Copper is a ductile metal that can be treated well and has electrical and thermal conductivity. To improve operational properties, various alloying components are introduced into its composition. This article will focus on the alloy of copper with nickel, which increases its resistance to corrosion, increases strength and electrical resistance.
What does the nickel copper additive give?
Nickel is introduced into the alloy as the main alloying component. It significantly increases the hardness of copper. Metals are endowed with a rare feature, they completely dissolve in each other. During fusion, depending on the proportion, homogeneous alloys of two metals change their properties as follows:
- Increases resistance to acids and alkalis.
- Increases heat resistance.
- Corrosion resistance is developed.
- Increases elasticity and strength.
- The temperature coefficient of resistance decreases.
Classification
Using mechanical, chemical and physical properties, as well as the scope, copper-nickel alloys can conditionally be divided into two main groups:
- Structural - characterized by high corrosion resistance and high strength. These include nickel silver, containing up to 30% nickel and small amounts of other metals, nickel silver with excellent strength and a special alloy of kunial with aluminum additives, which is well processed by pressure.
- Electrical - have a high electrical resistance. These include the Kopel thermoelectrode alloy, which contains a high content of nickel, manganin and constantan. Used in electrical engineering for compensation wires, thermocouples and rheostats.
Alloys are used for the manufacture of parts, are used in devices, heat exchangers, so they are subject to stringent requirements for chemical composition and physical characteristics.
Cupronickel
An alloy of copper with nickel, whose name is nickel silver, can contain up to 22% of the main alloying component of nickel, about 80% copper and not more than 0.6% impurities. He noted high strength, ductility, corrosion resistance. The alloy lends itself well to mechanical processing, it is stamped, cut, minted, brazed, polished, pressurized in any form (cold and hot). Cupronickel is available in the form of ribbons, stripes and pipes. The metal has a silver color. It goes to the production of condenser pipes, air conditioning parts, and is used in instrumentation.
In addition, medical products, inexpensive jewelry, coins and utensils are made of alloy. To improve the appearance of the product is covered with a thin layer of silver.
Nickel silver
Alloys of nickel, copper and zinc contain up to 35 percent nickel and 45 percent zinc, and the rest is copper. The nickel silver (translated from the German language as “new silver”) has a beautiful silver color, they are not susceptible to oxidation in air, and are stable in solutions of organic acids and salts. Due to the high corrosion resistance, non-ferromagnetic alloys are used in instrumentation and are used for the manufacture of medical instruments and clockworks.
In the manufacture of products for the jewelry industry, deoxidizers are added to the alloys, which can reduce the amount of copper oxide, increase ductility and strength. With an increase in nickel in the alloy, its hardness and strength increase. With the introduction of aluminum, the alloys become dispersively hardening, while corrosion resistance is also increased. The presence of lead in nickel silver gives the metal elasticity and improves machining.
High Resistance Alloys
For the manufacture of electric heaters, conductors are required that have a high specific and low temperature coefficient of resistance. Exact resistance for devices, as a rule, is made of manganins - this is an alloy of copper, nickel and manganese. It consists of 86% copper, manganese 13% and nickel about 3%. To stabilize, a small amount of iron, silver, and aluminum is introduced into manganins. Alloys have a high melting point of 960 degrees, the average density is slightly more than 8 g / cm3. and orange color.
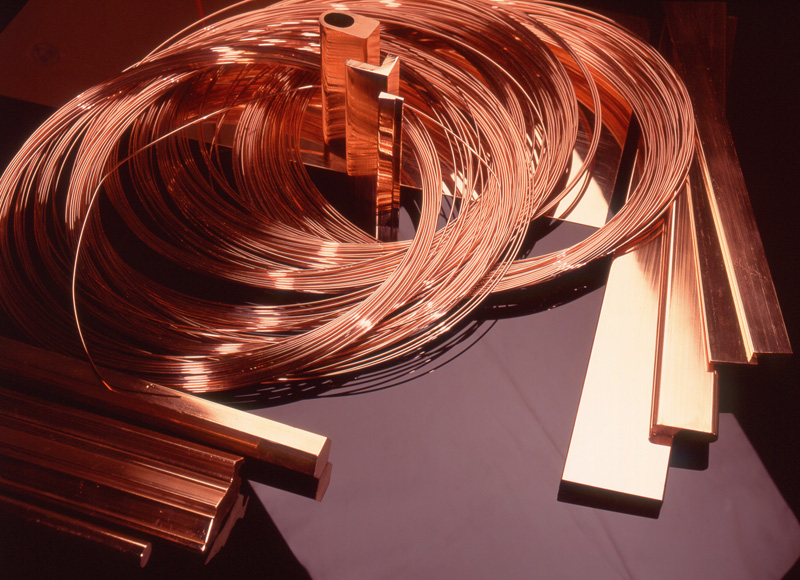
Manganins depend little on the temperature of electrical resistance, which is very important for their use in electrical measuring devices with a high degree of accuracy. Another advantage of the alloys is a very small thermo-EMF paired with copper. To stabilize the electromechanical properties, artificial manganin is aged. The wire is heated in vacuum to 400 degrees for about two hours, after which it is kept at room temperature for a long time to obtain stable properties. The alloy is used for manufacturing additional resistances, coils, shunts, and high-precision measuring instruments.
Constantan
Which alloy of copper and nickel, along with manganin, refers to alloys of high electrical resistance? This is constantan, it contains up to 65% copper, up to 41% nickel and about 2% manganese. This alloy has a specific silver tone, medium density and a melting point of 1270 degrees. The industry produces constantan wire, the diameter of which is 0.02-5 millimeters. Significant thermo-EMF paired with copper limits the use of alloy in precision electrical meters. But it finds application in thermocouples for measuring temperatures up to 300 degrees.
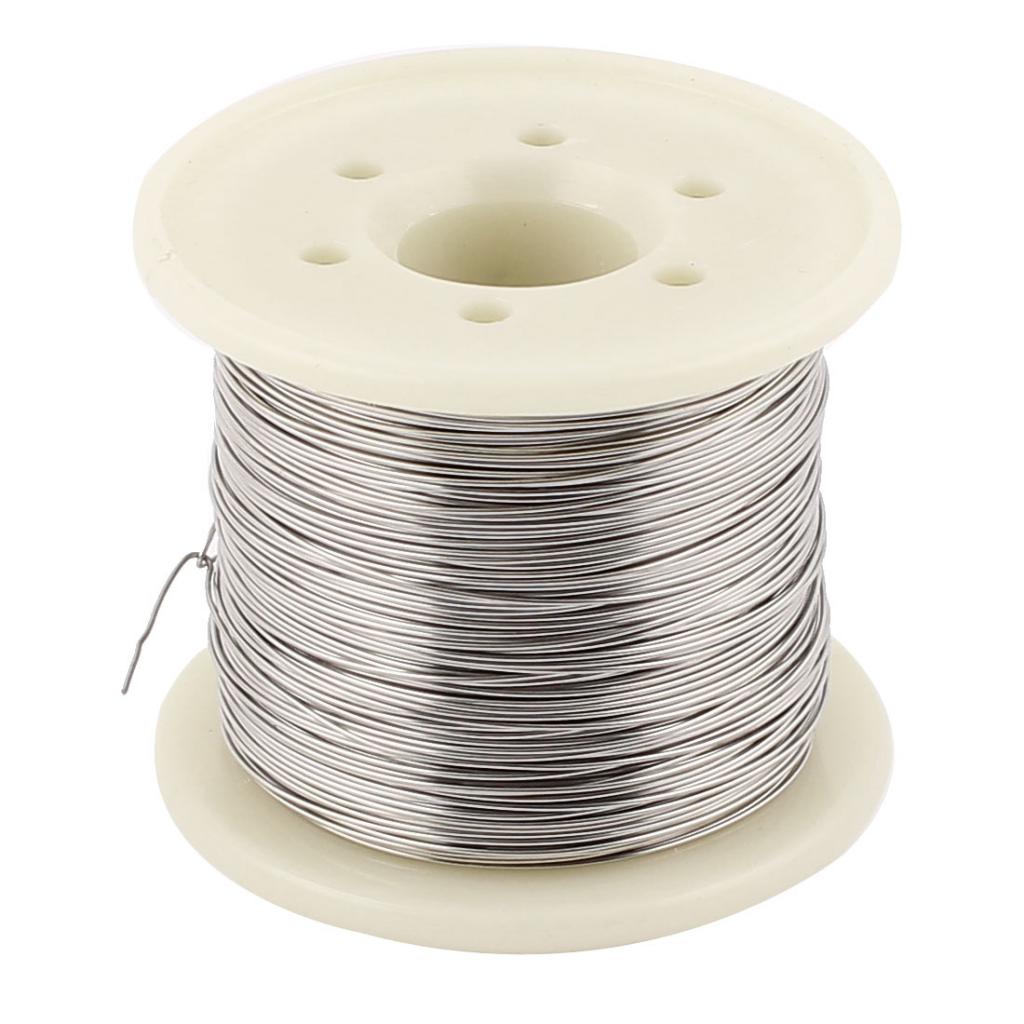
The constantan wire from an alloy of copper with nickel is subjected to special heat treatment by heating it to 900 degrees and subsequent cooling. As a result, a dark gray oxide film forms on its surface, which forms an insulating layer and does not require additional protective coating. The alloy lends itself well to machining; therefore, it has high technological properties. It finds application in measuring instruments, electric heating elements and rheostats with temperatures up to 400 degrees.
Conclusion
Alloys of copper and nickel are used in various industries. They are plastic and have anti-corrosion properties. Of them make parts that have a responsible purpose, used in heat exchangers and devices. Therefore, strict requirements are imposed on alloys in terms of density and chemical composition.