The technology of flooring on a dirt surface is often used in projects of country houses. Moreover, it should not be confused with the decorative finish as such, since a multi-purpose βpieβ is being formed, in the list of functions of which there is also power bearing support. If we compare with other options for the initial overlap, then the floors on the ground will be practical and economical. However, the technology of their device has its own difficulties, so the work process should be approached with maximum responsibility.
When is the technology used?
You can use this method of flooring with tape, columnar and other types of foundations, which do not provide for the filling of the entire working platform with a monolithic platform. For example, in the case of a tile base or complex screed, the reinforced concrete structure itself will act as a rough overlap. In other configurations, the central floor base should be interlocked with the structural elements of the foundation.
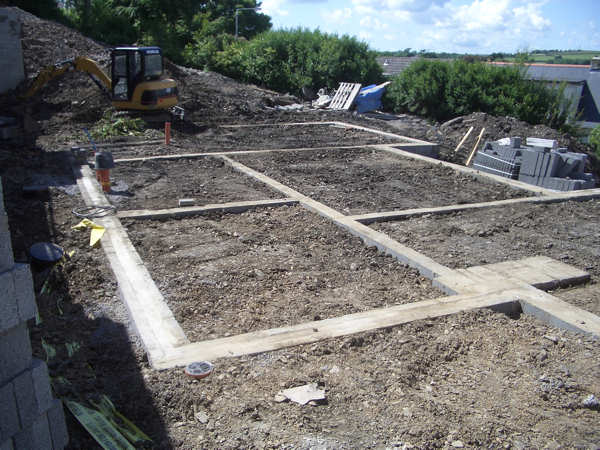
In the case of tape partitions, the floor is connected to the side walls of the structure, and with a columnar foundation, it adjoins the grillage. There are no technological limitations in terms of the structural arrangement of the floor on the ground with an emphasis on height relative to grillages. This parameter should be calculated based on what level the front door will have. This is an important point, since miscalculations in the distribution of the bottom of the door frame and the position of the opening in the tape in the future will require the formation of additional clippings.
There are few cases when specialists fundamentally do not recommend using a floor base on the ground. Is that the scheme of lifting the rough floor on piles makes it inappropriate to use this technology. At the same time, neither seismic conditions nor the groundwater level with freezing impose any restrictions on the creation of this type of floor platform.
Floor layers
The whole structure is formed on a soil basis, which before this must be sealed with high quality. Moreover, the turf layer is sometimes preserved, which improves the effect of thermal insulation. The first structural layer will be the bedding for the future floor on the ground, the thickness of which will be about 15-20 cm. By the way, the total height of the βpieβ will be 50-70 cm. The bedding is made of sand and large gravel. The main objective of this level is to protect against capillary rise of water, but also on problematic soils, the backfill also acts as a leveling layer.
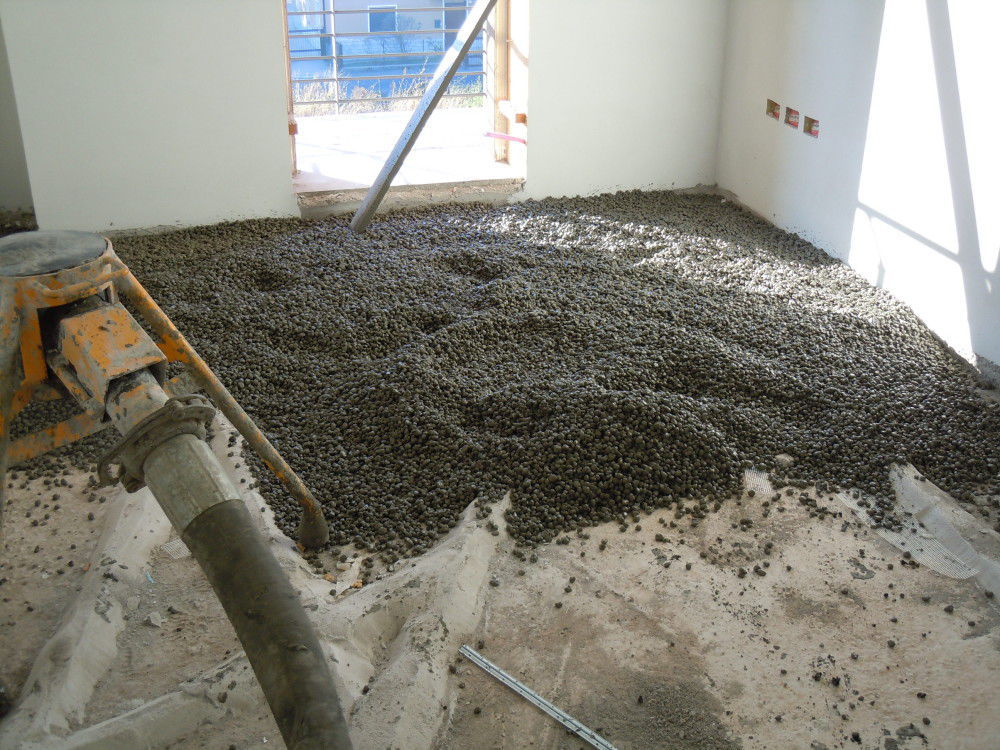
This is followed by a rough screed, the thickness of which will be 5-7 cm. It is performed on a waterproofing layer (for example, from a plastic film) using river sand and small gravel. This is the first reinforcing layer, followed by spillage and high-grade insulating materials. As for the main waterproofing, it is made of roofing material in one or more layers. Thermal insulation for the floor on the ground can be arranged using extruded polystyrene foam, and with the use of polystyrene with a density of 30-35 kg / m 3 .
The final layers will form the final coatings - screed and decorative finish. As for the first, its thickness will be about 10 cm. The solution is prepared from sand and fine-grained gravel and can be reinforced during pouring. There is no restriction for a fine decorative coating in the case of a concrete base.
Design options of the device
Floor requirements may vary depending on future operating conditions. But there are also user requests that the screed must answer. In both cases, you must initially decide on different ways of implementing the project. There can be no fundamental deviations from standard technology, but it is advisable to think over some structural nuances in advance. To begin with, the question of whether the base of the floor will have walls is decided. So, on a screed reinforced with a wire with a diameter of 4 mm, an arrangement of an internal brick wall or block of a partition 10 cm thick is allowed.
If the house has increased requirements in terms of insulation, the construction of the floor on the ground should be carried out with a gap between the walls and the final screed of 2 cm. The lower levels must necessarily adjoin the walls. The gap is left for future installation of coolants - for example, electric heating cables or water pipes of underfloor heating systems.
Another significant point of the technical device relates to the load on the carrier base. This issue will also be related to the need for the introduction of reinforcing elements in the rough screed. If it is assumed that the floor pressure will exceed 200 kg / m 2 , then for reinforcement it is better to use the same wire with a diameter of 4 mm. In other cases, they are limited to reinforcing with a wire mesh up to 3 mm thick.
Material selection
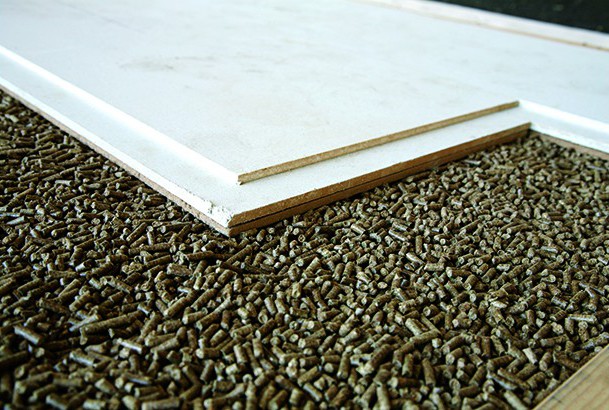
In almost every stage of the device of the next layer, a fork in the choice of material may occur. As a rule, this applies to means for performing spillage, bulk insulation and spillage. It has already been noted that the basis for these layers can be formed from a combination of sand and gravel of different fractions. But, for example, gravel is sometimes replaced with expanded clay. And in this choice, you must initially evaluate the tasks that the bedding will solve. If it is arranged as protection against capillary rise of groundwater, expanded clay should not be used, since it will swell upon contact with the liquid. However, as a leveling and even warming material, it turns out to be more profitable than crushed stone. Using a βpillowβ made of expanded clay, it is quite possible to create a warm floor on the ground at its very base, which will later eliminate the need for additional heat carriers. But to replace the same extruded polystyrene foam, a claydite layer of at least 15 cm is required. The main problem in such a replacement is caused by the difficulty of leveling the insulation flooring.
It is also widely believed that bulk materials can be replaced with broken bricks, as well as construction waste. This approach can justify itself only because of financial savings, but such a filler is not suitable as a full protection against groundwater or a way to level the bedding.
Wood flooring
The weak point of capital flooring on unpaved surfaces is considered to be insufficient strength and durability. In the case of wooden flooring, these shortcomings are amplified, therefore, this technology should be used in the construction of small houses. At the same time, this type of floor device has its advantages, the main one of which will be the ability to ensure air circulation in the underground niche. The fact is that between the directly wooden flooring and the dirt platform, free space is preserved, which has adjustable air ducts with channels in the walls.
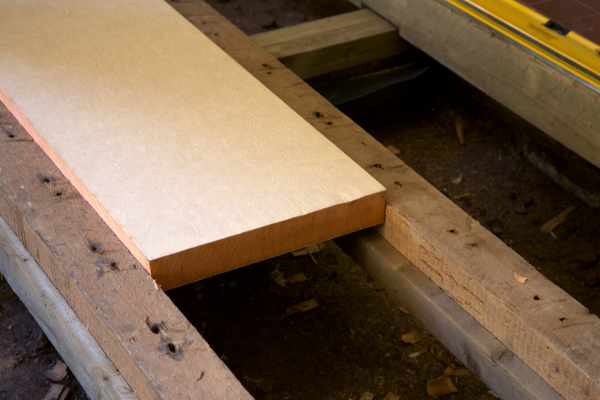
At the first stage, the soil is cleared and rammed. In the future, it is not necessary to cover it with bedding or arrange a screed. The power base will be columnar structures, which are recommended to be made of brickwork. A lag construction will be based on them, which can also be realized in the form of a crate. As for insulators, the wooden floor on the ground is previously protected by steam, hydro and heat insulators. As a material for supporting protective coatings, a reinforcing mesh can be used. The top layer is a boardwalk. Its elements are nailed to the lags and additionally fastened with metal ties. This coating can act as the basis for decorative finishes.
Concrete floor
A more common way to implement the technology, which is durable, functional and in terms of its technical characteristics, is slightly inferior to monolithic foundations. As already mentioned, layers of backfill, waterproofing and spillage are used as the base. Next, the first layer of screed is made of sand-cement mortar. After this layer, if necessary, you can repeat the insulation protection using mineral wool or polystyrene. Again, as an alternative, you can use bulk insulation materials like expanded clay. Bitumen is sometimes used as a means of bundling and tamping - it has an additional sealing effect and acts as a hydroinsulator in itself.
The main work in creating a ground floor on a sand-cement base will be associated with the filling of the final screed. The finished coating can be considered as the basis for decorative design. Depending on the characteristics of the flooring, additional surface leveling, insulation or primer may be required.
Ground screed pouring technology
It is desirable to perform the operation in one pass, so that a homogeneous, one-piece structure is formed. By the time of pouring, preparatory insulating, sealing and supporting layers should be arranged. A solution of screed for the floor on the ground is prepared from cement grade M400 with the addition of river sand and fine gravel. As for the proportions, one part of the cement has two parts of sand and four parts of the filler. All components are thoroughly mixed with a construction mixer or concrete mixer.
To obtain a flat platform, it is recommended to use formwork around the entire perimeter of the target site. Filling is carried out from one point - as a rule, central. This will allow faster alignment of the mixture, and a concrete vibrator will help to eliminate air bubbles from the structure of the mixture . If you plan to create a warm floor on the ground directly in the screed, then you should lay out the contours for it. Typically, such structures arrange water channels with connection to external collectors and thermostats. At this stage, it is important to evenly distribute the heating circuits throughout the site. Then the surface of the screed is covered with plastic wrap and left for a month.
How is reinforcement made?
There are several options for strengthening the floor structure, but they all rely on the device of reinforcement elements. It can be fiberglass or metal reinforcement, as well as a mesh. How to make floors on the ground using traditional reinforcement? To do this, a frame is created on the stands, on which the rods will be knitted. It is desirable to distribute the connection nodes so that a rectangular structure is formed over the entire casting area of ββthe future finishing screed. Knitting can be done manually or using a special mounting gun, using a thin metal wire as an consumable.
It is more convenient to use a finished metal mesh, but in this case the gain will be less reliable. Reinforcing mesh should be placed either in the middle of the layer or closer to the top. The choice of height will also depend on the use of coolants. If you plan to install a floor with pipes, then the grid should be laid on top - so that there is 2-3 cm of a layer of external protection.
Outdoor insulation
After the end of work activities and the completion of the polymerization of the final screed, surface preparation for decorative finishing begins. Almost all floor materials can be laid on a concrete base , and mainly laminate, parquet and plywood sheathing on a wooden board. Regardless of the type of exterior finish, insulation may be required. Final insulation of the floor on the ground can be performed using rolled materials, mats or plates. At this level, it is best to use natural products like felt, cork or mineral flooring. Waterproofing can be provided with thin membrane coatings with the function of vapor protection.
Conclusion
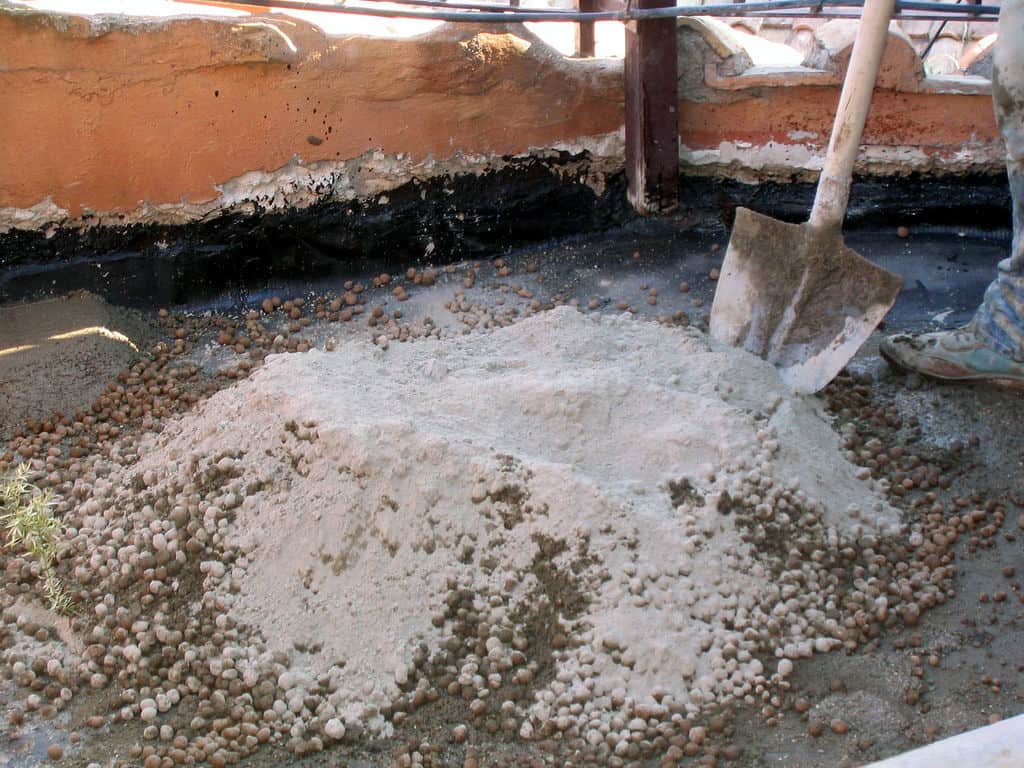
Subject to the installation technology, the floor on compacted soil will provide reliable protection for the foundation of the building for many years. But there are certain drawbacks to this method, which should be considered before choosing the type of foundation. The most pronounced include a reduction in the height of the ceilings, the complexity of changing the supporting structure after construction, and high financial costs. At the same time, the floor in the house on the ground provides a lot of opportunities in terms of solving problems to protect the base. These opportunities are opened by the multi-layer construction of the βpieβ, due to which, however, the height of the premises will also be reduced. But in any case, at each stage of the floor device, the performer can, with a high degree of accuracy, lay certain protective properties. For example, crushed stone bedding with two layers of screeds provides a reliable support base suitable for the construction of large country cottages of any complexity. Moreover, after each functional layer, it is possible to create insulating linings taking into account the technical features of the contacts between different materials.