In human activities, mechanical devices are often used. Reliability of work of moving parts in any mechanism is provided by reduction of friction and deformation. For this, special materials called antifriction are used. Their main purpose is to reduce the coefficient of friction, facilitating the sliding of moving surfaces of mechanisms. This article will examine the antifriction properties of various materials used for these purposes.
Types of friction
Friction occurs when bodies that touch each other move. There are two main types:
- Dry - the surfaces of solids are in direct contact. It is observed in belt and friction gears.
- Liquid - when there is an oil layer of liquid between the parts of the mechanisms and the bodies do not touch. It is found in thrust bearings, bearings.
And also distinguish between intermediate types of friction: semi-dry and semi-liquid.
Regarding the motion of bodies, the following types of friction are noted:
- rest - occurs with the relative rest of the bodies;
- slip - manifests itself in the relative movement of mechanisms;
- rolling - external friction when rolling bodies.
Depending on the type of friction, material with certain anti-friction properties is selected for the surfaces of the bodies.
Types of materials used to reduce friction
All antifriction materials providing a low coefficient of friction are divided into:
- Metal - alloys of three metals are used, in which copper (babbits) is present. Designed to operate in liquid friction mode.
- Powder - are based on iron and copper with the addition of graphite and sulfides. Used in plain bearings.
- Self-lubricating sintered - materials of various combinations of iron with graphite, copper and bronze are used for manufacturing. They are used for the production of plain bearings at low speeds and in the absence of shock loads. Good anti-friction properties allow them to be installed in places where it is difficult to lubricate.
- With solid lubricant components - as a thin layer, particles of a solid lubricant consisting of chlorides, metal oxides, fluorides, and plastic are applied to the surface of parts. Products operate at increased sliding speeds.
- Non-metallic - made of plastics: thermoplastic and thermosetting. Used for bearings of propellers, rolling mills.
- Metal-polymer - consist of heterogeneous components. They are divided into matrix, dispersed and layered. Used for the production of plain bearings, gears and sprockets.
- Minerals - use natural (agate) and artificial (corundum). They produce small wear-resistant bearings for tachometers, watches, gyroscopes.
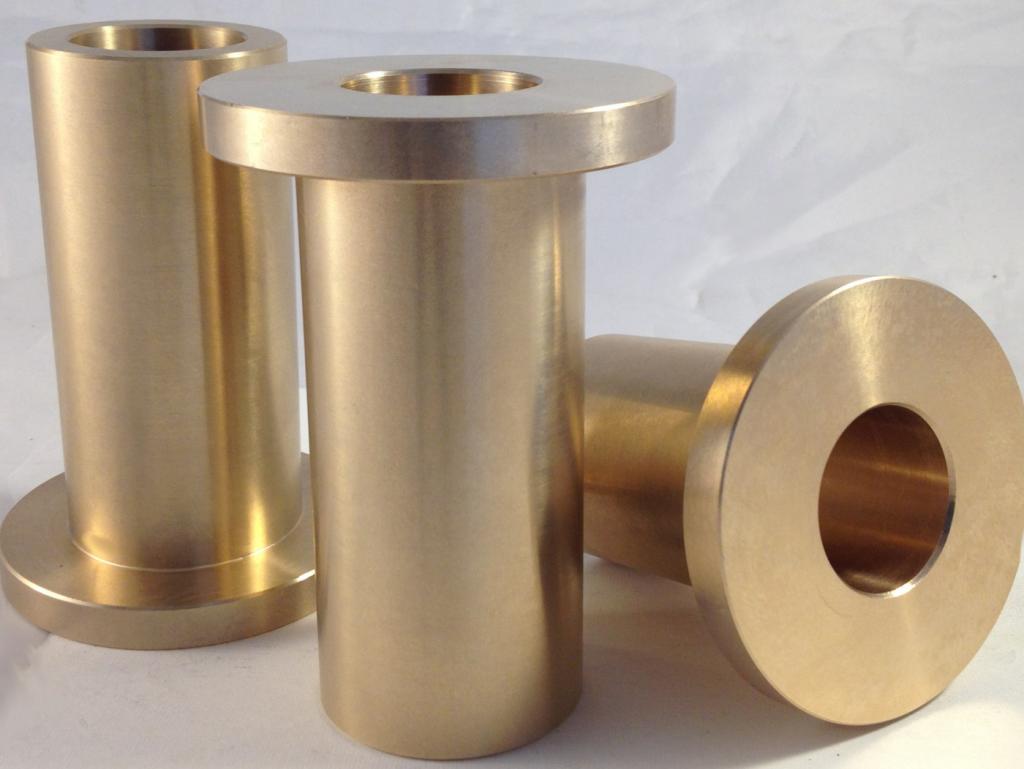
Each material finds its application for the production of parts according to its antifriction properties.
Low friction alloys
Friction bearing shells are made from such alloys, so they must have:
- Low coefficient of friction compared to the shaft material, which is most often made of hardened steel.
- Good thermal conductivity.
- Resistance to corrosion.
- Low hardness.
- A property that holds grease.
To satisfy the listed properties, the alloy structure should include metals with antifriction properties, which have increased softness and ductility of the base. And solid particles consisting of chemical compounds are already interspersing into it. In this case, the shaft is quickly run-in to the bearing, small grooves appear on it from solid particles, which are filled with grease and through which wear products are removed. Tin, lead, copper, cadmium, bismuth are taken as the basis, and blotches are made from alloys of antimony and copper.
The use of bronze alloys in friction units
Bronze is an alloy of copper with various metals, which may include tin, aluminum, silicon, lead, beryllium, and many other additives. Depending on the percentage of one or another element included in its composition, bronze is called tin, aluminum, lead. Bronzes are widely used in the manufacture of products that are used for high friction. The best are bronzes with antifriction properties, made on the basis of tin.
Particularly well-behaved are tin-phosphorous, from which the liners of supports are manufactured, working under significant load and at high speed. The only drawback is their high cost, so they are replaced by aluminum and lead bronzes. When working in an aggressive environment, bronze aluminum bearings are often used for bearing bushings. They, in addition to resistance to abrasion, have good corrosion resistance. Low coefficient of friction provides lead. Bearing liners are made from such materials for operation at high pressure and high speed.
Antifriction Alloys: Composition and Properties
In industry, for the manufacture of friction parts of mechanisms, various alloys are used that have a small coefficient of friction:
- Brass is an alloy whose main components are copper and zinc. It may include components in the form of aluminum, tin, lead, manganese and other elements. It is inferior to bronze in strength and a small coefficient of friction and is used in the manufacture of sliding bearings operating at low speeds.
- Babbitt - complex alloys having different composition and physical properties, but consisting of one soft base: tin or lead with solid additives from alloys of alkali metals, copper or antimony. Due to the soft base, the bearings are well run in to the shaft, and solid additives increase wear resistance. High antifriction qualities of babbitt, but lower strength than bronze and cast iron, make it possible to use them only for applying a thin layer to the surface of products.
Oil properties
In order to guarantee the reliability and efficiency of the rubbing parts, lubrication oils are used to reduce sliding friction. All of them are classified by:
- origin
- production method;
- destination.
Lubricating oils perform the following functions:
- reduce friction between the contacting surfaces of the parts;
- reduce wear and prevent teasing;
- provide heat removal from rubbing parts;
- protect against corrosion.
The antifriction properties of oils are their ability to reduce the amount of energy due to friction. Viscosity is the main indicator of these properties and is determined by the carbon and fractional composition. To improve the quality of oils, various anti-friction additives are produced, which allow to increase power, extend the operation of the unit, and reduce loads. They enhance the properties of oils, increasing the timing of the replacement of the lubricant. Anti- friction additives contribute to the creation of a protective layer during the interaction of parts, smooth their surfaces and smooth friction. By creating an oily, durable film, they reduce wear on parts.
Antifriction properties of epoxy polymers
Epoxy polymers are viscous liquids that harden when various organic substances are added to them. They have high mechanical strength, are used for adhesion of concrete, metal, glass and wood. Due to these properties, they are used for the production of metal-polymer parts, producing bushings, rollers, gears, bearings and couplings.
Fillers give products made of epoxy polymers high antifriction characteristics. Parts can work without lubrication if wetted with water. The coatings are resistant to atmospheric conditions and chemical environments.
Non-metallic anti-friction materials
For sliding bearings, two types of plastics are often used:
- Thermosetting - this includes textolite, which is used for the manufacture of rolling mill bearings, propellers and hydraulic machines. Parts are able to withstand harsh conditions, lubricated and cooled by water.
- Thermoplastic - polyamides are widely used: fluoroplast, capron, anide. Advantages are high antifriction properties of materials, resistance to corrosion and good resistance to wear at high loads and sliding speeds.
To reduce friction between the parts, various fillers are introduced in the form of solid lubricants, which, when used on the surface, create a structure of liquid crystals. It is worth noting that the fluoroplastic has a very small coefficient of friction, but poor heat dissipation and fluidity under load are considered a drawback, so it is used in conjunction with other materials.
Conclusion
Antifriction materials are suitable for the manufacture of liners and bearings, which are easily replaced when they are worn. Raw materials for the product should have a greater coefficient of friction, i.e., when parts come into contact, the hard-to-replace part of the mechanism remains without damage. This happens only when the material of a valuable part is endowed with excellent antifriction properties in front of the analogue.