This material is made from safe, clean and natural components (composition of sawdust concrete: sand, cement and sawdust). Due to the high content of organic filler (chips), such blocks have good sound-absorbing properties and a low level of thermal conductivity. In its parameters, this material is fully consistent with wood and therefore provides a high-quality microclimate in residential premises.
DIY making
Blocks from sawdust concrete can not only be purchased, but also manufactured independently, for this you will need:
- organic filler such as wood chips or shavings;
- alumina sulfate or lime;
- Portland cement M300;
- water;
- mineral additives, namely: water glass, calcium chloride, sodium sulfate and ammonia acid.
Sawdust concrete can be distinguished by composition, preparation technology, content of mineral additives and binders. In order to increase strength, sand is most often used.
Production of sawdust concrete is carried out according to the following scheme:
- pre-measured proportions of sand, cement, lime and filler are mixed;
- in a container with water you need to dissolve all prepared mineral additives;
- the solution that was obtained must be added to the prepared dry mixture;
- the whole composition is thoroughly mixed.
It should be noted that prepared components should not crumble in the hand. If this still happens, you need to add binders to it and mix everything thoroughly again. Hardening and solidification of the prepared blocks is slow, in order for them to gain their strength, several months must pass.
As a rule, stones of various sizes can be made from this material. To do this, you need to have special forms that have a removable bottom. Then the prepared mixture is poured into them in layers and constantly tamped, after finishing work, everything must be left until completely solidified. Next, the blocks will need to be removed and sent to a place in which the sun's rays and moisture do not fall, where they will finally harden and gain the necessary strength.
Manufacturing rules
In order to make sawdust concrete efficiently, you need to follow certain rules:
- Sawdust is added to water only after the binders and sand are dry mixed thoroughly. Moreover, water is infused only in small portions from the irrigation funnel with small holes.
- The main thing in adding water is its quantity, since if it is lacking, the material will be spoiled. And in the case of excessive amounts, drying and hardening will not work as it should.
- Then you need to check the quality of the substance. If everything was done correctly, then when compressed in the palm of the hand, the material will not fall apart and will give off light moisture.
- After the block has completely hardened, its surface should be well rubbed on all sides with cement or gypsum. Formwork can be removed after 5 days have passed.
- In order to increase the service life of the walls of this material, it is possible to replace the plaster with a brick cladding.
Quality
There are various types of building materials that are used for the construction of houses, among them, sawdust concrete, which has its own unique advantages, is especially distinguished:
- this raw material can be classified as light concrete;
- the material has fairly good thermal insulation properties;
- a wall of such blocks of 40 cm in its thermal conductivity can easily be compared with a brick wall 1 m thick;
- sound insulation performance is much higher than that of standard concrete;
- this material is characterized by frost resistance, fire resistance and vapor permeability (it can withstand a temperature of 1100-1200 degrees for about 2.5 hours), which is why it belongs to the group of slow-burning substances;
- ecologicaly clean;
- Among all types of lightweight concrete, it has the lowest thermal conductivity.
Sawdust concrete has all these positive qualities. The reviews of the builders indicate that this material also has disadvantages, which include hygroscopicity. Its water absorption is from 8 to 12%. But this flaw can be smoothed out. The external walls must be covered with brick or in another way to finish the facade, thereby protecting the walls from ingress of excess moisture.
Before the manufacture of sawdust concrete chips are necessarily treated with water-repellent compounds, which will reduce the hygroscopicity.
It is considered important that this material is easily machined, therefore, during the construction of the walls there will not be much waste.
Classification
Like all types of building materials, sawdust-concrete blocks must comply with GOST 6133-99. They are systematized by the following parameters:
1. Use:
- Intend for a laying of internal and external walls;
- partition walls are used only for the construction of partitions.
2. Form:
- hollow - have through holes that are formed during the manufacturing process (this is done in order to give the unit the necessary performance characteristics);
- corpulent - partition or wall parts that do not have internal voids.
3. Dimensions:
- in accordance with the above GOST, bricks for laying walls can be of the following sizes: 288x138x138 mm, 288x288x138 mm, 290x190x188 mm, 390x190x188 mm, 90x190x188 mm and 190x190x188 mm;
- the dimensions of the partition parts: 390x90x188 mm, 590x90x188 mm and 190x90x188 mm.
It is also possible to manufacture blocks and other necessary sizes.
Cost
Wood stone, or stone wood, as sawdust concrete is called, is also a fairly cheap material. Sawdust concrete, whose price is low, is considered the most affordable when compared with other materials. For example, one wall block, which measures 390x190x188 mm, made of sand and screenings, costs about 23 rubles on the market. A stone that has the same dimensions, but is already made of sawdust concrete, will cost 3-4 rubles cheaper, and at the same time it is lighter and warmer.
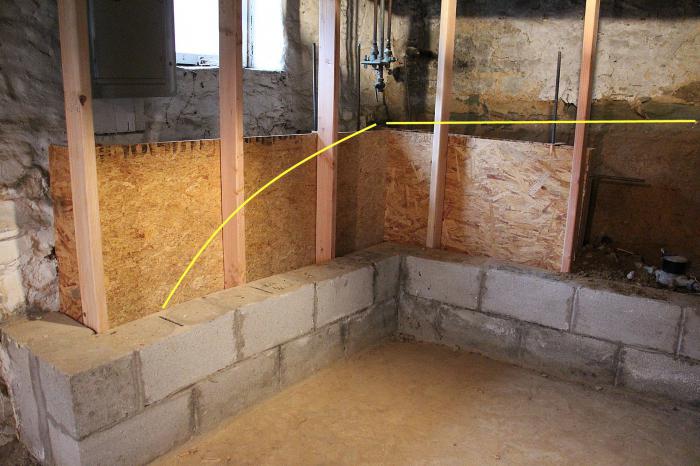
By the way, it can replace 7 bricks (the cost of one is 5-7 rubles). It is easy to calculate that a wall of a mixture of sawdust and concrete will cost 2.5 times cheaper than a brick one. In other words, to build a box of a house 8 by 8 meters, you will need 20,000 bricks, the owner will have to pay 140 thousand rubles only for stones, the same amount to be laid for the laying of the craftsmen and 40,000 rubles for sand and cement. If you use sawdust concrete, the price of such a building will vary from 100 to 150 thousand rubles. Agree, tangible benefits.
Compare with other materials sawdust concrete: the price per cube of brick will be 3 times higher than the cost of a cinder block cube, 2 times a cube of natural stone, and 1.5 times a cinder block.
Manufacturing technology
In order to properly prepare sawdust concrete, the proportions must be observed according to the recipe. All ingredients can be purchased at any construction store. The basis is chips, shavings, sawdust or any waste from woodworking enterprises. In order to prepare stones of the M20 brand, it is necessary to take 200 kg of cement, 50 kg of clay or lime, 500 kg of sand and 200 kg of sawdust.
For the manufacture of blocks, wood components must be sieved, and if necessary, chopped. For sifting, you need a sieve with 10x10 mm cells. Then, the prepared ingredients must be soaked in salts to remove the adverse effect of the sugar substances that make up the wood filler on the cement stone. Also, such impregnation will give the material non-combustible properties and protect against damage by rot and fungi. For these purposes, you can use sodium sulfate, lime, calcium chloride, aluminum, sodium, potassium or water glass.
To mix sawdust concrete, the proportions of which were observed correctly, it is best in a concrete mixer or in any other similar mixer, since it is quite difficult to do this with your hands. The wood filler is mixed together with cement and sand, after which lime (clay) dough is added and again everything is thoroughly mixed. Then, in small portions, pour water. Then mix thoroughly the resulting mass.
In order to determine whether the mixture is ready or not, you need to squeeze it in your hand. Ready can be considered a mixture in the form of an elastic lump without excess moisture. The prepared mass must be decomposed into molds and carefully packed so that the excess air is completely out. All this must be done quickly enough, since after 1.5 hours the mixture will already set.
There are no strict requirements for the sizes and shapes of the prepared blocks. The width is most often determined by the size of the wall, and the height remains a multiple of several rows of bricks (taking into account the solution between them). This will become especially convenient if at the end a brick cladding is applied to sawdust concrete. The responses of the builders indicate that it is not necessary to make very large blocks, since they will dry for too long, and the deformation during shrinkage will be significant. In order to avoid such troubles, they make several holes in them. Forms for the manufacture of large stones are prepared single or double.
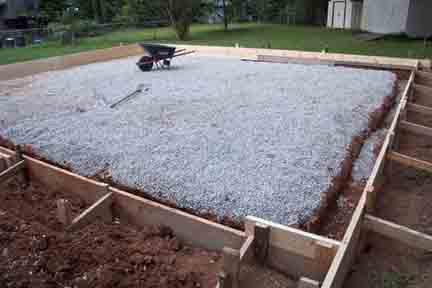
For blocks of small sizes, it is best to use forms in which you can fill from 4 to 9 stones. For their manufacture, boards with a thickness of 30 mm are most often used, then they are surrounded with tin, plastic film, plastic, linoleum or other material, the adhesion with cement of which will be insignificant. Outside the form is pulled together by U-shaped couplers with nuts at the ends. For large structures, additional couplers or a stiffener must be provided.
Reviews
Recently, very often, such inexpensive and high-quality material as sawdust concrete has been used in construction. The reviews of builders who often work with him confirm its main advantages. These include:
- Environmental Safety. This material is made only from natural components (sand, wood sawdust, cement), and this ensures its high environmental friendliness.
- In terms of vapor permeability and sound absorption, it can be compared with wood.
- It fully complies with established sanitary standards.
- Due to the low thermal conductivity of the material and the voids that are in it, the house of sawdust concrete will be quite warm.
- Low specific gravity allows reducing transportation and foundation costs.
- Ease of handling greatly simplifies construction. Such blocks can be sawn, it is very easy to drill, and it will not be difficult in the future to drive a nail into the wall from sawdust concrete.
- The material has high bending and tensile strength.
Despite all the advantages, negative feedback about this material can also be heard from the builders. The disadvantages include the following points:
- A relatively high degree of moisture absorption, which requires measures for additional moisture protection.
- There is a need to increase the cement content in the block during the construction of several floors. This can lead to a rise in price, deterioration in the quality of thermal insulation and increased requirements for the strength of the foundation.
- There is a relatively high degree of shrinkage, which complicates the finishing work.
How to build a house out of blocks
The house of sawdust in all sanitary and hygienic indicators will have good soundproof and heat-insulating qualities. Due to the large number of air pores that are inside this material, the walls will firmly retain heat and guarantee natural ventilation of the rooms, thereby maintaining optimal humidity.
From sawdust concrete it turns out to be a fairly low-cost house construction (the price of the material was considered by us above). In addition, blocks, in addition to what can be purchased at any hardware store, are easy to make on their own. You need to know that this material must be prepared in advance for styling, if you did it yourself. To do this, it should be dried for several months.
Recently, private construction has become popular; blocks of various sizes are used for it, depending on needs. Walls made from such raw materials will be strong enough, lightweight and low heat conductive. If they are built correctly, they will last a very long time.
As we said above, sawdust concrete has a high moisture capacity. Therefore, after construction, the walls must be plastered, but this is best done after complete shrinkage (this process will take about 8 months).
The sawdust concrete bath, like the house, must be very strong, so the walls must be reinforced with wooden slats or brushwood, which is previously cleaned of bark. The prepared reinforcement is laid every 40 cm in several rows. At the same time, great attention must be paid to the corners and joints of the walls.
Useful tips for making blocks
A large number of masters use sawdust concrete for their work. The builders' feedback on this material is very good and will be useful if you are going to make it yourself. In order to produce quality blocks, it is necessary to take into account a number of recommendations:
- for thorough drying, you must leave gaps between them;
- before filling the material into molds, they are installed on pallets and sprinkled with a thin layer of sawdust;
- the mixture needs to be well compacted, builders often use manual tampering for this purpose;
- it is better to dry the prepared blocks in drafts, due to this, the solidification time will be reduced;
- one must not forget that it can rain if there is no canopy, it is necessary to prepare polyethylene in order to manage to cover the material in case of bad weather.
In order to find out how durable the material turned out, you can conduct a test. For this, the prepared block is dumped from a height of 1 m, if it remains intact, it means that it is of good quality.
The construction of a monolithic house
Today, it is considered very fashionable and convenient to quickly build. Masters often use monolithic sawdust. For the construction of this type, it is necessary to lay on top of the foundation two layers of waterproofing from roofing material. In the case of a low base, several rows of brickwork should be completed. Then the formwork is mounted, the material for which can be steel sheets, lumber, moisture-proof plywood.
The height of the installed shields should be approximately 60 cm. At the time of pouring the first layers on the side of the foundation into the soil, the stakes are driven into the entire height of the walls. The selected material for the boards is wedged between the side surfaces of the foundation, and then the stakes are joined together by pieces of bars, and those that are located on opposite sides of the wall are pulled together with a wire.
At the end of the casting, the pegs should remain in the walls, then they will be used to fasten the panels during the formwork rearrangement, and after the private construction is completed - to fix the battens when facing.
The prepared mixture for sawdust concrete is poured in layers whose height does not exceed 15 cm, and then carefully rammed. At one time, the wall can only be raised by 20-30 cm, after which you need to take a break for 5-7 days. Every 40 cm, it must be reinforced longitudinally using wooden battens or steel mesh.
After the filling is completed, a belt of timber is laid out on top, which in the future will serve as a support for the roof elements. It is very important to protect new walls from moisture. To do this, the future roof is made with wide overhangs, and the facade is faced.
Not very expensive will be the construction of a house. The price of sawdust is quite acceptable for the average resident of our country. The construction will serve for many years, its walls erected from this material will not require insulation, and a laying of 40 cm will provide frost protection even at -35 degrees.