Ultrasonic thickness measurement is a non-destructive one-way method for determining the width of the material. It is fast, reliable, versatile and, unlike a micrometer or vernier caliper, does not require access to two sides of the subject. The first commercial sensors using the sonar principle appeared in the late 1940s. Small handheld devices optimized for a wide range of applications became familiar in the 1970s. And innovations in the field of microprocessor technology have achieved a new level of accuracy, simplicity and miniature.
A large number of well-known companies are engaged in the production of devices. Among them - the German company Siemens, the American Dakota Ultrasonics, the British Cygnus. In Russia, devices are manufactured by such companies as NPF AKS, NPK Luch, NPP MaxProfit, etc.
What can be measured?
Virtually any conventional structural material can be measured using ultrasound. Ultrasonic sensors can be tuned to metals, plastics, composites, fiberglass, ceramics and glass. Measurements of extruded plastics and rolled products are also possible during the manufacturing process - both individual layers or coatings, as well as multilayer products, liquids and biological samples. Another operation where an ultrasonic thickness gauge is simply necessary is to determine the thickness of bricks, structures made of concrete, asphalt and rocks. Such measurements are almost always non-destructive and do not require cutting or disassembling the object.
Materials that are not suitable for conventional ultrasonic metering due to poor transmission of high frequency waves include wood, paper, concrete and foam products.
How to measure?
Sound energy can be generated in a wide range of frequencies. Audible sound ranges from 20 to 20 kHz. The higher the frequency, the higher the perceived tone. Energy of a higher frequency, beyond the limits of human hearing, is called ultrasound. Most often, ultrasonic testing is carried out in the frequency range from 500 kHz to 20 MHz, although some specialized instruments reach 50 kHz or 100 MHz. Regardless of frequency, sound energy is a mechanical oscillation that takes place in a specific medium, such as air or steel, in accordance with the basic laws of wave physics.
For measurements using an ultrasonic thickness gauge. The principle of operation of the device is to accurately calculate the transit time of the pulse from a small probe (transducer) through the measured object, reflected by its inner surface or the far wall. Since sound waves are reflected from the boundary between dissimilar materials, this measurement is usually done on the one hand, in the "pulse / echo" mode.
The transducer contains a piezoelectric element, which is excited by a short electric pulse to generate discrete ultrasonic waves. They are sent to the measured material and pass through it until they collide with the back wall or other obstacle. The reflected wave returns to the sensor, which converts mechanical vibrations into electrical energy. In essence, ultrasonic thickness gauges listen to echoes from the opposite side. Typically, the time interval between the sent and the reflected signal is only a few millionths of a second. The device contains data on the speed of sound in the test material, from which it can then calculate the thickness using a simple mathematical relationship: d = V t / 2, where:
- d is the thickness of the plot;
- V is the speed of sound;
- t is the measured travel time of the sound.
Important parameter
It is important to note that the speed of sound in the studied object is an essential part of this calculation. Different materials transmit sound waves in different ways. As a rule, it is higher in solids, and lower in soft ones. In addition, it can vary significantly with temperature. It is always necessary to calibrate ultrasonic thickness gauges for speed in the measured material, on which the accuracy of the instrument readings directly depends.
Sound waves in the megahertz range pass through the air poorly, therefore, to improve the transmission of sound between the emitter and the sample, a drop of connective fluid is placed. Typically, glycerol, propylene glycol, water, oil, and gel are used as contact fluid. A small amount of liquid is enough to fill the extremely thin air gap.
Measurement modes
Manufacturers of ultrasonic thickness gauges measure the time interval for the passage of energy through the test sample in three ways:
- The gap between the excitation pulse that generates the sound wave and the first returning echo minus the small offset value, which compensates for delays in the instrument, cable and transducer.
- The time interval between the returned echo from the surface of the sample and the first reflected echo.
- The gap between two consecutive bottom echoes.
The choice of mode, as a rule, dictates the type of converter, as well as the specific requirements of the application. The first mode is used with a contact sensor and is recommended for most applications. In the second, there is a delay line or immersion transducers used on convex and concave surfaces, in a confined space, for measuring moving material or objects with high temperature.
The third mode also uses delay lines or immersion sensors and, as a rule, provides high accuracy and the best minimum thickness resolution. It is usually used when the quality of measurements in the first or second mode is unsatisfactory. However, the latter mode is suitable only for materials that produce pure multiple echo signals, as a rule, with a low attenuation index, as in fine-grained metals, glass, and ceramics.
Two types of devices
Ultrasonic thickness gauges are usually divided into two types: corrosion and precision. One of their most important applications is to determine the residual wall width of metal pipes, tanks, structural parts and pressure vessels, which are susceptible to internal corrosion and cannot be visible from the outside. Ultrasonic corrosion thickness gauges are designed for this. They use signal processing methods that are optimized to detect the minimum residual wall width in coarse and rusty samples with specialized dual-element sensors.
In other cases, it is recommended to use high-precision devices with single converters - for metals, plastics, fiberglass, composites, rubber and ceramics. Many different sensors of precision devices have been created, which are capable of measuring with an accuracy of ± 0.025 mm and higher, which exceeds the performance of corrosion meters.
GOST classifies ultrasonic thickness gauges by purpose, degree of automation, protection against environmental influences, resistance to mechanical stress, and also determines their main indicators.
Transducer Types
- Contact sensors are used in direct contact with the test sample. Measurements with their help are simple, therefore they are used most often.
- Transducers with a delay line contain a plastic, epoxy or quartz cylinder as an intermediate link between the active element and the object under study. The main reason for their use is the measurement of thin objects, where it is important to separate the excitation pulses from the bottom echo signals. The delay line can serve as a heat insulator, protecting the thermally sensitive element of the sensor from direct contact with hot materials. It can also be shaped to improve traction on sharply concave or curved surfaces.
- Submersible transducers use a water column or bath to supply sound energy to the measured element. They are used to measure moving objects, to scan or optimize grip in the presence of sharp radii, grooves or channels.
- Two-element transducers are used in corrosion gauges to determine the width of objects with a rough, corroded surface. They consist of a separate transmitting and receiving element installed at a small angle to the delay line in order to focus energy at a selected distance below the surface of the measured sample. Although such measurements are not as accurate as other types of sensors, they typically provide significantly higher performance.
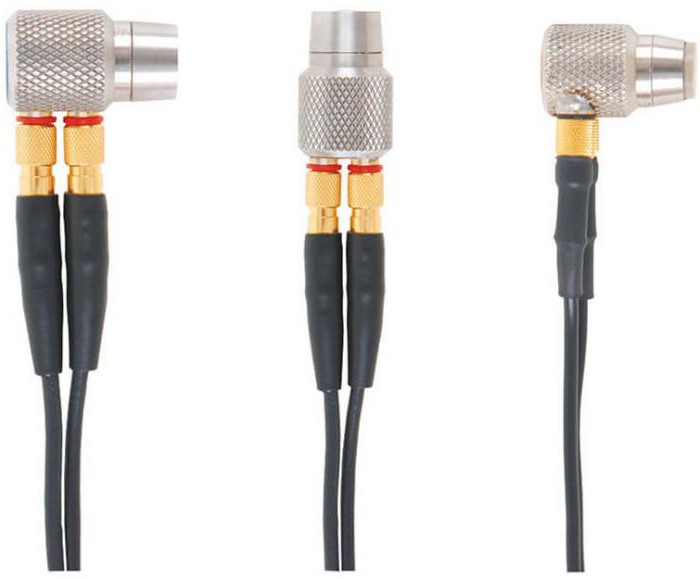
Ultrasonic thickness gauge: instruction
To prepare for measurements, connect the transducer to the device, turn it on, set the speed of sound and calibrate. To do this, apply a little contact substance to the calibration standard, attach a sensor and enable calibration mode. This procedure must be performed after replacing the inverter or batteries. Calibration options for known thickness and sound velocity are possible.
For measurements, it is necessary to apply a contact substance to the surface of the object and attach a sensor. The result is displayed. You can use the device in scan mode, for example, to search for the smallest thickness of the material. You can also configure the signal to detect a place with a wall size less than the set value.
To measure the speed of sound, it is necessary to measure the object with a caliper or micrometer, attach a transducer and wait for the result. Having set the previously measured value, press the button to save the data in the device memory. Some devices allow you to transfer results to a PC.
Ultrasonic thickness gauge: reviews
Users positively appreciate the compact size, ease of use, reliability, ease of calibration of modern instruments. Experts note the lack of alternatives to devices of this type in assessing the condition of cars, the quality of bodywork. The device allows you to determine whether the vehicle was repainted and whether it participated in the accident. Thickness gauges that do not require contact fluid, as well as those capable of self-calibration, are most popular.
Material and range
An ultrasonic thickness gauge, the principle of which is selected depending on the composition, measurement range, geometry, temperature, accuracy requirements and other possible conditions, is sometimes simply irreplaceable.
The type of material and measurement limits are the most important factors when choosing a device and transmitter. Many substances, including most metals, ceramics and glass, conduct ultrasound very efficiently and allow measurements to be taken over a wide range. Most plastics absorb energy faster and therefore have a more limited maximum thickness range, but in most industrial situations, measurement is not a problem. Rubber, fiberglass and many composite materials absorb much more and require large transmitters and receivers optimized for low-frequency operation.
Thickness determines the type of converter. Thin objects are measured at high frequencies, while thick or damped objects are measured at low frequencies. For very thin materials, a delay line is used, although they, as well as immersion transducers, are limited in thickness due to interference from multiple echoes. For wide objects or objects consisting of several materials, different types of sensors may be needed.
Surface curvature
With increasing surface curvature, the contact efficiency between the transducer and the measured object decreases, therefore, with a decrease in the radius of curvature, the size of the sensor should be reduced. Measuring very small radii may require the use of delay lines or contactless immersion transducers. They can also be used for measurements in grooves, cavities and other places with limited access.
Temperature
Contact transducers are generally applicable at object temperatures up to 50 ° C. Hotter materials can damage the sensor due to the effect of thermal expansion. In such cases, always use transducers with a heat-resistant delay line, immersion or high temperature sensors with two elements.
In some cases, an object with a low acoustic impedance (density multiplied by the speed of sound) is connected to a material with a higher acoustic impedance. Typical examples are plastic, rubber and glass coatings of steel or other metals, as well as a polymer coating of fiberglass. In this case, the echo from the boundary between the two materials will be phase-inverted - inverted with respect to the echo from the boundary with air. This can be corrected by simply changing the instrument settings, but if nothing is done, the readings will be inaccurate.
Error
The accuracy of measurements is influenced by many factors, including the verification of ultrasonic thickness gauges, their calibration, uniformity of velocity in the substance, sound attenuation and scattering, surface roughness and curvature, poor connection and bottom non-parallelism. Accuracy is best achieved by using standards of known size. With proper calibration, the error of the ultrasonic thickness gauge is ± 0.01 mm and even ± 0.001 mm. Delay lines or immersion sensors in the third mode also increase measurement accuracy.