Nitriding technologies are based on changing the surface structure of a metal product. This set of operations is required in order to endow the target with protective characteristics. However, it is not only physical properties that increase nitriding of steel at home, where there is no possibility for more radical measures to endow the workpiece with improved characteristics.
General information on nitriding technology
The need for nitriding is determined by the maintenance of characteristics that allow to endow products with high-quality properties. The main share of nitriding techniques is performed in accordance with the requirements for thermal methods of processing parts. In particular, grinding technology is widespread, thanks to which specialists can more accurately adjust the parameters of the metal. In addition, protection of areas that are not subject to nitriding is allowed. In this case, coating with thin layers of tin can be applied by means of a galvanic technique. Compared to deeper methods of structural improvement of metal characteristics, nitriding is the saturation of the surface layer of steel, which to a lesser extent affects the structure of the workpieces. That is, the basic qualities of metal elements associated with internal characteristics are not taken into account with nitrided improvements.
Varieties of nitriding methods
Approaches to nitriding may vary. Usually, two main methods are distinguished, depending on the nitriding conditions of the metal. These can be methods to increase surface wear resistance and hardness, as well as improve corrosion resistance. The first option is characterized in that the structure is changed against the background of a temperature of about 500 ° C. A reduction in nitriding is usually achieved by ion treatment, when a glow discharge is excited through anodes and cathodes. In the second embodiment, alloyed steel nitriding is performed. This type of technology provides for heat treatment at 600-700 ° C with a process duration of up to 10 hours. In such cases, processing can be combined with mechanical action and thermal finishing of materials, in accordance with the exact requirements, to the result.
Exposure to plasma ions
This is a method of saturation of metals in a nitrogen-containing vacuum, in which electric smoldering charges are excited. The walls of the heating chamber can serve as anodes, and directly processed workpieces act as the cathode. In order to simplify the control of the layer structure, correction of the technological process is allowed. For example, the characteristics of current density, degree of rarefaction, nitrogen flow rate, levels of adding pure process gas, etc. can change. In some versions, plasma nitriding of steel also involves the addition of argon, methane and hydrogen. In part, this makes it possible to optimize the external characteristics of steel, but technical changes nevertheless differ from full alloying. The main difference is that deep structural changes and corrections are made not only on the external coatings and shells of the product. Ion treatment may affect the complete deformation of the structure.
Gas nitriding
This method of saturation of metal products is carried out at a temperature level of about 400 ° C. But there are also exceptions. For example, refractory and austenitic steels provide a higher level of heating - up to 1200 ° C. Dissociated ammonia acts as the main saturation medium. Structural deformation parameters can be controlled through the gas nitriding procedure, which involves different processing formats. The most popular modes are considered two-, three-stage formats, as well as a combination of dissociated ammonia. Less commonly used modes that involve the use of air and hydrogen. Among the control parameters that determine the nitriding of steel by quality characteristics, one can distinguish the level of ammonia consumption, temperature, degree of dissociation, the consumption of auxiliary process gases, etc.
Electrolyte Solutions
As a rule, anode heating technology is used. In fact, this is a type of electrochemical thermal processing of steel materials. This method is based on the principle of using a pulsed electric charge, which passes along the surface of a workpiece placed in an electrolyte medium. Due to the combined effect of electricity charges on the surface of the metal and the chemical environment, the polishing effect is also achieved. With this treatment, the target part can be considered as an anode with a positive potential from electric current. At the same time, the cathode volume should be no less than the anode volume. Here, some characteristics should be noted, according to which the ion nitriding of steels converges with electrolytes. In particular, experts note a variety of modes of formation of electrical processes with anodes, which also depend on the connected electrolyte mixtures. This makes it possible to more accurately regulate the technical and operational qualities of metal billets.
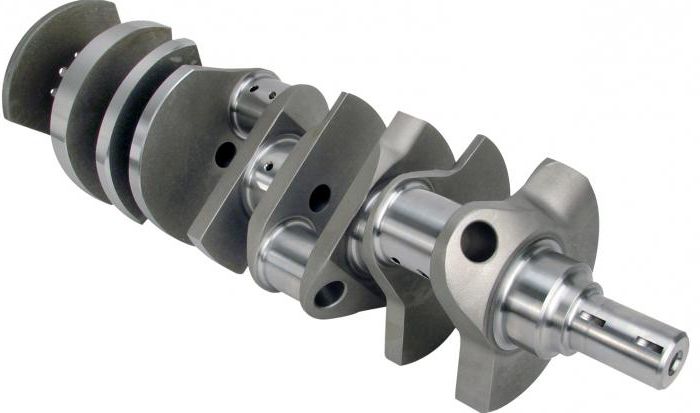
Catholic nitriding
The workspace in this case is formed by dissociated ammonia with the support of a temperature regime of the order of 200-400 ° C. Depending on the initial qualities of the metal billet, the optimum saturation mode is selected, sufficient for the correction of the billet. This also applies to changes in the partial pressure of ammonia and hydrogen. The necessary level of ammonia dissociation is achieved by controlling the pressure and volume of gas supply. At the same time, unlike classical methods of gas saturation, Catholic nitriding of steel provides for more gentle processing modes. Typically, this technology is implemented in a nitrogen-containing air environment with a smoldering electric charge. The anode function is performed by the walls of the heating chamber, and the cathode by the product.
Structure deformation process
Practically all methods of saturating the surfaces of metal billets are based on connecting the temperature effect. Another thing is that additionally electric and gas methods of correction of characteristics can be involved, changing not only the external, but also the external structure of the material. Mostly technologists are seeking to improve the strength properties of the target and protect against external influences. For example, corrosion resistance is one of the main tasks of saturation, in which nitriding of steel is performed. The metal structure after treatment with electrolytes and gaseous media is endowed with insulation that can withstand mechanical and natural damage. The specific parameters of the structural change are determined by the conditions for the future use of the workpiece.
Alternative technology nitriding
Along with the nitriding technique, the external structure of metal billets can be changed by cyanidation and cementation technologies. As for the first technology, it is more reminiscent of classical alloying. The difference between this process is the addition of carbon to active mixtures. It has significant features and cementation. It also allows the use of carbon, but at elevated temperatures - about 950 ° C. The main goal of such saturation is to achieve high operational hardness. At the same time, both cementation and nitriding of steel are similar in that the internal structure can maintain a certain degree of viscosity. In practice, such processing is used in industries where the workpieces must withstand increased friction, mechanical fatigue, have wear resistance and other qualities that ensure the durability of the material.
Benefits of Nitriding
The main advantages of the technology include a variety of workpiece saturation modes and versatility of use. Surface treatment with a depth of about 0.2-0.8 mm also makes it possible to maintain the basic structure of a metal part. However, much depends on the organization of the process, in which nitriding of steel and other alloys is performed. So, in comparison with alloying, the use of nitrogen treatment is less costly and is allowed even at home.
Disadvantages of nitriding
The method is focused on external refinement of metal surfaces, which leads to a limitation on protective performance. Unlike carbon treatment, for example, nitriding is not able to adjust the internal structure of the workpiece in order to relieve stress. Another disadvantage is the risk of negative effects even on the external protective properties of such a product. On the one hand, the process of nitriding steel can increase corrosion resistance and moisture resistance, but on the other hand, it will minimize the density of the structure and, accordingly, affect the strength properties.
Conclusion
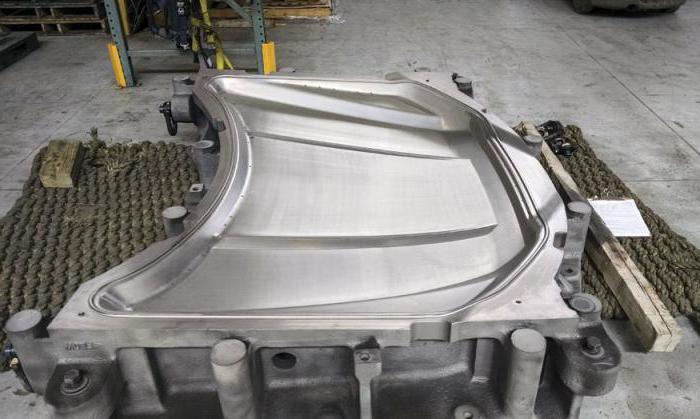
Metal processing technologies involve a wide range of mechanical and chemical effects. Some of them are typical and are calculated on the standardized endowment of blanks with specific technical and physical methods. Others focus on specialized refinement. The second group includes nitriding of steel, which allows the possibility of almost point refinement of the outer surface of the part. This modification method allows you to simultaneously form a barrier against external negative influence, but at the same time not to change the basis of the material. In practice, such operations are subjected to parts and structures that are used in construction, machine and instrument making. This is especially true for materials that are initially subjected to high loads. However, there are strength indicators that cannot be achieved due to nitriding. In such cases, alloying with deep full-format processing of the material structure is used. But it also has its drawbacks in the form of harmful technical impurities.