In some houses, the owners, in order to provide themselves with drinking water, make wells, and pump stations are installed in them. And now they can break at the most inopportune moment. Moreover, with a breakdown, the house is completely left without water - not very nice, especially in the summer heat. In the article you will find out why the pumping station does not gain pressure or does not turn off in a timely manner. All the reasons why this happens will be discussed below.
The main causes of breakdowns
Immediately it is worth considering one malfunction - the pump works constantly and does not turn off. In the event that the pumping station builds up pressure and does not turn off, the unit operates continuously, the following reasons can be considered:
- The water level dropped significantly.
- The filter mounted on the inlet pipe is clogged.
- The integrity of the entire system is broken.
- The ejector is clogged.
- One or more pump parts broke.
- The inlet of the pressure switch is clogged or it is completely out of order.
In the course of the article, we will consider all these malfunctions in more detail.
Water level drop
One of the most common reasons why the pump does not work and there is no pressure in the pipeline system is a significant drop in water level. Especially when water is taken from a shallow well. This is a normal phenomenon, it is associated with a change in temperature. If there is a small amount of liquid, then air plugs will begin to appear in the system. You can see that the water cycle in nature has been severely disrupted: the lakes begin to dry up, the rivers become shallow, therefore, the groundwater goes to great depths.
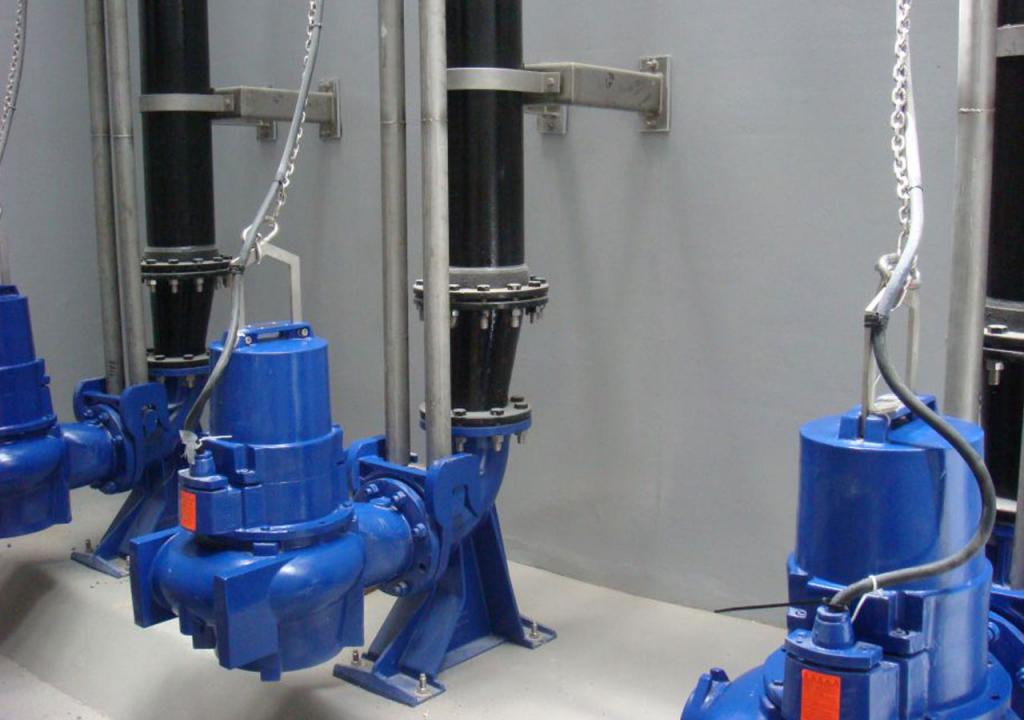
If the pumping station slowly builds up pressure, then most likely the catchment is at a shallow depth (up to 10 meters). In the event that the pump does not take water from anywhere, it is necessary to make a large well. If the water level has fallen directly in the station, you will have to unscrew the bolt provided for by the design and add water through the hole formed. After this, the station must be restarted and wait for the pressure to increase. To speed up the process, you must repeatedly turn off the pump and add more water.
If the filter is clogged at the input
It is necessary to take into account the fact that in the water there is a large number of small particles - silt, sand, clay. They wear out the elements of the pump. The filter, which is placed on the inlet pipe, allows you to accumulate all the garbage in yourself. In the end, this helps to increase the resource of the entire system. But if you do not change the filter in a timely manner, no liquid will enter the pump.
If the pumping station gains pressure for a long time, does not turn off, the cause may be a break in the inlet pipe or a clogged filter. In the latter case, you must either clean the filter or install a new one. After this, you need to add fluid and start the station.
Air leaks
It should be noted that the level may fall in the station. At the same time, water will begin to leak in the “weakest” place. In some cases, the leak is visible to the naked eye, but sometimes, to find it, you need to examine all the hidden places. It is worth noting that if the pumping station does not gain pressure, the cause may be covered in pipeline leaks. The examination should be carried out as carefully as possible. First, inspect the nozzles at the joints directly at the pump station. Then you need to move on to the rest.
If the pipes find cracks, then they need to be sealed with a special adhesive tape. But note that this measure is temporary, it is recommended to replace the damaged area as soon as possible. If a leak appears on the threaded connection, turn off the pump and add a tow. If necessary, install a new rubber ring or gasket. In particular, this may be relevant in the manufacture of the station from old worn pipes. Water can seep from cracks in the flange that is adjacent to the hydraulic accumulator. In this case, you will need to dismantle the element, weld the hole and install it back.
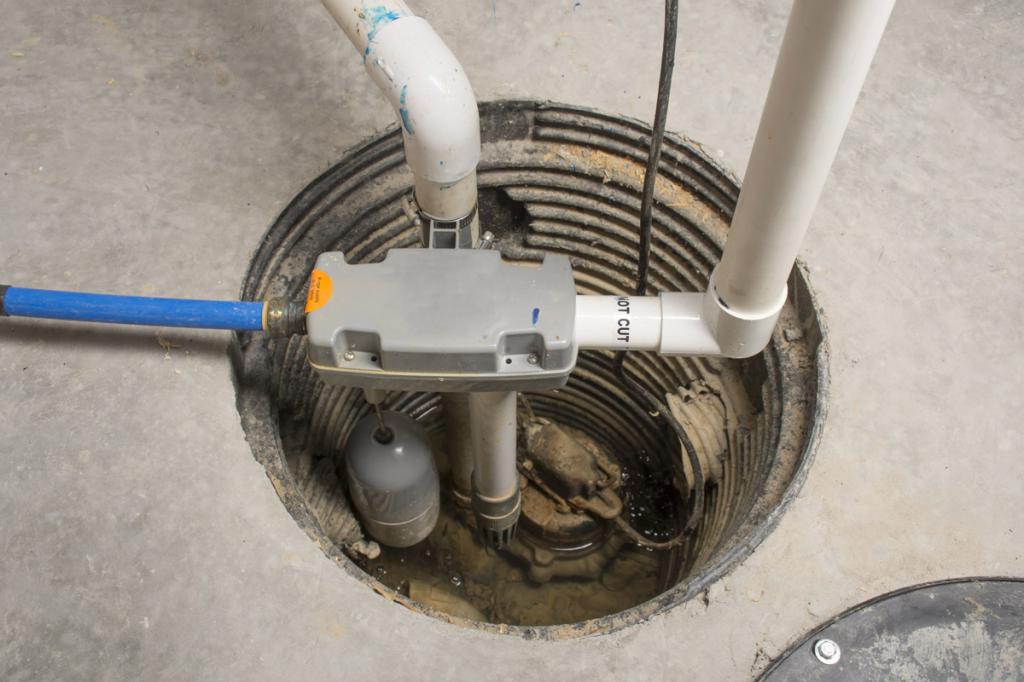
By the way, threaded connections need to be sealed with the help of the thread “Tangit Uni-Lock”. This sealant is easy to use. Leakage may occur if the check valve installed on the supply pipe breaks. As a result, the device will not be able to retain water, since there is a large accumulation of dirt. In this case, the work boils down to the fact that the pump pumps water to the lowest level, after which it is switched back on. You can observe the continuous operation of the station even at night, when there is no water flow. And if the pump will constantly work, it will quickly fail.
Destruction of the gasket or ejector
If simple pumps get liquid from a depth of not more than 10 meters, then the pumping station is able to lift water from 45 meters. Therefore, in order to improve the water supply system, two pumps are used, as a result of which the efficiency can be increased by about 35%. And if the pumping station does not gain pressure, the reasons may lie in the internal elements.
Damage to the ejector is the most serious. During repair, all components must be cleaned and replaced. Remove all harmful impurities, sand, dirt, and then lower it back into the well.
Working wheel
If the pump works without stopping, then all its components wear out much more. In the power unit are working elements. In particular, the impeller. If sand or other abrasive material acts on it, it will begin to wear out quickly. The impeller is often made of plastic. But it is recommended to choose such designs in which it is made of metal.
The impeller is destroyed by the action of sand and other abrasives. If such substances entered the system, then the fault is the one who drilled the well. The fact is that, most likely, the sand trap mesh was incorrectly selected. The second option - there is no filter element at the input.
Relay fitting
And now about the reasons why the Jumbo pumping station is not gaining pressure to the desired level. The problem may be in the electrical part. For example, in the breakdown of the relay through which the motor turns on. The settings of the automatic system can be lost when the fluid level in the well decreases. In this case, air enters the intake pipe. To get rid of the breakdown, you need to lower the pipe below, then pour water into it and turn on the station.
Often a relay breaks. If the spring regulating the work of the contact group is damaged, the pumping station stops turning on and off. The most common damage is the formation of oxides and rust on the work surface. To make repairs, you need to carefully disassemble the relay and clean all the contacts. In this case, penetrating grease of type WD-40 can be used. But it is better, of course, to put a new relay.
To adjust the pressure, you need to rotate the special nuts clockwise or counterclockwise. It all depends on whether you need to increase or decrease pressure. On the device there are designations - "+" and "-". If the connection is clogged, the relay will start to work incorrectly. To eliminate the breakage, the nozzle must be completely removed and the hole cleaned of dirt.
Why no pressure?
But for what reasons does the Gileks pumping station still not gain pressure in the system? Private sectors often use individual sources of water. Therefore, it is necessary for him to need a pump or even a station. Such a system allows you to lift water from the well and transport it through pipes to the consumer. Next, we will consider how to properly eliminate all the causes of this phenomenon.
But is it really important to maintain the nominal pressure in the system? Let's take a brief look at the principle of operation of the station in order to put everything in its place. Knowing the principles of work, you can quickly find and fix breakdowns. The centerpiece of the station is the pump. It is with its help that water rises and is fed into the system. The power of the pump is high, but the “flair” is also not bad. The problem is that the pump constantly turns on and off, and this reduces its resource. It is possible that all the elements of the pump itself will be in good condition, but the electric motor will fail.
To ensure stable and safe operation of the pump, a so-called hydraulic tank or hydraulic accumulator is included in its kit. In fact, it is he who is responsible for ensuring that the system has pressure. This is a kind of liquid storage. The scheme of work is approximately the following:
- A pump pumps water from a well.
- Water enters the accumulator.
- The pump switches off after the tank is full.
- Water to consumers comes from the tank.
- When the level drops to a critical level, the pump is turned on and the tank is filled to the maximum level.
Causes of station failures
But why does the pumping station gain pressure for a long time, and sometimes do not even bring it to its normal value? At the same time, it is audible that the pump is operating constantly, water is going to the tank, but is not gaining working pressure.
You can fix such a breakdown yourself, but first we look at the most common causes of such a malfunction:
- Small power electric pump motor. In this case, you can blame the one who designed the system. The second option - after the installation of the pumping station, there was a change in communications, the connection of new consumers. In order to correctly determine the electric motor power, it is necessary to take into account the diameter of all pipes, the number of people living in the house, the purpose of water consumption, the depth of the hole. It is also recommended to buy a pump whose power is 25% more than the calculated one.
- Low voltage in the power grid - this can often be observed in villages located away from cities. In this case, the pressure does not develop by the pump, therefore, the pressure cannot increase. In other words, you will hear how the pump works, water will flow to the tank, but the electric motor will not turn off. There are two ways out - to install a more powerful pump or to connect a good voltage regulator.
- Incorrect pressure setpoint switch setting. This component of the system monitors the operation of the entire station - it is he who sets the lower and upper pressure. It is possible that the maximum value is incorrectly set. To lower the threshold, you need to unscrew the nut, which is located on the smaller spring. In this case, the maximum pressure decreases, the station starts to shut down in a timely manner. Please note that the nut, which is located on a larger spring, reduces both values ​​at once - both maximum and minimum. But the range does not change.
- It may be the reason that the pump runs continuously, and the complete wear of all its components. This often happens with centrifugal structures. The reason is that the impeller rotates very quickly, passes liquid through itself. At the same time, abrasive materials also pass through the pump. And they work like sandpaper. As a result, the pump works, but the right amount of water does not enter the hydraulic tank. To repair, you must either put in a new impeller or completely replace the entire element. In order not to collapse the impeller, you need to purchase a pump with a filter in the working chamber.
Leaks in the system
If the pumping station is not gaining pressure well, the reason may lie not only in it, but also in the pipeline. This breakdown often occurs in structures. At the same time, the pump is functioning, water enters the tank, but not completely. But the fluid does not reach the final destination. And the pressure build-up does not occur, the pump pumps continuously, without stopping. If you find a leak on the pipe, you need to cut and replace the area. In case of leakage from the thread, it is necessary to wind sealing material on it.
Leaks may also appear in the check valve. At the same time, water begins to flow back, the pump does not pump to maximum pressure. The electric motor works constantly. The most obvious sign of such a breakdown is the spontaneous switching on of the pumping station, even when all consumers are completely disconnected.
The destruction of the elastic membrane in the hydraulic tank leads to the fact that it is not possible to adjust the pressure. The pump is functioning, the maximum pressure is almost reached, but then abruptly turns off the motor. When the tap is opened, the pump starts working again. To eliminate the breakdown, you need to check the spool, through which air enters the hydraulic tank. Click on the pin and observe its behavior. If water starts to leak, then this indicates a rupture in the membrane. Two ways out - replacement of the accumulator or membrane.
Self-priming pump: why breakdowns occur?
In order for the water supply system to work stably even when used in shallow wells, so-called self-priming pumps are used. When pressure drops in the tank and water supply, airway and main impeller airing can occur. But why does air enter the system? Let's try to figure this out:
- One of the main reasons is a sharp drop in the well water level. In this case, air enters the pump hose. To eliminate the malfunction, you need to check the water level in the well, and then lower the intake hose a little lower.
- Seal leakage between intake hose and pump inlet. The way out is tightening the nuts, strengthening the gasket.
- It also happens that at the time of start-up, the pump contained not only water, but also air. The pumping station gains pressure for a long time, and often, in general, cannot lift water from the well. Only pouring water and restarting the entire station will help. Sometimes they resort to squeezing the air plug out of the pump. To do this, a tee is connected to the suction part of the pipe, water is poured into it from the tank, which is installed above the ground. The pump must be turned on.
Does not pump water
Now let's talk about why the pumping station is not gaining the pressure necessary for the normal functioning of the system. We have already considered many reasons, indicated the main actions, and now we get closer to the elimination algorithm. If the station does not pump water at all, does not even turn on, then you need to perform several actions:
- Check if there is any voltage on the mains. If there is, then you need to make sure that it is supplied to the pressure control relay and the electric pump.
- If there is voltage in the network, you need to make sure that the circuit breaker installed for protection in the switchboard is turned on and is in working condition.
- It is also recommended to check the integrity of all connecting wires. When the machine is turned off, you need to make a “call” of all wires with a multimeter. Also make sure that the contacts are intact and not burnt.
- If there is voltage, the contacts are in excellent condition, the relay is activated, then most likely the problem lies in the electric motor itself. It is possible that the terminals have burned. But most often, of course, the winding burns out. If so, the smell of burning insulation will be present. It is better not to do self-repair of an electric motor, entrust it to specialists.
The pump turns on, water does not swing. Surface pumps
Consider a few more failures, after which the pumping station stopped to build up pressure. The motor turns on, but the water does not swing. The reasons can be any, it all depends on the type of station. So, standard turretless systems with surface pumps do not pump water in the presence of such breakdowns:
- There is no water in the pump or inlet pipe. Before starting up for the first time, it is recommended that the pump and pipe be filled with water. Otherwise, pumping water out of the well will fail. If you poured water, but then suddenly it turned out that it was not in the pipe, then this indicates that it left through the joints or the return valve.
- Lack of tightness in the suction pipe, air entering the pump. If there is no tightness, air will be sucked in. To make sure that such a malfunction is absent, you need to wipe all connections dry and carefully inspect them.
- Clogged filter or return valve. It is possible that the strainer clogged completely. Have to clean it or put a new one. If the blockage is repeated again and again, then you need to clean the well. Too much sand, silt, clay has accumulated in it.
- Lowering the water level in the well.That is why the pumping station does not gain the required pressure in most cases. This happens in the summer when the air temperature rises. If the water level drops to a mark lower than the inlet valve, then you need to lower the pipe deeper.
- Impeller sticks after a long downtime. The electric motor refuses to rotate the impeller. To fix the breakdown, turn off the engine and try to turn the axis with the impeller on your hands. If necessary, disassemble the electric motor, the impeller, and then lubricate all the elements.
- . , . – . .
- . .
- , . . .
, , . , , .
, .
If the pump station does not build up pressure, the cause of the breakdown may lie in the pump itself. Make sure that it is working, only after that you can proceed to further manipulations:
- The connection between the pump and the pipe is broken. It happens that the pipe is disconnected from the check valve or pump. May loosen the clamp on the joint. In this case, you can observe the water fountain in the well. To eliminate it is enough to connect the pipe securely.
- A pipe break between the house and the well. If this happens, you will only have to replace the damaged section.
- Lowering the water level in the well is the same as in the previous case. It is necessary to check the level, and if it really fell, then lower the entire structure down.
- Reducing the voltage in the mains is also dangerous for a pumping station with a deep motor. Spend some money and put a source of voltage stabilization.
All these breakdowns can be found at most modern stations. You need to know why the Gileks pumping station is not gaining pressure. And then it will be much easier to exploit it.