The practice of using firewood as fuel in our time, even in relation to boiler equipment, seems morally obsolete. Nevertheless, this principle of operation of energy systems has undeniable advantages, which, accordingly, is reflected in the emergence of new technological concepts. In this case, a gas generator is considered, the operational features of which have long attracted the attention of designers from the automotive industry. Of course, there is no question of traditional firewood under the hood, however, the energy generated by such units is directly related to the burning of solid fuel.
Designs of gas generating equipment

The equipment consists of a converter, a fan, a scrubber, a pipeline supply infrastructure, a combustion chamber and connecting accessories. The design focuses on the conditions of thermal processing of solid fuel in order to generate heat or electric energy. This can be a monoblock or modular installation with the ability to perform the replacement of individual elements. Component housings are made of metal (sheet steel) by welding assembly. A metal platform is mounted at the bottom, which can be supplemented with a running gear, depending on the specific construction solution. In the upper part, a loading system with a hopper is usually organized, to which oxygen supply channels are connected. In industrial gas-generating plants, mechanical bodies for fuel loading with automatic adjustment are sometimes provided for generating electricity. But in this case, the combustion chamber must be provided with special indicators that will give a command to make the next portion of fuel.
Functional areas of the gas generator
The entire internal space of the unit can be divided into four departments:
- Drying area. A kind of fuel preparation chamber, in which the same firewood finds its optimum temperature without excess moisture. Typically, the temperature in this area is 150-200 Β° C.
- Dry distillation zone. Another step in the preparation of solid fuel, but in conditions of higher temperature conditions up to 500 Β° C. At this stage, the gas generator sets carbonized wood to remove tar, acids and other undesirable substances from them.
- Burning area. This department is located at the level of connecting the air channels through which air is directed to maintain combustion stability. Structurally, this is a conventional combustion chamber, which is present in all solid fuel boilers. The average temperature in it varies from 1100 to 1300 Β° C.
- Recovery zone. The section between the grate and the combustion chamber. By analogy with modern pyrolysis boilers, this department can be represented as a place of re-combustion. Hot coal enters here from the combustion zone, which can be removed or disposed of immediately.
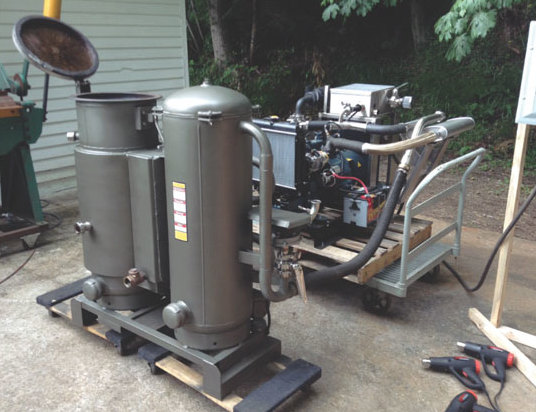
The principle of operation of the gas generator
The workflow of this equipment is based on the incomplete processing of carbon emitted during fuel combustion. Solid fuel elements can be both wood with coal and biomaterials like peat briquettes, pellets or pellets from waste from the wood processing industry. The resulting carbon, when interacting with the supplied air flows, can attach oxygen atoms to itself. The resulting gas can potentially give off a volume of energy corresponding to only 30% of the initially loaded fuel from which it was generated. On the other hand, carbon processing requires much less resources - at least oxygen is required in a minimal amount. And already in the process of secondary combustion, the gas generating unit produces target energy suitable for use. At this stage, various converters and storage batteries may be involved, depending on the type of energy that is planned to be obtained from the gas-air mixture.
Capabilities of gas generating equipment
Combining the principles of burning organic fuels with gas production was considered as early as the beginning of the 20th century. Moreover, there were successful practical developments in this direction, which replaced the more common at that time generators for processing renewable energy sources. Today, against the background of the popularization of the principles of rational use of resources with a focus on energy conservation, the concept of thermochemical conversion of waste and plant biomass is again becoming relevant. And even small-capacity gas generator sets of 70-80 kW can be used in municipal or agricultural enterprises, where local industrial waste will be used as fuel. For example, there is a practice of operating such plants in irrigation systems of farms in full autonomy for 4-5 hours. Equipment from 150 kW finds its place in large enterprises, in servicing areas and large energy-dependent facilities.
Application of gas generation technologies in industry
For the first time, gas-generating technologies began to be applied in the glass and metallurgical industries in Europe, and in the USSR they found their place in the national economy. For example, in the middle of the 20th century gas generating stations were distributed throughout the country, generating up to 3 MW from plant biomass and peat. Modern equipment has significantly increased in technological development. Today, these are entire complexes provided with automatic and even robotic control under computer control. The capacity of gas generating units for generating electricity in the industrial sector averages 300-350 kW. In some cases, these are entire chemical plants that impose stringent requirements on fuel materials. Such installations are used in large industrial complexes for servicing several consumption systems at once - power units (machine tools, assembly lines, dynamos, compressors), lighting devices, ventilation infrastructure, etc.
Gas generators in transport equipment
The practice of finalizing cars for installing gas generators began in the pre-war years. A high-efficiency electric generator was installed on many machines as part of this modernization, since it was necessary to provide a sufficiently powerful flow of oxygen pressurization. For this, an electric fan was used. The most notable developments of this type include the GAZ-AA "one and a half" and "ZIS-5" three-ton trucks, the gas generating units of which provided mileage at one gas station of up to 80-90 km. This is not much, but in the conditions of a shortage of liquid fuel in forestry, this decision fully proved itself economically. As for today, the transformation of conventional cars with ICE is also motivated mainly by the interests of energy conservation. There are successful examples of remodeling GAZ-24 and AZLK-2141 cars, which drive up to 120 km at one gas station, maintaining high-speed mode in the range of 80-90 km / h.
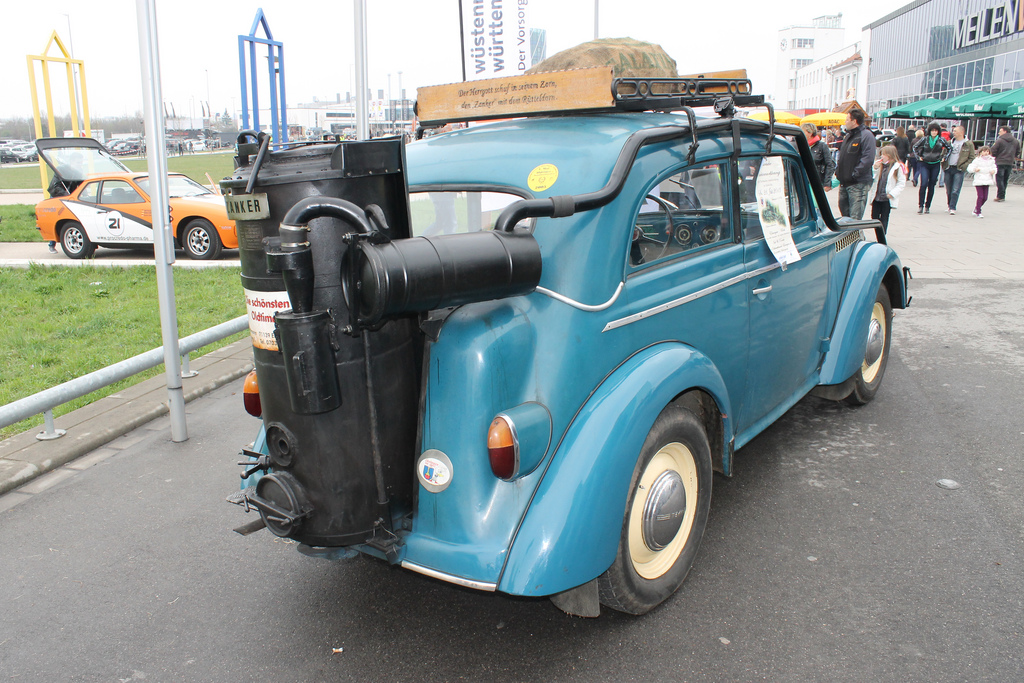
How to make a gas generator for a car with your own hands?
You can implement this principle without resorting to specialists at home yourself. The general instructions for such modernization can be represented as follows:
- A loading bunker is organized. Usually use a gas cylinder with a capacity of 40-50 liters. The bottom is cut out in it, and a hole or a window is made in the neck for filling fuel. You should focus on the use of either fine-grained coal or pellets.
- The grate is mounted to take on the main load.
- A cyclone filter and lance are made, which will absorb the heat load. Regardless of the type of solid fuel used, it will emit combustion products in the form of ash and dust. These wastes should be collected immediately after discharge by the filter.
- Mounting a radiator. This component will perform the function of cooling the gas mixture. For a gas generator installation, you can make a radiator design of plumbing pipes with your own hands. It is only important to correctly calculate the cross section for optimal carbon preparation.
- Creating a fine filter. From modern membrane materials it is possible to produce a shutter for multi-level cleaning of the gas-air mixture, which will increase the power of the energy generator.
- Connection to the engine. The final stage, during which, using commutation pipes, the motor is connected to direct the cleaned gas mixture to it.
Household gas generators
Home boiler equipment is also improving, complemented by new functionality and operational capabilities. Gas generators up to 150 kW for LPG (liquefied carbon gas) are offered in this area, complete with a liquid cooling system, a battery charging unit and protective devices. This is a full-fledged backup generator, which can be used in case of a power outage.
Calculation of gas-generating equipment by capacity
Regardless of the purpose of the energy unit, its technical and operational indicators should be calculated before purchase. The following is a typical example of calculating a gas generator for a home heating system.
The power of the unit should be averaged with the area of ββthe target operating room, bearing in mind the following relationship: 1 m2 of the power potential from the generated gas mixture per 10 m2. So, for a site of 50 m2, installation of at least 5 kW will be required, and if the area of ββthe production facility is 1000 m2, then a heating system of at least 100 kW will be needed. But that is not all. For each opening in the wall, an addition of approximately 1 kW is made, not counting the correction for climatic conditions. As a result, an object with a total area of ββ1000 m2 with 10 windows and 5 doorways will require the use of a unit with a capacity of 1015 kW as a minimum.
Technology advantages
Gas generators perfectly cope with the basic tasks of energy production. So, if conventional solid fuel units have an efficiency of 60%, then gas analogues - more than 80%. Positive nuances of service are also noted. Since complete combustion occurs in the chamber with the conclusion of the carbon dioxide mixture, special cleaning of the equipment walls is not required in the future. Of course, there are economic advantages. The simplest gas-fired gas generator can save up to 30-40% compared to electric heaters and boilers that provide a similar thermal effect.
Cons of technology
The advantages of gas generators could make them the main means of generating electric and thermal energy, if not for the weak points. These primarily include multicomponent functional parts. Despite the simple principle of operation, the gas generator unit contains many interdependent elements, which complicates the assembly and control of the system. It is also worth emphasizing the need to constantly maintain combustion by loading fuel raw materials. In the conditions of a working production, this must be done regularly, therefore, it will not be possible to do without controlling automation.
The future of gas technology
An organic combination with biofuel elements, which are unconditionally one of the most promising sources of combustible raw materials, speaks in favor of continuing the development of gas generating units. In the direction of optimizing designs for pellets and briquettes, it is more likely that this concept will move. As for gas generator sets for automobiles, at the industrial level, their development can also justify itself economically. By the way, about 2 kg of cheap fuel materials produce as much energy for a car as 1 liter of gasoline. However, the development process in this direction is still hindered by the need to complicate the design of cars and the emergence of ever new competitive generators, which also replace the usual ICE.
Conclusion
Electric and liquid energy generation systems today are increasingly opposed to alternative energy technology. For the same household environment, complete solar panels and geothermal batteries have long been produced. What place can a modern gas generator take in this competition? This is not the most practical solution to use for domestic use due to the large size of the equipment and troublesome maintenance. However, the industry is quite interested in such plants, since they allow us to count on impressive savings without reducing power.