Among the equipment used for metal processing, hydraulic listogib has gained sufficient distribution. It belongs to the category of universal devices and allows manufacturing parts with various parameters. Machines are used both to create complex reliefs and holes on the surface, and as a powerful press.
Description
Hydraulics are used on industrial equipment characterized by high productivity and the ability to process material with a thickness of about 3-4 mm. As an addition, presses and rotary beam elements act. The machine is set up using software control or manually, depending on its type.
In large-scale production, a hydraulic hydraulic bending machine with CNC is most often used. This is facilitated by the possibility of obtaining within a short period of time many products in accordance with the specified parameters and with a minimum amount of marriage. For smaller production, a programmed device is also relevant due to the storage of product parameters of any shape. The release of the selected type of product begins with the press of just one button. In some cases, it becomes necessary to replace the matrix, but it takes no more than five minutes.
Devices equipped with software can be quickly configured to produce new elements using a remote display, a control panel located on the device, or a special program. The four-roll hydraulic bending machine is notable for its ease of use and the ability to perform tasks that are beyond the power of other varieties. Using it, you can create parts that have a square, oval and triangular shape.
Design
Despite the fact that presses for bending metal are based on a single scheme, they can differ in the list of additional functionality, memory size, dimensions, templates used and power.
The production of hydraulic sheet benders consists of many stages, the basis of the design is made up of the following elements:
- data system;
- controller;
- sensors that track speed;
- hydraulic and cylindrical elements;
- matrix;
- moving traverses and guides;
- bed.
DIY hydraulic bending machine
At the heart of the bending machine, which you can make yourself, is a special traverse. Such equipment allows you to process metal sheets with a width of 50 cm. Bending is performed by means of the pressure of the beam, while the base of the workpiece is fixed in a vice or using clamps. To obtain a 90 degree bend, it is recommended to supplement the design with a tab in the form of a metal strip. The hydraulic bending machine includes a punch and a die. The latter is installed on the workpieces, and the matrix acts as a substrate for the material.
The first step in the manufacture of the machine is the calculation of the applied effort and the cost of materials, the order of components, the determination of the dimensions of the structure and the total mass. When fixing parts, it is worth restricting the use of welding, since such joints are not designed for alternating loads. Elements that cannot be performed at home must be ordered in advance from the milling machine operator.
A T-bar hydraulic bending machine can be made at minimal cost, this will require several pieces of a large I-beam, channel, bushings, rings for springs, a punch and materials for the matrix. The frame of the structure is made of an I-beam, the lower part of which is fixed on the channel. The stand for the bending machine can be made of any suitable material, its dimensions are selected in accordance with the installation location of the device. The upper movable part of the structure is equipped with a jack. The angle of the matrix should be less than 90 degrees. As a clamping bar, a tee can be used on which metal plates are fixed. Holes are drilled in them with a size slightly larger than the diameter of the bolt.
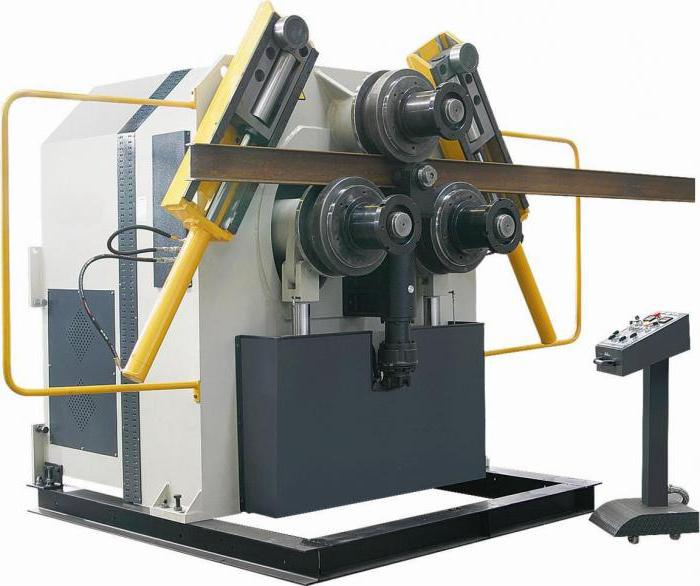
The spring should raise the bar by 6-8 mm, if necessary, it can be cut. Then a bolt is inserted into the hole of the bar, the spring is fixed, and the nut is screwed. Work with the bending machine can be simplified by supplementing the jack valve with a handle in the form of a valve.
Principle of operation
The principle of operation of the hydraulic machine is to issue an element from the workpiece in the form of a strip or sheet in accordance with the specified parameters. The adjustment of the device is made depending on the required characteristics. Of particular importance is the lowering distance of the clamping mechanism, the return speed, the degree of pressure and the crosshead speed. The press is suitable for processing metal with a thickness in the range of 0.5-5 mm. There are also narrow-profile varieties designed to process material with a larger thickness.
What you need to know
At the bending point, there is the possibility of residual deformation, which is controlled by adjusting the feed rate. Thus, even at high speed, material breakage can be avoided. Electromechanical and pneumatic devices emit a fairly high level of noise during operation, while manually operated equipment or CNC equipped do not have such a disadvantage.
Features
Hydraulic bending machine is suitable for the manufacture of products with an extensive degree of bending, as well as to obtain parts of a semicircular and conical shape. Devices of this type do not have smooth adjustment and high power, so they are not always convenient when working with non-ferrous metals and blanks of sheet material.
Among the varieties of bending machines, it is worth highlighting crank equipment, which is based on an electric motor with a drive that ensures the movement of the matrix as a result of shaft rotation. Such equipment is controlled by a lever or pedals, the setting can be either software or manual.
How to choose
Hydraulic bending machines are quite expensive devices, therefore, special attention should be paid to their capabilities and characteristics. Functionality should fully ensure the performance of production tasks. The purchase of CNC equipment is not always justified for workshops and small workshops, as the costs will pay off for too long.
There are key characteristics that must be considered when selecting machines. These include the following:
- the possibility of using CNC;
- complete with profiles and inserts;
- distance between working racks;
- crosshead height.
Varieties
Hydraulic bending machine can be produced in stationary and mobile versions. The latter has a smaller range of processed metals, but it is not without advantages, such as minimal power consumption, low weight, the ability to move to various objects.
The most widely used stationary industrial bending machines. This is due to the possibility of using various blanks and obtaining parts with the required configuration. They are also convenient for the production of bulk batches of products. The use of programs of varying complexity ensures the release of material with sufficient thickness, while the accuracy of processing is not lost.