In modern plants using oil and oil materials, the percentage of waste can vary widely, sometimes requiring the involvement of third-party organizations for the disposal of waste products. In turn, liquid fuel boilers today are undergoing the next stage of development, offering consumers a lot of new technological opportunities. The use of economical fuel based on industrial waste just adds to this equipment attractiveness in the market. However, waste oil boilers have certain technical and operational features, which can also be considered as weak points. In any case, before choosing such an aggregate, a detailed analysis of all the technical, functional and economic aspects of its application is required.
General information about boilers at "development"
The concept of the secondary use of spent fuel materials has existed almost since the emergence of the problem of the disposal of oily waste. However, in boiler equipment, this approach has found a full-fledged life only recently - from the moment of mastering by large manufacturers of pyrolysis technologies and long-burning systems. These developments are more likely to relate to the processing of gas mixtures from solid fuels, but their principles can be shifted to the concept of waste oil boilers. In this case, a special burner is used for oil, connected to an inversion combustion chamber and a smoke pipe.
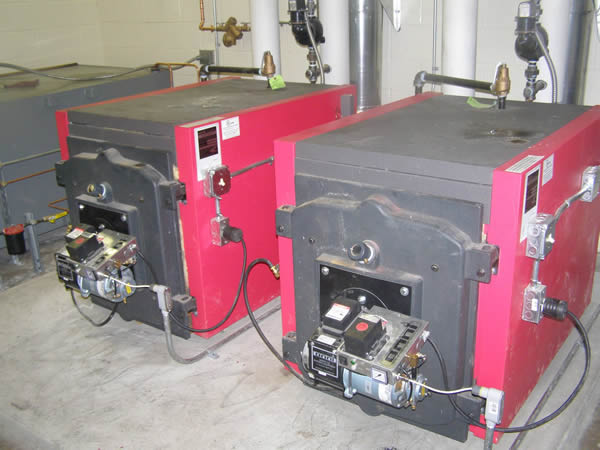
Of course, the main point of difference between this equipment and classic liquid fuel assemblies is the fuel feed used. There is still a certain segmentation according to the type of technological development products used, but the future of such models is universalization in terms of fuel supply. One way or another, boilers for a home in used oil primarily operate due to kerosene, diesel fuel and other diesel derivatives. Some modifications also support combustion when refueling with vegetable oils and special heating oil. In the case of industrial models, we can talk about the use of coarse inhomogeneous compositions with impurities.
Unit design
The main material for the manufacture of this type of liquid fuel boiler is metal - cast iron, steel and individual elements from other alloys. The structure is formed by the following parts:
- Body.
- Protective sheathing.
- The combustion chamber.
- Case cover.
- Fuel tank.
- Fuel line.
- A fuel supply pump.
- Burner.
- Divider.
- Bowl.
- Control panel with automation unit.
- Glass overflow.
- Damper
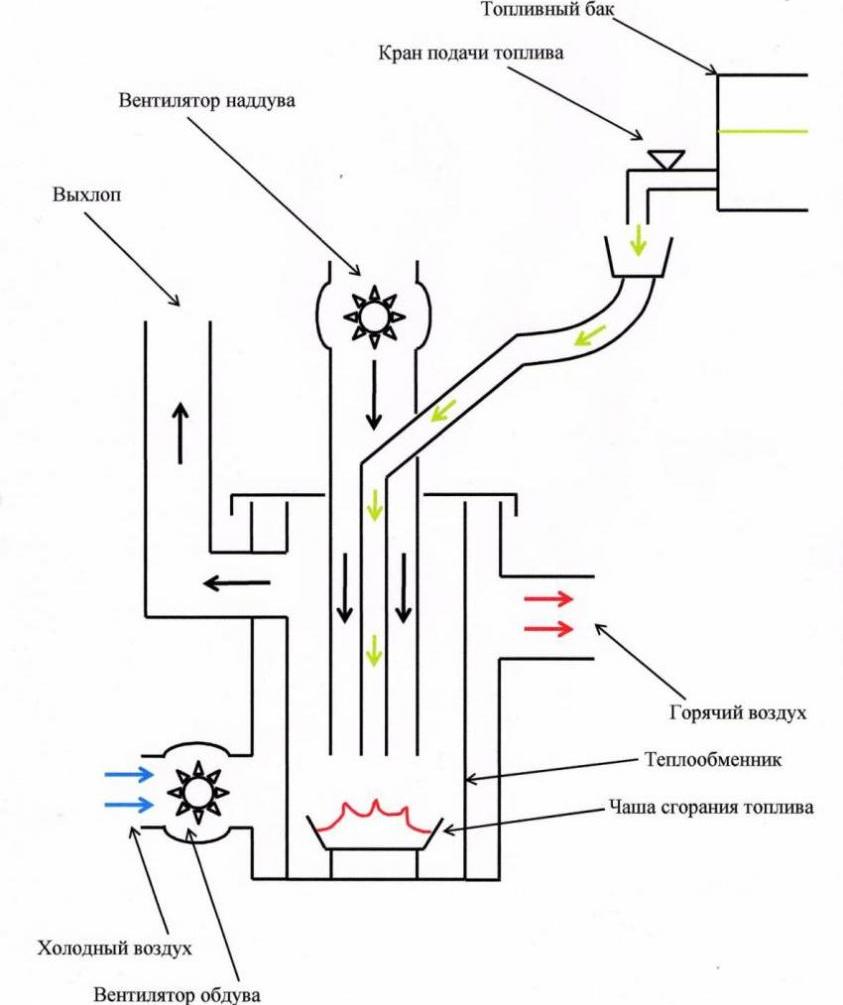
In the above drawing of a waste oil boiler, you can also notice the presence of a fan for supplying oxygen to the burner. This solution is rather optional, but it gives a fundamentally important opportunity to control the intensity of combustion. Theoretically, the possibility of converting the generated thermal energy into current, on which it is possible to provide an autonomous working process of equipment, is also allowed. However, the technical implementation of this function does not justify itself in practice for a number of reasons. On the other hand, power supply from a standard 220 V mains does not load the user much in terms of financial expenses, since energy is required only for low-power control electronics, and not for heat generation. By the way, the thermal power of such boilers averages 10-25 kW, which corresponds to the average performance of industrial heating equipment. The efficiency reaches 75%, which is also not bad, although gas pyrolysis units in modern versions reach 95%.
The principle of operation of the boiler
At the time of starting up the equipment, a fan starts operating through the control panel, directing air flows into the combustion chamber. At the same time, automatic ignition in the burner is performed. The full-fledged operation of the pump in the waste oil heating boiler starts after 30-40 minutes, when the body warms up. The temperature sensor, upon reaching the desired indicators, gives a signal to start the fuel line. Further, from the preheated bowl with the tank, oil is supplied to the burner.
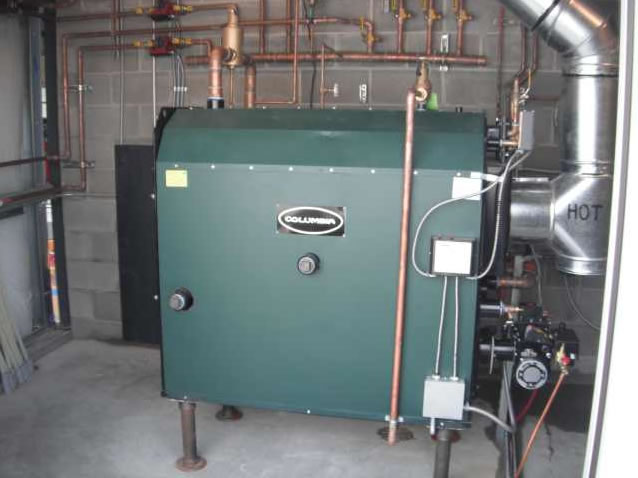
It should be noted that in different boilers the fuel supply is organized in several ways. In the simplest version, the oil is fed in its pure form without auxiliary additives. This simplifies both the design of the unit and its processes. But in more developed models, the fuel delivery channel has a number of technological points at which the liquid is filtered and enriched with air from the fan. At the final stage of the functional cycle of the boiler using waste oil, the mixture burns, and the products of combustion are discharged through the chimney to the street. After the burner function is completely turned off, the fan must run for some more time to cool the boiler walls and remove residual fumes.
Features of hot water models
Dual-circuit boiler equipment is today widely used in individual home heating and water supply systems. One circuit serves the needs of heating, and on the second a hot water supply is organized. What are the features of a boiler with a water circuit for waste oil? In this design, the unit combines the structural differences of indirect heating boilers and typical equipment for the burning of used oils. In particular, the design is complemented by the following functional components:
- Fuel heater. Before heading to the unit with the nozzle, the oil is heated to the optimum combustion temperature. This preparation is necessary to maintain fluid combustion stability.
- Storage tank. Buffer tank (receiver) for constantly or periodically heated water. The volume of the tank in the waste oil boiler can be 30-80 l, if we are talking about the household class of equipment.
- Heat exchanger. This component is present in all boilers. It is where the processes of water heating take place to service the DHW system. The type of energy supply for the heat exchanger is fundamentally important - either due to third-party boiler equipment, or using the built-in heating element with power from the same 220 V network.
In addition, in the design of a boiler with a water circuit on the used oil, less significant structural features are sometimes present:
- Refillable fuel filter - for use with low quality oils.
- Water cooling for the heat exchanger - required to prevent the formation of burnout and scale points.
- Aquastat is an additional control element of the boiler in the part of the water circuit.
Boiler fuel system
The fuel supply line, as already mentioned, can be organized according to various schemes. It does not have to be an integrated infrastructure - at least starting from a junction with a fence. In other words, a container with permanent storage of fuel material can be organized in a completely different room in a place safe from fire. In this case, the main thing is to organize a pumping system of sufficient power. Also, according to the rules for operating a boiler using waste oil, fuel must be taken from the bottom of the tank at a level not lower than 150 mm from the bottom. This is important to protect the communications from contamination by impurities and sediment that accumulates at the bottom.
As for the pumping system, the pump forms its basis. It is important to keep in mind that even boiler circulation pumps in this case will not work. Due to the specifics of the fluid being serviced, only special industrial models for technical mixtures can be used. The same applies to the pipeline with hoses and connecting-transition fittings. Like conventional water supply and heating networks with a liquid coolant, boilers operating on waste oil are not immune to air supply of the fuel mixture supply line. Moreover, in such systems, the presence of air can result not only in a decrease in productivity with thermal power, but also in a serious accident with damage to the combustion chamber. Therefore, an air vent, either manual or automatic, should be secured to the fuel assembly.
Waste oil burner
One of the most important devices of the unit, directly involved in the process of burning the fuel mixture. The burner must be sized and structurally compatible with the fuel pump, as well as the filter and heater, if any. In the kit with this device may be present:
- Pressure gauge for measuring pressure in the fuel line.
- Vacuum gauge.
- Assembly fuel intake fittings.
- Separator for additional purification of incoming oil.
The structural fastening of the burner for waste oil boilers is usually carried out on the flange of the front door of the equipment using a special gasket. Next, a heater and other functional accessories like the same filter are mounted. At the same stage, an electrical power supply circuit is laid to the heater. Moreover, it does not have to be connected to 220 V. In some models, 12 V is enough, that is, you can limit yourself to battery power supply. As for the connection to the fuel line, it is more often done through the fitting to the burner valve. A thin 1/4 ”hose is used for the liner.
Boiler communications
The main works regarding the connection of the boiler itself are the organization of hydraulic connections. At a minimum, pipes for oxygen supply (closed loop system) must be prepared, and in the case of using dual-circuit hot water models, piping for the heat exchanger is performed. If a full-fledged DHW system is organized, then it will not be superfluous to introduce a controlled multifunctional collector into the infrastructure, from which it will be possible to control the temperature on different water supply lines - for example, the contours of the sink in the kitchen, bathroom, bathtub, etc. On the other hand, a waste oil boiler must be connected to wastewater discharge channels. Although at the level of the storage tank with the heating system we are not talking about water consumption, the heat exchanger can be washed periodically, after which the used liquid is sent to the sewer. In terms of electrical connections, an insulated wiring circuit is organized in which a safety block, a short circuit protection system, a stabilizer and grounding are provided.
Homemade waste oil boilers
The design of such a unit can be assembled with your own hands, using special equipment and accessories that are also found in ordinary private households. The base will be arranged on metal housings, which will be required to contain the used oil and the combustion chamber. All connections to the combustion chamber are made using metal pipes - to a container with oil and a chimney. The most difficult thing to do with your own hands in a waste oil boiler is the automatic circulation system. To do this, it is better to use a submersible circulating oil pump. It is installed in a tank with fuel and pumps combustible liquid into the combustion chamber. The flow rate installed in the evaporation chamber, where the oil is preliminarily held, will control the oil supply rate. A fan with an oxygen boost is also connected to the combustion chamber to maintain stable combustion.
Equipment advantages
The strengths of the operation of boilers at the "development" include the following:
- Profitability. The main factor in favor of the use of this equipment. Gas is considered to be the cheapest fuel material, but this system can compete with it. Another thing is that the initial price of waste oil boilers is 15-20% higher than conventional liquid fuel models, averaging 70-100 thousand rubles.
- Autonomy. The system is independent of local engineering and communications lines. If there is no supply line for the same gas, then it makes sense to organize the delivery of used oil from the nearest disposal point or service station. Some enterprises are ready to give “working out” for free, therefore logistically such a scheme fully justifies itself.
- Efficiency. Liquid fuel boilers as such today are inferior to gas and solid fuel counterparts by a number of criteria, but they have a big plus in the form of high rates of heating and heat transfer rates.
Lack of equipment
Unfortunately, the positive aspects of the use of this equipment can be overshadowed by one significant drawback. It consists in high requirements for the maintenance of the unit. The wood stoves are considered the most “dirty” and troublesome in terms of maintenance, but recyclable materials of oil refining can cause even more problems in this regard. The fact is that waste oil for boilers contains persistent impurities that accumulate on the walls of the combustion chamber. Even in industry, specialized equipment is used for subsequent cleaning, and in everyday conditions only daily maintenance of equipment will help to eliminate the need for painstaking struggle with stagnant deposits.
Boiler Owner Reviews
The practice of using such boilers rather reflects the positive operating experience. Many users note organizational ease in servicing equipment due to the absence of oil delivery problems and economic benefits. Despite the skepticism of many private homeowners in principle regarding the use of oil recyclables as an energy source, reviews of waste oil boilers show that relatively clean mixtures pollute the chimney with a combustion chamber less than solid fuel units during operation. That is, it all depends on the characteristics of the oil used, but the very possibility of using a huge list of liquid fuel materials, of course, is a plus for such boilers.
Conclusion
Developers of heat supply systems today pay more and more attention to the possibilities of using alternative fuels. The prospects of this area are explained by both benefits for end consumers and the interests of preserving the environment. This tendency also fully complies with the principle of operation of boilers for waste oil. The price of such equipment is still at a relatively high level of about 100 thousand rubles. for a high-tech model with modern controls, but the low-cost maintenance process will pay back this cost over time. Another thing is that there may be expenses for maintenance activities, but this also applies to solid fuel and gas installations to varying degrees. Electric boilers are considered to be the cleanest, but because of the cost of energy, they are also the most costly from the point of view of financial content. Moreover, dual-circuit modifications with water heating regularly set records for operating costs.