Figured glass cutting is a rather complex process that requires effective technology. The planes obtained by this method are widely used for glazing windows, making shelves, partitions, decorating rooms and much more. Glass of complex relief - these are elegant details on doors, facades, kitchen and other furniture.
Types and methods of cutting
Depending on the complexity of the work that is being done, the lines can be divided into the following categories.
- Simple straight lines, in which you can get figures such as a rectangle, square, trapezoid, rhombus with certain dimensions along the length and width.
- Curly - thanks to them you can get curvilinear shapes that can be rounded, wavy and with various internal cutouts. With this canvas, you can realize the most incredible design ideas in unexpected combinations.
Cutting mirrors and glass can be carried out in the following ways.
- Manual - performed with a special circular knife (glass cutter). This technique is considered the cheapest compared to others, but the cultivated area can only be small. For example, glass furniture inserts, countertops and shelves.
- Automatic - carried out on special equipment, which allows to guarantee high accuracy and speed of execution. Glass cutting and processing in this case takes place efficiently, quickly and in large volumes.
- Sandblasting is the most common. The work is carried out by abrasive particles, which are released under high pressure onto the product contours not protected by a film. The technology helps to produce complex shapes with high cut quality and accuracy. In this way, it is possible to decorate the glass itself and apply various drawings, images and patterns to it.
- Hydroabrasive is a proven and old technique, which consists in feeding water along with abrasive particles to the canvas. Using a thin trickle, both simple and figured glass cutting is performed with excellent edge quality and high precision. This method allows you to process a lot of material with a minimum amount of scrap.
- Laser - is considered a modern technology with which you can get a high-quality product with a smooth cut that does not require additional processing. Using this method, filigree figures of varying complexity are performed.
Instruments
There are many devices with which curly cutting of glass is carried out, and each has its own advantages and disadvantages.
- Diamond glass cutter - a tool used for a long time. He successfully copes with professional tasks and is suitable for domestic purposes. It is arranged as follows: a small natural diamond is fixed in a special holder with a handle. Such a tool is suitable for material with a thickness of not more than 10 mm.
- Oil - able to cut the canvas up to 20 mm thick. Some of the models sold have movable heads, which are indispensable if curly glass cutting is needed.
- The device with an artificial crystal - differs from the first only with the used cutter. Well close to natural, much cheaper, but less effective. The thickest surface that lends itself to it is 5 mm.
- Roller - is also an effective and widespread device, consisting of a roller made from a very hard alloy. It is attached to the handle, models can count from 1 to 6 circles, designed for a material of not more than 4 mm.
- Glass cutter-compass, it is suitable for those cases when it is necessary to prepare round or oval figures.
- Quick cutter for glass - used for high-speed cutting. It has an oil head, which lubricates cutting lines with a special mixture. The tool has a special scale on which you can set the cutting width, so that the work is carried out without problems.
Advantages of the waterjet technique
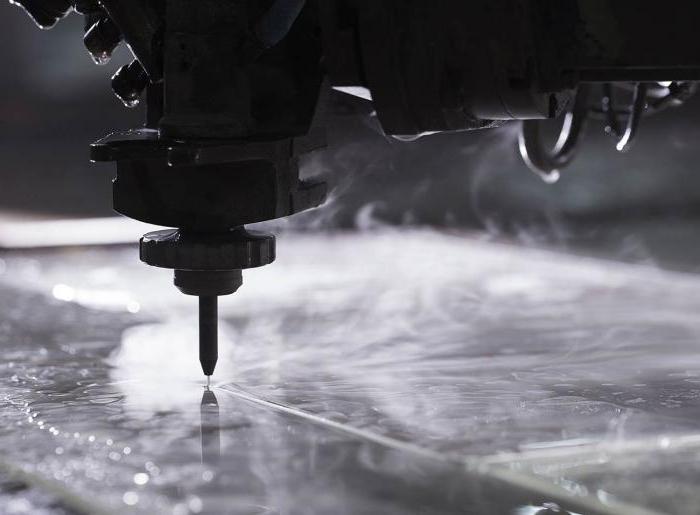
- There is no heat treatment of the material (the cutting zone is heated to 60β90ΒΊ). Due to this, in the process the glass does not deform, does not burn and does not melt. The heat that is released in the process is carried away with the water.
- A wide range of processed materials (granite, marble, stone, steel, plastic, wood, rubber and ceramics).
- The thickness of the glass that water can cut, varies from 0.5 mm to 195 mm.
- Cut in a circle of any curvature. The method helps to carry out the cutting of the material along the necessary path, including corners, holes, oblique lines and various radius curves.
- Economical material consumption. The width of the cut is not more than 0.5 mm.
- You can do without subsequent edge processing. It does not need further grinding and polishing.
- Ecological cleanliness of the process. Thanks to the water jet there is no dust, crumbs do not pollute the air. It also helps to save on the protective equipment required by other methods.
- Full automation of the process.
Laser cutting
With such a tool, it is easy to perform operations of any complexity in a short time. The human factor in the process is minimal, as the machine does all the work. Using the positioning sensor, you can cut with surgical precision. You should not worry about errors at all, as they are absent. Designed to work with window, red-hot and hardened cloth, as well as with mirrors. Moreover, the parameters and thickness of the glass do not matter at all. Equipment copes with tasks of any complexity.
DIY cutting
If you want to save, all the work can be done at home and on your own.
- Initially required to prepare the surface. The table should be perfectly flat, as the smallest tubercle can cause marriage.
- Next, you need to process the plane itself. It is wiped with a special degreasing compound, after which it is well dried.
- Then the so-called cutting of glass is carried out. It is worth noting that if you plan everything correctly, you can get several finished products from one glass.
- After everything is completed, a special tool for work is obtained. It has a handle, and the cutting element itself is made of very hard material.
- How to cut glass at home is already understandable, but it is also considered important that after the procedure it is necessary to grind all sharp edges. If the material was prepared to be inserted into the frame, this can not be done.
- To work with thick surfaces, it is necessary to use special fluids that simplify the tool and, in turn, help to penetrate it deeper.
If you perform all the steps correctly, then problems with the work should not arise at all.
Figured Mirror Cutting
Various forms of this material can be prepared as a special device, or as a home-made "glass-cutting pencil" made of charcoal. The prepared powder is mixed with gum arabic (a clear, viscous liquid secreted by acacia forms an adhesive solution in contact with water). The resulting dough is rolled into large sticks and thoroughly dried.
Before starting work, the edge of the glass is filed with a trihedral file. Then the pencil is ignited and they are touched to the processed end. The hot end lead in the necessary direction. The cracks that have formed, the mirror easily bursts. It is important that all movements must be performed exclusively on the front of the surface.
Further processing
It is done only if the edge of the glass is visible on the final product, since it should look aesthetically pleasing.
Grinding is necessary to improve the surface. This helps to make the plane not only decorative, but also safe for humans. The operation is carried out using abrasive materials. After this procedure, the surface takes on a matte and slightly rough look with a greenish tint.
The second step is polishing. During this procedure, only soft fibers are used. After it, the edges become more transparent and smooth. It is carried out using special equipment for easy handling.
Application
Figured glass cutting is widely in demand where sophistication, nontriviality and decorativeness are required:
- in advertising production - complex products attract more attention;
- in the manufacture of souvenir products - such figures are very popular and will decorate any room;
- in the furniture industry and in design work.
Useful Tips
- If there is a need to make a hole or carefully cut the glass, and then give it a round shape, you only need specialized tools and knowledge of your craft.
- For any work, thoroughly wash and degrease the surface with acetone or gasoline and rinse with plain water. If the surface cannot be cleaned with liquid, you can take a slice of potatoes, rub the product with it and thoroughly wipe it with a dry rag.
- At the place where you need to make a hole, no matter what the thickness of the glass, you need to pour a handful of sea sand, make a hole in it of the desired diameter, and then pour molten tin or lead into the hole and let it cool. Then you need to remove the solder and remove the remaining sand.
- Before starting cutting, glass is necessarily degreased where the glass cutter passes. Then the sheet is attached with a suction cup and a metal rod is installed.