Welding metal products and structures is a complex process that can be organized in various ways. The traditional method involves manual operations. This is a time-consuming, low-cost method. A more modern approach is semi-automatic welding, which facilitates the tasks of the master and improves the quality of the seam.
Technology Description
The principle of operation of welding semiautomatic devices is quite simple. In the process, the welding gun is directed to the target zone, after which the workpiece begins to melt from the heat of the formed arc. Unlike other welding methods, in this case, the wire can perform the function of a conductive electrode and the task of the filler.
As a means of protecting the working area, semi-automatic welding technology provides for the formation of gaseous media - in particular, which do not allow oxygen to enter the treatment zone. But later, the mode in which the process occurs without gas will be considered. Conversely, other protective media and materials may be added. So, to minimize the spraying of metal droplets due to moisture absorption in the working area, silica gel or copper sulfate, placed in a desiccant, is used.
Ultimately, the operator can rely on the following benefits from the use of technology:
- High degree of protection of workpieces.
- Convenience in working with equipment - the master can perform operations from almost any position, since there are no restrictions in the direction of welding.
- The seam is smooth and with a minimum content of slag.
MIG and MAG welding methods
In specifications and normative documentation, semiautomatic welding using wire and gaseous media is designated in this way. Steel and aluminum alloys can be targeted billets, although in practice the technology has a wider range of uses. How is semi-automatic MIG welding different from the MAG method? In fact, the difference goes by the type of gas used to protect the working area. For example, MIG welding uses inert gases like argon and helium, while MAG works with active nitrogen and carbon dioxide.
As practice shows, MAG provides a better and more reliable seam compared to the MIG effect, although much depends on the skill of the performer. If we compare both methods with the formats MMA and TIG, then we can talk about the balance of semi-automation. It gives optimal performance with proper weld quality, but itβs worthwhile to turn to alternative methods specifically for delicate high-precision operations or providing ultra-strong joint structures.
Welding modes
Different conditions and technical goals will require the use of certain processing parameters. Depending on the operational tasks and equipment settings, the following modes of semi-automatic welding are distinguished:
- Short Arc. At low current and with the support of short consecutive faults under conditions of low current strength up to 200 A, the transfer of drops of the melt is carried out. In the course of operation, a wire with a thickness of 0.8-1.2 mm is used.
- Spray Arc. The operation is performed at a current strength of 200 A, which ensures higher penetration of droplets into the melt. The diameter of the wire is more than 1 mm. This mode is suitable for thick-walled workpieces.
- Pulse Arc. At low current, this welding format provides high melting speed with a small amount of melt spray. Ideal for stainless steel and aluminum, but only if they are small in thickness.
- Pulse on Pulse Arc. The mode allows to obtain a strong seam with a smooth surface due to the regulation of temperature and current level.
Especially for work in low temperature conditions, a special mode of semi-automatic welding of MIG with soldering elements is also used. The connection of parts in this case occurs against the background of the addition of the melt from the solder material. This method is used in auto repair shops when performing body repair.
Shielding-free welding
Regulation of the working environment gives the operator a lot of advantages - both in terms of safety and as a means of improving the quality of the seam. But there are conditions in which the use of gaseous media can in principle be ruled out. For example, semi-automatic welding in a carbon dioxide environment can effectively solve the problems of processing steel billets, but due to the need to connect a cylinder with a gearbox, the safety requirements, which can be imposed and restrictions, are significantly increased. In this regard, it is appropriate to identify two main ways to use gas-free MIG-MAG technology:
- Welding with flux wire. The consumable is brought by a support to an electric arc and, as it burns, covers the molten bath. The method is environmentally friendly and safe, but can only be applied to soft non-ferrous metals.
- Cored wire welding. A consumable based on a mixture of silicate and silicate is used, which is rejected by the melt and forms a protective film on its surface. The coating performs the task of a barrier to oxygen, replacing the same carbon gas. This method also has a number of limitations associated with low thermal arc power.
Applied Equipment
The semiautomatic device acts as the main and most responsible tool in the working process - it is also a rectifier or inverter that provides power to the burner. These are electromechanical devices, due to which the process of melting the electrode with its supply to the weld pool is performed. In particular, the parameters of the apparatus for semi-automatic welding will determine the range of wire feed speed and the stability of its movement in principle. There are models of inverters for domestic and professional use (for 220 V and 380 V, respectively) with monoblock and modular designs. Pay attention to the configuration of the connectors for connecting the same burner, but the most important thing in choosing is the direct operating parameters of the equipment.
Characteristics of devices
For simple household tasks in a garage or a home welding workshop, you can use low-power devices of 4-5 kW with a maximum current of 90-120 A. Such models are quite capable of working adequately with workpieces with a thickness of 1.5-2 mm, while saving energy. The professional segment represents models with power up to 14 kW and above. The supported current strength of such equipment can reach 350 A. For what tasks is this type of equipment used? Productive semi-automatic welding has good versatility, which is reflected in the ability to service metals such as titanium and nickel. The thickness of the workpiece may be 10 mm.
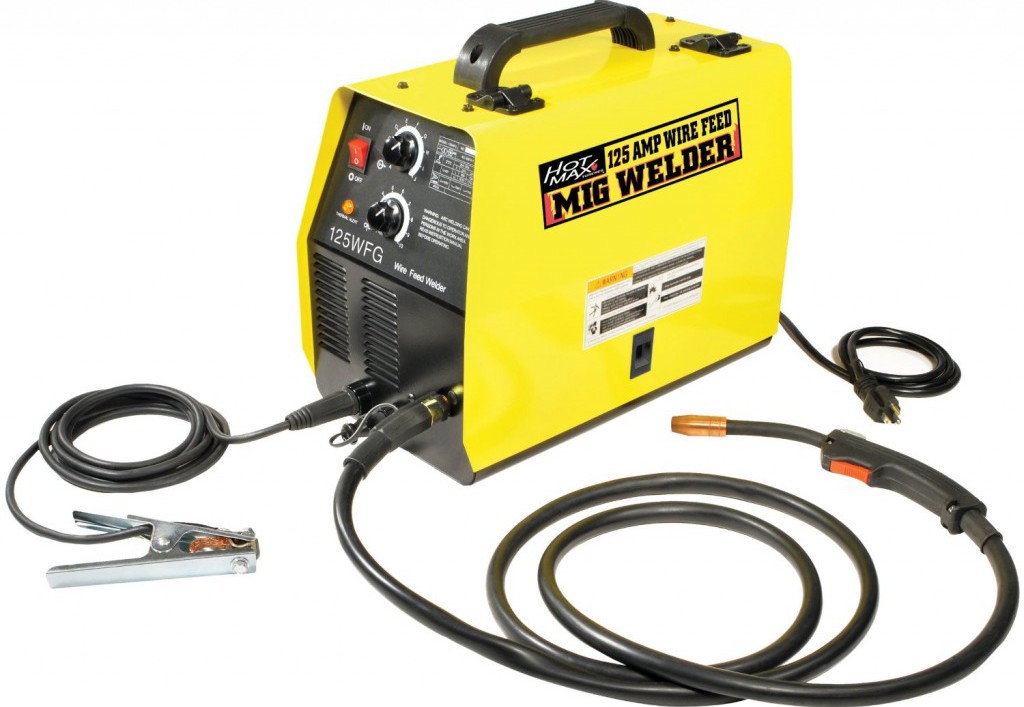
What is important from the point of view of the organization of the workflow is the value of the duration of the inclusion. It determines the relationship between the welding period and the rest time. So, in the case of powerful professional inverters, you can count on 6-7 minutes of welding, after which a break of 4-5 minutes will be required. Household appliances have a working time of 1-2 minutes, and rest - up to 10 minutes.
Feed mechanics
To automatically direct the wire to the working area, special units are used. They are a complex of electrical and mechanical components that support an uninterrupted welding process. The basis of a typical design is formed directly by the feed mechanism, welding sleeve, control unit and devices for the initial loading of cassettes with a new wire. Itβs a mistake to think that the equipment only works with consumables. Thanks to the integrated hose-hose, semi-automatic welding with a feed mechanism also forms a protective environment. That is, special organization of gas supply channels from the cylinder to the welding zone is not required with the help of adapters, gearboxes and regulators.
Welding torch
A tool for directly feeding a high-temperature torch to a workpiece. The device of such devices is quite simple. The main control element is a button or a mechanical flame regulator. It turns out manual semi-automatic welding, the control of which at the final stage of the formation of the seam is taken over by the master, and the auxiliary processes are supported by the same electrode feeding mechanism. When choosing a gun-burner, it is important to consider the diameter of the wire for gripping, the current strength (up to 650 A) and the type of cooling - built-in or external from the semiautomatic device.
Welding wire
The main consumable in such works is a wire or electrode. The thickness of this element determines with what blanks the semiautomatic device can work with. In addition, the diameter ultimately imposes restrictions on use in the feed mechanism. Conventional cars focus on 0.6-2 mm, but there are also non-standard models, which is important to consider when choosing. The material of the wire is also important. If it is planned to semi-automatically weld low-alloy and non-alloy steels, copper elements are preferred, and aluminum equipment interacts well with magnesium and silicon billets.
Activated wire models represent a special group. Their difference lies in the content of special additives in the rod (5-7%) based on oxides and salts from alkali metals. This modification allows you to get a neat seam and reduce melt spatter.
Accessories and equipment
When all the main components of the semi-automatic welding infrastructure are ready, you can proceed to the selection of accessories. Essentially personal protective equipment will be required. Semi-automatic carbon dioxide welding requires gloves, heat-resistant shoes, an apron and a mask. To protect against infrared and ultraviolet radiation, it is recommended to use filters for the overview. For example, masks of the "Chameleon" type are provided with self-regulating tinted windows, which creates not only eye protection, but also wearing comfort.
Conclusion
Among the main advantages of MIG-MAG welding technology is versatility. It is used both in the domestic sphere, and in industries, in construction, etc. The technical organization of the process requires considerable resources, but for large amounts of work these investments justify themselves. Why is semi-automatic shielding gas welding attractive for ordinary home craftsmen who only occasionally turn to such operations? First of all, the quality of the seam. As already noted, there are more accurate and accurate technologies, but in this case, you can achieve the optimal result with a high level of security and convenience. For example, many motorists acquire semiautomatic devices with consumables only for the full service of the car body. The ability to direct welding from different positions, in particular, allows you to perform the most complex operations during repair activities.