Each building has fire safety requirements. The presence of fire hoses and equipment for him is a prerequisite. This will quickly eliminate the spread of fire and the source as a whole.
Definition
The fire hose is a special hose, which is equipped with connecting heads and is used to collect and supply fire extinguishing materials directly to the place of ignition.
The device of the fire hose is not complicated - a textile frame and internal waterproofing. The frame can be made of natural or synthetic fibers, and a layer of waterproofing is rubber, latex or other polymeric material.
To lengthen the water conduits, quick couplers (BRS) are used. A fire hose with a barrel is used to deliver water to the flash point in the form of a jet. The trunks can be both high pressure and normal, in addition, they can be manual or monitors.
Sleeve classification
The classification of fire hoses includes various features. The following types of sleeves are available depending on the method of use:
- pressure head;
- suction;
- pressure-suction (combined).
Pressure fire hoses, in turn, may differ in the material from which they are made. On this basis, they are divided into two groups:
- sleeves having a reinforcing frame made of natural fibers - linen and flax jute;
- sleeves with a frame made of synthetic fibers - latex, rubberized, with a polymer coating on both sides.
Types, depending on the climate in which the hose is used, look like this:
- for temperate climate;
- for temperate and cold climates;
- for temperate and tropical climates.
If operation occurs in harsh conditions, special sleeves are required. They are divided by durability into the following types of fire hoses:
- percolated (perforated);
- heat resistant;
- wear resistant;
- oil resistant.
Pressure hose
Most often it is a pressure fire hose that is used. It is designed to transport the substances necessary to extinguish a fire (water, blowing agents, solutions). The fluid in the pressure pipe is supplied under overpressure.
The pressure hose must comply with the requirements of GOST 51049-97 and NPB 152-2000. Sleeves of this type are equipped with fire hydrants and fire trucks. They consist of a fabric frame, which is impregnated with waterproofing material inside. The frame is made of either natural fibers or synthetic.
Internal waterproofing can also be made of various materials - latex, rubber, polyurethane and other polymeric materials. If the sleeve is made of natural fibers, then the inner layer of waterproofing may be absent.
The characteristics of pressure hoses are as follows:
- minimum size in the roll and low weight;
- high strength so that the sleeve withstands high pressure;
- neutrality to hostile environment;
- resistance to abrasion;
- resistance to movement of water inside should be low;
- increased resistance to sunlight and decay.
Pressure hose marking
The industrial marking of fire pipelines of this type is as follows:
- Name or trademark of the manufacturer.
- Sleeve type pressure type. Depending on the configuration, for fire engines (RPM) and for fire hydrants (RPK). The latter, in turn, are divided into internal (RPK-V) and external (RPK-N). Depending on the material: with a double-sided polymer coating (D), with internal waterproofing (B), with the impregnation of the frame and internal waterproofing (P).
- Diameter of fire hose in mm.
- Working pressure in MPa.
- For RPK type sleeves, product length in meters.
- Special purpose if available. In turn, such products are divided into wear-resistant (I), oil-resistant (M) and heat-resistant (T). Also, the operation of fire hoses, depending on the climate, is divided into: TU1 - tropical and temperate climate of the 1st category of accommodation; U1 - temperate climate of the 1st category of accommodation; UHL1 - temperate and cold climate of accommodation category 1.
- Month and year of manufacture.
Suction type
This type of fire hose is designed to suck up liquids in order to fill fire tanks of both mobile and stationary types. Pump out water using fire pumps and pumps.
When water is sucked in, a negative pressure is created in the hose, which allows filling the pipe. The product itself is relatively flexible, vulcanized rubber coated with fabric for strength.
This type of fire hoses has special heads instead of traditional connecting heads (as on a pressure head). They allow you to connect the product to various devices, such as cranes, pumps and other elements.
The suction pipe is heavy with low flexibility. Products are divided into the following classes:
- B - designed for water intake;
- B - used to work with gasoline, oil, diesel fuel and other fuels and lubricants;
- KShch - for pumping acids and alkalis;
- G - for working with gases;
- P - used for transporting food liquids (dairy products, drinking water, alcohols and spirits).
The length of the product is mainly 4 m, possible diameters from 5 to 20 cm. If the product is used in moderate climatic conditions, then the operating temperatures range from -35 ° C to +90 ° C.
Suction and pressure hoses
This type of fire hoses is used both for sampling fire extinguishing material and for draining it. Sleeves are made according to the tasks that they will perform.
The device of a fire hose of this type consists of a fabric frame, which has internal and external protection of latex or rubber. A metal spiral is built into the body of the product. It gives the sleeve the necessary stiffness and flexibility that is necessary for normal functioning. The edges of the sleeve have special cuffs necessary for connecting the product to various devices.
The diameter of such a sleeve can be from 2.5 to 30 cm, the length of the cuff is from 7.5 to 20 cm. The operating pressure ranges from 0.35 - 1.10 MPa.
Marking of suction and pressure suction hoses
The marking of the suction and combined type hoses does not differ much from the marking of pressure hoses:
- trademark or name of the manufacturer;
- fire conduit class (B, V, G, P, KShch);
- group - suction or pressure-suction;
- diameter in millimeters;
- working pressure in MPa;
- length in meters;
- month (quarter) and year of manufacture;
- GOST;
- mark of technical control.
Any marking is applied in such a way that it can be preserved and read throughout the full term of use of the product.
Sleeve Testing
Testing of fire hoses is an obligatory part in the process of product operation. All of them are strictly subject to the requirements of GOST 51049, and the order for all types of sleeves is the same.
The main purpose of such tests is to check the condition of the product under pressure with rolling. All tests performed must be documented. Such manipulations can only be carried out by a specialist who has a special license and all the necessary equipment.
Tests are carried out upon commissioning of the sleeve, after each use, repair, and, moreover, at the end of the warranty storage period. In case all is well, then the fire hose is used further. In general, the maximum service life is no more than 10 years from the date of manufacture of the product.
Suction and combined fire hoses are tested at least once every six months during scheduled inspections. In addition, tests are carried out if the fire hose did not pass the external inspection after repair.
Tests of pressure hoses are carried out after each use, but not less than once every six months. Testing of this type of hose takes place under pressure to check for leaks.
Test order
Upon receipt or delivery of fire hoses, checks are carried out. During them is determined:
- Length. The sleeve is deployed on a flat surface and measured with a tape measure.
- Inner diameter. For measurements, a step gauge is used.
- Tightness. Most often, the test is carried out by connecting no more than five hoses in one line. One end is connected to a motor pump or a fire hydrant and serves water under operating pressure (or slightly higher). During this time, the sleeve is carefully inspected for leaks and fistulas.
- Completeness. An appropriate form is required (according to GOST 2.601).
- Marking. It should be clearly visible and located from each end of the sleeve at a distance of no more than 0.5 m.
- Packaging. You can store both in a case and without it. It is important that the sleeve is in a flat roll, and its outer end is tied.
If the conduit is in operation, then tests are also needed. The frequency depends on the type and material of the product and is usually indicated by the manufacturer.
- Weight 1 m of the sleeve. To do this, measure the length of the product and lay on the scales. The resulting weight is divided by the length in order to find out the average weight of 1 m. According to GOST R 51049 for hoses with a diameter of 5.1 cm, this value should be 450 g / m, and for 6.6 cm - 550 g / m.
- The thickness of the internal waterproofing. It should be no less than 0.3 mm.
- Relative increase in diameter and length. In the first case, an increase of 10% is allowed, and in the second - by 5%.
- Water consumption for hydration. This indicator is important only for percolated sleeves.
- Bursting pressure. Ideally, it should be 2 times higher than the working one.
- The relationship of internal waterproofing with the frame. The strength of the latex coating should correspond to 7 N / cm, and rubber - 10 N / cm.
Wear-resistant sleeves are checked not only for tightness, but also for heat resistance, oil resistance and abrasion resistance.
Maintenance of suction and combination hoses
Maintenance of suction and pressure-suction pipelines involves the following steps:
- Thawing (soaking). After use in the winter, the hose needs to thaw completely in a warm place. For this, a bathroom with water is often used. In addition, the same bathroom can be used to soak contaminated water conduits.
- Washing. After soaking, the sleeves are washed by hand, while using a brush or special equipment.
- Visual inspection. Such an inspection is carried out after each use, but not less than 1 time per month. If the water pipe is stored in a warehouse, then the check should be at least 1 time per year. The purpose of the inspection is to identify internal or external damage and defects, as well as to check for markings. From this procedure depends on whether the sleeve will continue to be used, or whether it needs repair and testing.
- Tests If the sleeves are in operation, then the procedure is carried out once every six months with a scheduled inspection. For hoses stored in a warehouse, the test is carried out at the end of the warranty storage period.
- Drying. In winter, the hoses are dried in a sleeve dryer, and in the summer in the fresh air, but always in the shade. The temperature should not be higher than 50 ° C.
- Repairs. In the presence of visible damage and if the sleeves have not passed the tests, repair is made. If it is mechanical damage or loss of sealing, then repair can be carried out in two ways - vulcanization and patchwork. If the connecting heads are damaged, they are simply replaced with a clamp or by the method of fastening.
- Storage. Only clean water pipes can be stored. Products must be protected from ultraviolet radiation, direct sunlight and heat. In addition, oil, gasoline, vapors, acids and other substances that can destroy rubber should not get on the sleeves.
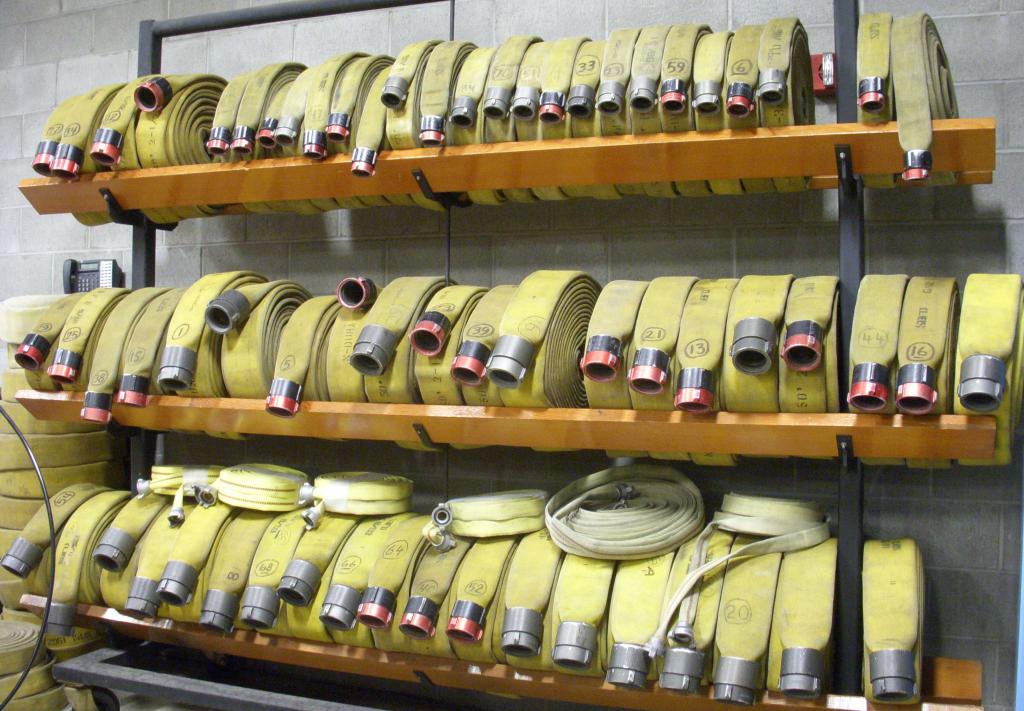
Maintenance of pressure hoses
The following maintenance is provided for pressure hoses:
- Soaking (thawing). Be sure to thaw the sleeves in a warm place or use the bathroom with water.
- Washing. Sleeves are cleaned either manually or using special equipment.
- Visual inspection. It is carried out necessarily at least 1 time per month, subject to storage - at least 1 time per year. Check for any defects and damage, as well as for mandatory marking. Based on the inspection, a decision is made to repair, test or continue using it.
- Test. It is carried out after each use, but not less than 1 time every six months. All results are entered in a special form.
- Drying. Dry pressure hoses are dried in dryers (chamber, tower or others), where there is a heater or other similar devices. If there are no bag dryers, then there are two ways to dry: on the street at +20 ° C and higher with a humidity of not more than 80% or in a very heated room with installed heating devices. With any method, drying should be no more than 24 hours.
- Rolling and rolling of fire hoses. When the conduits are completely dry, they are rolled into a double or single roll. For this procedure, you can use a special device. The frequency of rewinding of the fire hoses must correspond to the documentation for each pressure type hose separately.
- Repairs. Only clean and dried sleeves may be repaired. If the frame is damaged, then repairs are carried out either by vulcanization, or using special adhesive compounds.
- Storage is permitted only for clean products. Do not store sleeves near appliances that could harm rubber. The conditions must comply with the requirements specified in the documentation for each sleeve.
Finally
Fire safety is very important. Therefore, the presence of hose equipment and fire lines is mandatory for each room. This allows you to quickly and efficiently extinguish the source of fire and avoid its spread. Fire hoses differ in both material and purpose. In addition, it is important to regularly check the condition of the product to avoid unforeseen situations.