Domestic construction has long been focused on the use of large and heavy frame elements, thanks to which strong and reliable structures with high bearing capacity are built. However, in today's market, given the desire of consumers to reduce financial resources during construction, the situation has changed in the opposite direction. This process, in particular, illustrates the proliferation of I-beam wooden beams for flooring, which in Canada and North America are used for the construction of modular-frame houses.
Concept
Replacing capital solid and durable structures provides many advantages, including expanding the construction capabilities of the upper parts of the structure. It is these functions that the I-beam system provides, combining the rigidity of monolithic beams and the functionality of lightweight construction trusses. Classic solid logs are irrational to use on the top floor, as they overload the base supporting frame. In turn, I-beam wooden beams for floors form sufficient structural support, but do not reduce the quality of primary tasks. An analogy when comparing reinforced concrete or monolithic wooden structures with elements of modular-frame structures can be taken from the example of reinforcing bars. Conventional thick metal rods are successfully replaced by thin, lightweight fiberglass products, which retain the same strength characteristics.
As an element of overlap
First you need to deal with the technical features of the ceiling in private homes. This design, which is a horizontally located element of a tiled shape, which performs a protecting or retaining bearing function. In ordinary single-story houses or cottages, the ceiling acts as a kind of partition, separating the ground floor from the attic or attic in terms of altitude. Therefore, it is worth considering initially wooden I-beams in ceilings and rafter systems as an element with two-sided functionality. Depending on the arrangement of the roof, the I-beams can be pressurized and support stands from the roof covering. As for the design of the ceiling itself, its basic skeleton will be stiffeners, which will be guided along the Mauerlat from one wall to the opposite. That is, I-beams will form a power frame already for the installation of less critical and mostly decorative structural elements, for example, sheathing from wood-based materials.
Device
It should be noted right away that the principles and manufacturing technology of a building I-beam have been formed for a long time, and in the mid-20th century, assembly was carried out on the basis of the same monolithic bars and an intermediate dividing strip. However, the layout method has not fundamentally changed. This is the same system that consists of a central wall and two power rails. Today, an I-beam wooden beam-beam for the installation of floors is made of oriented particle board OSB-panel and LVL-bars (glued beam). On the one hand, the high technical and operational qualities of the I-beam are ensured by a unique combination of the physical properties of two modern materials, and on the other hand, by the layout itself, in which the bearing capacity is optimized while maintaining optimal size and weight indicators, which also eliminates overloads relative to the building frame.
Operational features of the overlap
The practice of moving from solid dimensional beams and floor structures to optimized I-beam technology demonstrates the following structural features of the structure:
- There are practically no restrictions on the fastening of the already mentioned skin to the edges of the I-beam. By means of mechanical rigid fasteners or by gluing to the supporting skeleton, it is possible to fix chipboard, MDF, plywood and even laminated panels if necessary.
- Beams at a height even without additional support due to the complex and heterogeneous structure provide the necessary floor stiffness sufficient to eliminate the likelihood of deflection.
- The use of floor rough coatings with a thickness of at least 2 cm can significantly increase the stiffness of I-beam wooden beams. For interfloor ceilings or in the separation of the attic, this is especially important, since higher loads will be placed on the upper level.
- Much will still be determined by the method of installation and, in particular, by the type of fixing materials. But in this part, it is worth emphasizing that manufacturers are expanding the range of modified beams with locking joints and groove fasteners, which, in principle, allow you to do without building glue, brackets, jumpers and hardware during installation.
- The use of auxiliary struts and locks when applying ceilings without power strapping can minimize floor vibrations, while also reducing the risk of creaks.
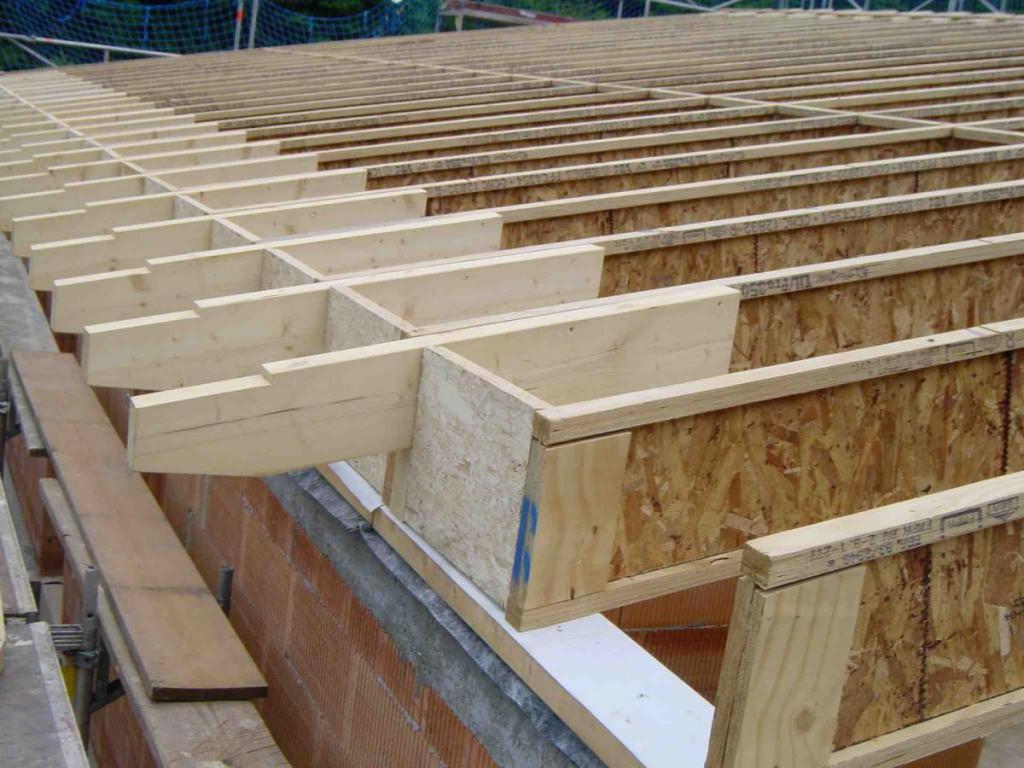
Varieties
Wooden beams of this type are mainly divided according to size. But there are certain unified output formats as well as products that are individually calculated for specific conditions of use. In both cases, size ranges are noted in which the following types of I-beam wooden beams for floors are conventionally distinguished:
- Models for short spans. The height of the beam is 240-300 mm, and the maximum width reaches 38-40 mm. Suitable as a modular element in ceilings for small suburban buildings.
- Universal beams for commercial and residential buildings. In this case, the height can reach 400 mm, and the thickness is 64 mm. The expansion of the installation area by increasing the size of the bars gives more opportunities for laying rough coatings.
- Massive beams for frames under high load. The height reaches 450 mm and the thickness is 90 mm. Such elements are mainly used in industrial and commercial facilities, where, in principle, the use of wood in supporting structures is allowed. As for the private sector, in such projects, such beams can be used as rods of the roof truss system or Mauerlat.
Determination of the load on the floor beams
The main task of the designer at the stage of development of the overlap scheme is to assess the potential load on the bearing elements. It should be repelled when selecting I-beam wooden beams for flooring in size. It is also important to determine the step in the placement of stiffeners. For example, the constant static load expected in the attic is 50 kg. For the margin for dynamic load, the base value is multiplied by a factor of 1.3 to 1.5, depending on the type of load. So, the output can turn out 75 kg. This indicator takes into account its own floor load, but depending on the objects that will be placed in the attic, this value can increase several times. To it is worth adding weight from auxiliary reinforcing and heat-insulating materials.
Calculation of I-beam wooden beams for flooring
First of all, it must be emphasized that each beam receives a kind of passport at the outlet, which indicates all the basic physical and technical characteristics with an allowable weight load. Even if these parameters correspond to different elements, the load power can be different, since other factors influence it - from the wood species to the manufacturing technology. The standard calculation of I-beam wooden beams for overlapping is made in height and width - indicators that vary from 100 to 450 mm and from 30 to 90 mm, respectively. At the same time, the height is selected based on the proposed insulation layer and the planned laying of communication channels. Even a minimum value of 100-200 mm is enough for a group of stiffeners to withstand a load of 200-250 kg. If necessary, the lack of power of the beam can be compensated by the frequency of its location - the indentation varies from 0.5 to 1.5 m.
Do it yourself
There is nothing complicated in making an I-beam. Materials such as OSB boards and glued beams are now available on the market in various formats. What is required from the contractor during installation? Only skillful handling of the tool and accurate calculation of the geometry of the elements. A plate of suitable width is installed on both sides in the prepared grooves of two bars along the entire length. Actually, the main task is to form these grooves. This can be done with a jigsaw and a chisel of a suitable format. As for fastening, I-beam wooden beams for floors are held and pressed by their own weight during operation, therefore, special physical fasteners are not required. There is enough glue to fix the OSB-plate in the grooves for the duration of the installation activities.
Installation technology
There may be different mounting configurations that vary in basis material, abutment method, and load requirements. So, brick walls, wooden elements, concrete slabs and metal structures can act as a basis. In each case, the installation of wooden I-beams for overlapping is carried out using the appropriate mounting hardware:
- A galvanized corner will help to complete the tying with the elements of the rafter system.
- The joining of the beam to a brick or concrete is made out with a metal clamp.
- The oblong bow lines, regardless of the base material (including those with transition sections from brick to wood), are made using mounting metal tapes.
- Responsible nodes-joints of the ceiling with the walls are provided with coupling clamps.
Technology benefits
According to expert reviews, the following operational factors can be attributed to the advantages of an I-beam:
- Almost perfect geometry, which facilitates subsequent work on the device roughing.
- High strength. The rigidity of glued beam beams virtually eliminates bending moments and structural deformation.
- Wide possibilities of combination with other materials. Having selected the optimal dimensions of an I-beam wooden beam for overlapping, you can organically fit a heat insulator into their niche - even a small format with a height of 250 mm and a bar width of 30 mm will allow you to integrate small polystyrene foam panels or mineral wool panels.
- High soundproofing. Again, a unique combination of beam components minimizes vibration and noise due to the damping effect.
Functionality
According to reviews, one of the key advantages of the I-beam is that it forms free space due to the grooves between the stiffeners. Using closure devices, it is convenient to lay engineering networks in them - pipelines, electrical wiring and other lines that require hidden wiring. In this sense, the advantages of I-beam wooden beams for floors over conventional monolithic structures will be in two points. Firstly, there are niches for convenient installation of the track. Secondly, the absence of restrictions associated with the contact abutment of the same electric cable or pipe with hot coolant to the surfaces of the beam. Both the OSB board and the glued beam in the I-beam are subjected to special processing, which makes such a pair possible.
Conclusion
This technology is beneficial as a universal structural solution in modular-block construction of houses with different characteristics. This is also confirmed by reviews of I-beam wooden beams for floors, in which both the convenience of installation and the technical and operational advantages of the material are noted. As for the economic factor, then, as noted by consumers, the I-beam in some modifications is really more expensive than conventional beams. But this difference is compensated by the reduction in transportation costs and handling measures, as well as the high durability of the structure, which does not require special maintenance.