Many people know that there is such a building material as expanded clay. This is common knowledge. But few people can give complete answers to the questions of what it is, what properties it has, how it is produced and where it is applied. We will try to fill this gap.
What is expanded clay
Expanded clay is a lightweight porous material produced in the form of gravel or gravel. Its production is based on firing in special furnaces at a temperature of about 1200 ยฐ C of special clay rocks of easy melting. Due to firing, the clay structure acquires a finely porous structure with a pronounced hard shell.
Such a structure of the material determined the diversity of its application. This material is used both in construction works and when planting plants.
The unique properties of expanded clay include water and frost resistance, excellent noise and heat insulation parameters. The material is practically not susceptible to decay and decomposition, does not attract insects and rodents. In addition, it is durable and refractory, frost and acid resistant, lightweight and durable, environmentally friendly and economical. Thanks to these qualities, expanded clay is widely used in construction and other sectors of the economy.
Expanded clay as a heat insulator
The ability of expanded clay to be a heat insulator depends on the size of the granules, its strength and bulk density. Expanded particles of granules produce fractions of expanded clay 5-10, 10-20 and 20-40 mm. Each fraction allows 5% of granules of a different size. By the density of expanded clay, 10 grades are determined, ranging from 250 to 800. This number indicates the number of kilograms in one cubic meter of material. The lower the density, the better the properties of expanded clay as a heat insulator. Expanded clay of a large fraction is more durable. It is suitable, for example, for warming the floor in a bath, and the attic can be insulated with a fine fraction.
Expanded clay production
For the production of expanded clay, only certain clay rocks are suitable. The most suitable are montmorillonite and hydromica clays containing less than 30% quartz. The essence of expanded clay production is the preliminary processing of raw clay, giving raw granules of a certain size, burning them in special kiln-drums to obtain a specific structure and stage-by-stage cooling.
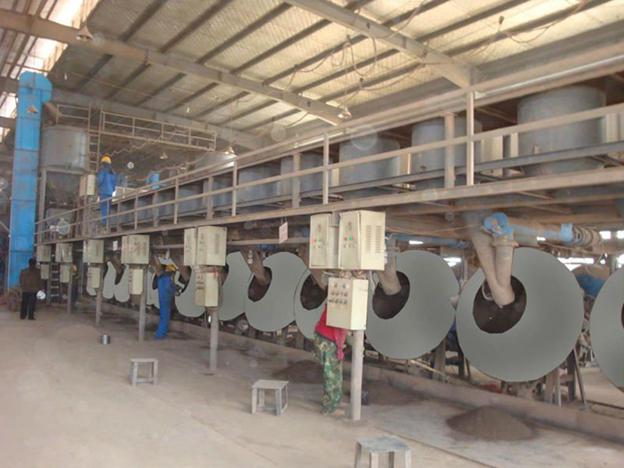
There are several technologies for pre-processing clay raw materials. This is a dry treatment, plastic, powder-plastic, as well as wet, or slip. The first (dry) technology - the simplest one - involves multi-stage crushing of pieces of clay rock with sieving of suitable fractions for further processing. The second, most common - plastic - consists in mixing raw clay with a clay mixer, molding cylindrical granules and drying them. Powder-plastic technology differs from the previous one only in that the raw materials are converted to powder before kneading. Finally, with wet or slip, technology from raw materials and water is first obtained with the help of clay soakers, the so-called slip with a moisture content of about 50 percent, which is then pumped into the furnace, characterized by the presence of curtains from suspended chains. The latter are heated and break the slip into particles, which are then fired.
A rotary kiln in the form of a firing drum is installed at a slight slope. The source material in the form of clay granules is poured into its upper end and gradually rolls down to the burning nozzle. Under the influence of hot gases and strong heat stroke when falling on a burning fuel from a nozzle (with a temperature of about 1200 degrees), clay boils and swells, and its outer layer melts.
The whole firing process lasts no more than 45 minutes, forming the familiar expanded clay light and durable gravel. Other fractions of expanded clay production (crushed stone or sand) are obtained by crushing this gravel. Higher quality products can be obtained using technologies based on the use of two and three-drum furnaces, in which the drums rotate at different speeds, creating the optimal mode of heat treatment of raw materials.
The final stage in the production of expanded clay is cooling in several stages with a gradual decrease in temperature, first in the furnace itself, then in drum and layer coolers and, finally, in aerial chutes.
Where is expanded clay used?
This is just a small list of applications:
- thermal insulation of roofs, ceilings and floors;
- soundproofing of floors and floors;
- Creation of a slope of lawn surfaces;
- production of lightweight concrete, expanded clay concrete blocks;
- thermal insulation of foundations and soil;
- drainage in road construction;
- growing plants (hydroponics).
Expanded clay delivery form
Expanded clay is delivered in bags or in bulk on dump trucks. Material in packaged form is much more convenient. It is easier to take into account (20 bags make up one cube of expanded clay), unload, store, and also transport to the place of work. Loose expanded clay is cheaper, but it gives more trouble. Therefore, it is better to use expanded clay in bags.
Expanded clay floor insulation
A significant part of the thermal energy leaves the house through the floor. To avoid such losses, the floor is insulated. This is especially important in cases of making concrete floors. Among the many thermal insulation materials available on the market, expanded clay is the most affordable. This application of this material (as insulation) is perhaps used most widely in construction. And this is not surprising. After all, a layer of expanded clay 10 cm thick corresponds in its insulating properties to a meter thick brickwork or a 25-centimeter thick wood.
Expanded clay is used for the floor (for its insulation) using the dry method (bulk method) or pouring expanded clay concrete screed. The process of warming is quite simple, it can be done on its own. It includes the following steps:
- marking the level of expanded clay filling (for better insulation, the layer should be at least 10 cm);
- waterproofing (high-strength plastic wrap);
- putting beacons to get a flat surface;
- filling and sealing of the insulation layer;
- surface alignment as a rule;
- pouring a layer of cement-sand screed on top of expanded clay.
Use the floor only after drying the screed.
Acceleration of floor insulation can be achieved using the dry method, when Knauf floors are lined on top of the expanded clay layer. They can be used directly after assembling the floor from the elements fastened together
with PVA glue and self-tapping screws.