formation of cold bridges.
Construction fill
After assembling the formwork structure, concrete is poured into the prepared niches. This applies to the strip configuration of the foundation, but the technology of a monolithic bearing base is also applicable, when the entire area between the walls of expanded polystyrene is poured with a solution. In both cases, concrete that has not yet solidified is equipped with reinforcing bars with a diameter of at least 10 mm. In the future, they will have to combine the foundation foundation and the formwork box into a solid monolithic platform.
Finishing foundation with formwork
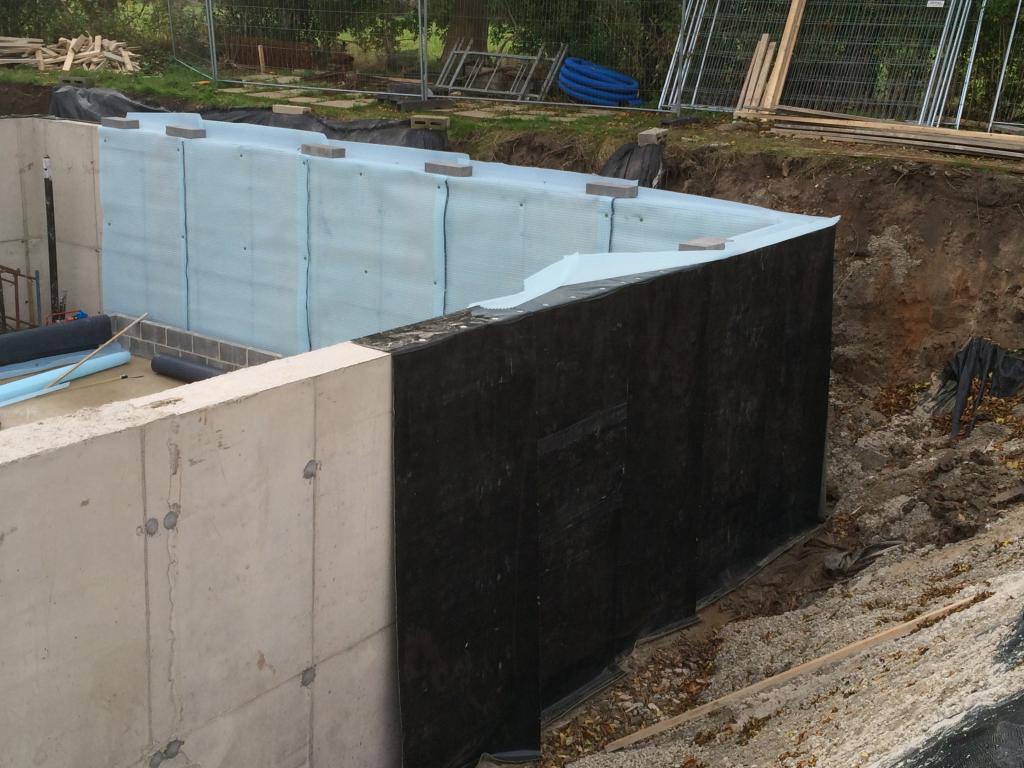
The external cladding will have two functions - the refinement of the formwork and its protection from external negative influences. Immediately it should be noted the advantage of expanded polystyrene, which lies in its almost ideal geometric shapes. Therefore, the need to align the walls of the structure simply disappears. You can immediately proceed to the external reinforcement and laying of the decorative layer. It is possible to strengthen the formwork surface with stainless steel mesh or fiberglass. These are thin reinforcing coatings that can be repaired with a plaster composition. This is followed by decorative putty with suitable textured qualities. Another interesting finishing option is allowed provided that metal formwork ties are used that extend outward, allowing the installation of heavy external coatings. The bows provide additional load-bearing force, due to which ventilation facades or siding subsystem can be fixed to expanded polystyrene blocks.
Technology advantages
If we compare the polystyrene foam formwork design with a conventional wooden assembly, then there will be a lot of pluses - both in functionality and in technical properties. The following are the most significant strengths of the formwork for the polystyrene foam base:
- combination of strength and lightness of construction;
- high assembly speed;
- variety of wiring diagrams;
- high insulating qualities;
- no need to dismantle the formwork after the foundation.
Technology disadvantages
If the advantages of the design are mainly expressed in its technical qualities, then the disadvantages are caused by the sensitivity of the material to external factors. As already noted, the blocks can undergo combustion, destruction under conditions of contact with moisture and in adverse biological environments. A serious drawback is the price per 1 m 2 of expanded polystyrene, which is about 1,000 rubles. In the final estimate, this means that the formwork for a house with an area of 100 m 2 together with installation accessories will cost about 70-80 thousand rubles.
Conclusion
Determining the choice of the method of foundation structure, it is desirable to formulate in detail the requirements for it. Expanded polystyrene is good because it expands the capabilities of a prefabricated frame, but at the same time sacrifices some of its familiar qualities. For many, the decisive factor is the ability to assemble the structure with your own hands. Polystyrene formwork for the foundation does not require the use of special installation techniques. All mounting nodes are formed by the usual set of tools of the home master. The only difficulty will be the need for accurate calculations and constant monitoring of the installation positions of formwork elements using levels and levels.