High-temperature processing of materials is one of the key operations in many industries, where heat exposure is included in the list of basic technological processes. The conditions for organizing this procedure may be different, which leads to differences in the characteristics of the equipment used. In general, the segment of units, due to which intensive heat treatment is carried out, is formed by high-temperature industrial furnaces.
Classification of equipment by the principle of heat generation
To date, there is no universal way to generate thermal energy that is equally suitable for different operating conditions. However, a narrow group of the following types of the most popular furnaces used for high-temperature heating can be distinguished:
- Fuel The traditional way of generating heat, which is generated from chemical energy by burning solid, gaseous and liquid fuels.
- Electric. A wide segment of units that are convenient and safe to use. In the category of high-temperature electric furnaces, more modern induction and electric arc models are also distinguished. A common disadvantage of such equipment is the high cost of electrical energy, which is expended in large volumes.
- Autogenous. Furnaces of this type operate due to combustion and oxidation reactions of elements contained in workpieces. For example, during the oxygen purge of molten iron, a process of carbon oxidation with natural heat generation occurs. It is obvious that the use of autogenous furnaces is economically advantageous, since practically no additional fuel cells are required, but not all production facilities normally provide for oxidation and combustion processes. As a rule, this applies to the areas of metallurgical processing of metals and alloys.
Chamber furnaces
This is one of the most common designs of a high-temperature unit, designed to provide thermal effects with rapid heating to the required level. In order to maintain uniform distribution of thermal energy in production, special gas and oxidizing media are additionally used. The maximum heating mode for high-temperature chamber furnaces reaches 1800 ° C, when it comes to standard industrial models for metallurgical production. Electricity usually acts as a source of energy - the power potential varies from 0.5 to 3.5 kW on average.
Tube furnaces
A variety of high-temperature models of furnace equipment with the possibility of directional supply of heat flows. The design provides for heating and separate blocks, the rotary mechanics of which allow you to work at different angles, depending on current requirements. Some models of tubular high-temperature furnaces are equipped with a quartz reactor with gas-tight heads. This design solution provides the effect of double combustion of gases, which also creates the conditions for minimizing the initial fuel resources. As heat emitters, sectional type heating-insulating modules are usually used, providing heating up to 1200 ° C.
Features of muffle furnaces
For effective work in aggressive environments, which often takes place in the processes of industrial processing of raw materials, various types of muffle furnaces are used. They can be used for direct impact on the design of gases, dust, steam, water and other industrial wastes. Insulation problems are solved by special heat-resistant materials. For high-temperature furnaces operating in the temperature range from 1150 ° C to 1300 ° C, in particular, ceramic elements are used that not only protect the furnace from negative external influences, but also contribute to a uniform distribution of heat from the outside. The design may also include special support pipes, through which heat is radiated purposefully along certain contours and for short periods of time.
Melting furnaces
As a rule, these are units with a small heating chamber, designed to service compact workpieces. Target materials for processing in such furnaces include non-ferrous metals, which require special thermal conditions. There are also special model lines for performing operations in laboratory conditions, provided with a casting trough with the possibility of accurate dosing of the melt. Average heating rates in high-temperature furnaces of this type range from 1000 ° C to 1500 ° C with the possibility of precise regulation. This modification also includes some modifications of units for firing.
Main characteristics of furnaces
Even within the same type of high-temperature industrial furnace, operating parameters can vary over large ranges. The average indicators, with which large industrial enterprises most often work, can be represented as follows:
- The power of the unit is from 0.2 to 5-7 kW.
- Temperature conditions - from 300 to 2400 ° C or more.
- The volume of the working chamber of high-temperature furnaces is from 2.5 to 20 dm 3 .
- The mass of the structure is from 2 to 100 kg.
- Voltage - Three-phase 380 V networks are typically used.
Workflow organization
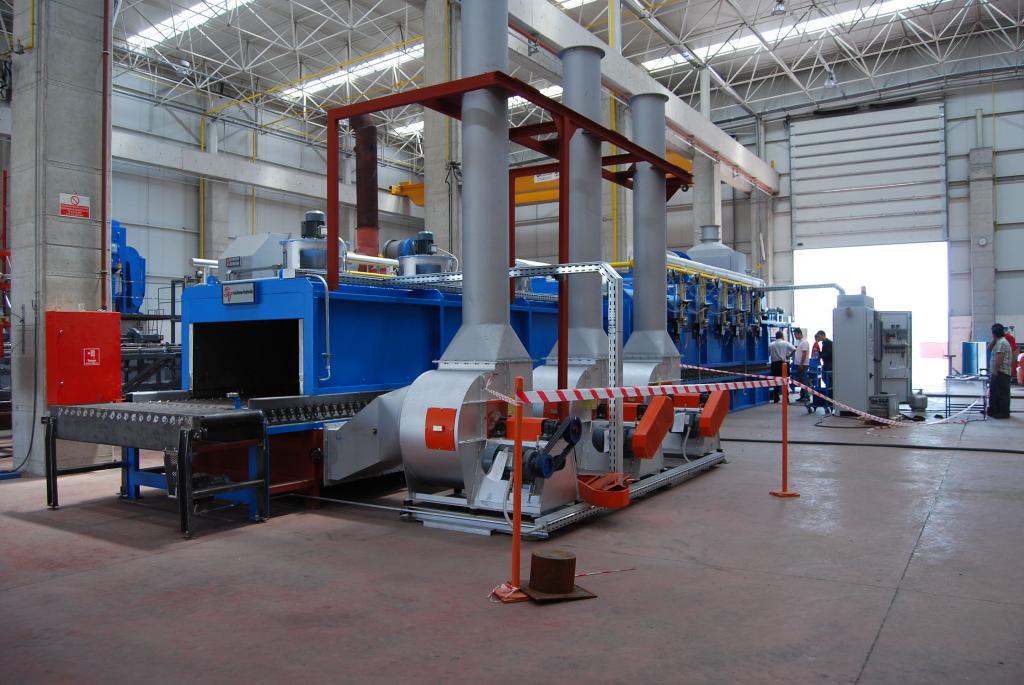
Installation of equipment is carried out in a stationary way, sometimes requiring preliminary installation of the foundation base in the form of a heat-resistant cement screed. The necessary communications and technological equipment for feeding blanks are brought to the furnace. Some components of engineering support are included in the basic package. For example, a cooling system is often implemented using a fan. High-temperature furnaces with a water cooling system are equipped with a circulation pump of suitable capacity, which is integrated into the local water supply infrastructure. Today, almost all industrial heating units are controlled by programmers with sensors and controllers of operating parameters. Thermostats can be integrated into the central control systems of the enterprise, which allows you to comprehensively monitor the performance of equipment in the general context of the production process, taking into account the characteristics of parallel technological operations.
Conclusion
The main scope of this equipment is metallurgy, as well as certain branches of the chemical and food industries. But even within such industries, the processes of thermal exposure are heterogeneous. As the processing technology becomes more complex, the approach to organizing thermal exposure operations is changing. The design requirements for high-temperature furnaces are also increasing. Materials for such equipment today are represented not only by tool steels, but also by heat-resistant ceramics, which makes structures easier and more practical to maintain. Furnace management approaches are also changing. The introduction of the same automation with programmable modules increases the efficiency of the workflow control, and at the same time increases the operational resource of the equipment and reduces energy consumption due to balanced control.