One of the traditional materials used for indoor and outdoor decoration of living quarters is wood. There are many techniques for artistic processing of wood, but the most spectacular decorations are obtained when slotted carving is used. The beauty and grace of such products amaze the imagination, while the technology itself is not particularly difficult.
Features of openwork carving
Openwork, or slotted woodcarving is performed by cutting through or drilling through the background. Ready-made patterns and compositions look light and airy. Openwork carving happens through and laid on. Through slotted thread "works" in clearance. An overlaid thread is when a welt pattern is attached to any base, for example, a wooden one, which serves as a background.
Chisels, special cutters, drills or files are used for cutting through sections. The most productive tool is an electric jigsaw. The slotted jigsaw thread allows you to easily and quickly reproduce patterns of even the most complex configurations.
Preparation for work
Novice masters should first of all pay attention to the theoretical part. Fortunately, today there is a lot of useful printed and video information about how grooved woodcarving is performed correctly, about the necessary tools, about the features of a particular wood, about preparing blanks, choosing patterns, etc.
Having studied the features of the technology, you can do the selection of tools. In addition to a jigsaw and a set of files with different tooth sizes, sharp knives, chisels, chisels, drills and drills of various thicknesses, spoon cutters, files, abrasive bars and grinding skins will be required to work.
Another stage of the preparatory work is the selection of patterns, compositions or genre scenes, to create which will be used wood carving. Sketches can be done independently or found on specialized sites and printed on a printer, if necessary, previously reducing or increasing their size.
Features of different types of wood
How high-quality, fast and neatly carved threads will be made depends not only on the skill level of the performer, but also on the wood. Each breed has its own unique properties, which must be taken into account when choosing a material for the workpiece.
- Pine tree The most affordable and inexpensive wood, however, it is not suitable for carving, and not only because of resinousness. The fact is that it consists of hard and soft layers. Cutting and grinding of pine products is rather difficult due to the difference in structures, since the knife and sandpaper โtakeโ them differently. In addition, this species of wood has a pronounced texture, which distracts attention from the carving pattern itself, especially if it is small.
- Aspen . Slotted carving from this wood is fraught with difficulties associated with the softness of its structure. Despite the fact that aspen is cut like butter, the tool โgets stuckโ when cutting, and it itself wrinkles. Beginner-carvers who do not have experience with this material, definitely should not start their โcareerโ with it, as well as with pine.
- Birch and linden . These wood species have a beautiful monophonic structure, the necessary hardness and at the same time flexibility, which allows to realize even the most complex and intricate carving sketches in products.
- Plum . Solid, very beautiful cross-sectional wood that lends itself well to all types of processing wood. It is great for creating products with small patterns, such as women's jewelry.
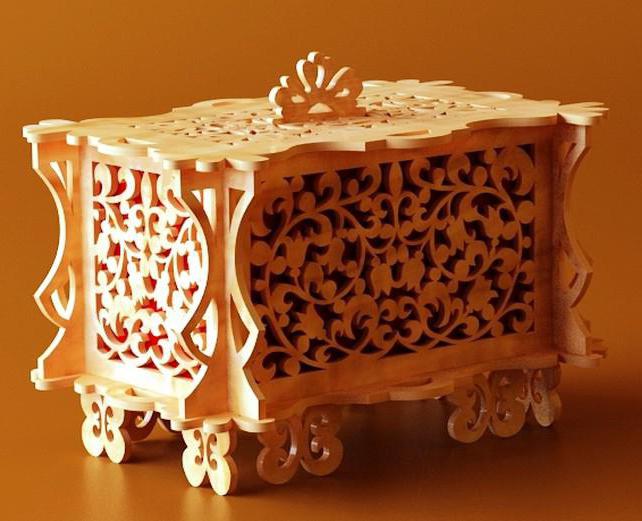
Where to buy wood for carving
There are many places where you can get material for work, the main thing is to find high-quality and dry wood. For example, good blanks for carving are sold in specialized stores for fans of handmade and art salons. In addition, you can buy suitable boards in building materials stores or at timber trading bases. And small furniture manufacturing enterprises and carpentry workshops are a real storehouse of dry wooden scraps of various sizes. For joiners, such waste is no longer of value, therefore, as a rule, they are given away for free.
Another option is wooden packaging (boxes, pallets). From one such product, one and a half to two dozen blanks will be obtained.
Wood Drying Rules
It should be remembered that for grooved and other types of carving, only well-dried wood should be used, so as not to observe with regret then how the finished carved product, when dried, warps and crackes. Drying of the workpieces should not be carried out in the sun or near heating appliances. Wood should dry arbitrarily in a warm room with good ventilation. It is better to put the boards on the ends, placing slats under them to provide air access to all sides. By the way, you can dry small workpieces in the microwave in several sessions.
The working process
Carved wood carvings, stencils for which must be prepared in advance, begin by transferring the design to a wooden blank. The background areas to be cut out are highlighted by hatching. Holes of a certain diameter are drilled near the lines of the pattern so that a saw blade can be brought into them.
Next, filing is done close to the contours of the figure. The narrow carvings of the hacksaws are carved, the stencils for which were selected complex, that is, with small parts and sharp bends. Sawing large parts with straight or smooth contour lines is carried out through wider blades.
Useful Tips
It should be noted that using large saws, you can get a ragged contour, so itโs better to prefer fine-toothed files. Drilling is recommended to be performed with pen drills, and this should be done on both sides of a wooden workpiece, after having previously drilled a through hole with a thin drill.
A great way to avoid torn edges and scuffs of wood is to stick thick paper on the back.
It must be remembered that the main factor ensuring the cleanliness of trimming is the sharpness of the tool, so you should take care of this side of the issue in advance.
When choosing an ornament, novice carvers should focus on simple images with large details and a minimum of "heavy" angles. Due to the correctly selected drawing, you can reduce the amount of work, resulting in a beautiful product.
Finishing a carved product
After removing the background, the product is refined to get even and clean edges of the picture. For stripping use steep and sloping chisels of medium and small size. Inaccessible places for chisel ornament places are cleaned with a sharp knife. Using these tools, the edges of the image are rounded off, cutting off a thin chamfer or choosing narrow fillets.
The chisel is recommended to be placed at a slight slope with respect to the work surface, moving it down and slightly to the side. This technique facilitates the finishing process and allows for a cleaner thread.
Processing slotted openwork products are performed on both sides. After trimming the contours with chisels, the cut-out pattern is cleaned using files, grinding bars and emery skins.
Modeling of the ornament is made in accordance with the applied thread - embossed or flat-embossed.
The technique of flat-relief slotted carving is used, as a rule, for the manufacture of decor for furniture, cornices, window frames, shutters, etc. Relief openwork carving allows you to get more elegant products, so it is used to create female jewelry, screens, placeholders for doors of lockers and etc. By the way, openwork furniture doors look even more impressive if you pull a bright fabric from the back, against which the ornamental composition will look sharper and brighter.