Before you begin installation of the final coating of the concrete floor, it is necessary to prepare the base. In this case, we mean the assessment of the state of the surface. First of all, the base must be smooth, free from cracks and other defects. The final result of the finish will depend on the quality of the surface. Before impregnation, dust removal and processing with paints or varnishes, the concrete floor is polished. Next, we consider this process in more detail.
Processing benefits
When applying a polymer coating, for example, a competently performed work to level the base will ensure reliable adhesion of the surface to the finishing material. Grinding enhances the practicality of the floor. In this case, the surface does not require special care after work. This, in turn, significantly reduces operating costs. Properly performed floor polishing eliminates the need for frequent restoration of the coating. Surface treatment allows you to create a perfectly smooth base. For many topcoats, this requirement is paramount. In the process of laying a bulk polymer floor, the stage of preparation of the base includes, among other things, grinding. An untreated base absorbs moisture. When the temperature drops to minus, water crystallizes, its volume increases. This, in turn, leads to the destruction of the material. Such damage is especially bad for the first floor.
Where is this coating used?
Surfaces treated in this way are widespread in stores, office buildings, hangars and warehouses. Such a processing method is also popular in residential premises. The polished floor is appropriate in any interior. Such coverage is arranged on playgrounds and other outdoor outdoor facilities. As is known, concrete is highly resistant to aggressive factors and mechanical stresses. The latter allows you to lay the coating in places with high traffic.
Process description
Sanding the floor is one of the varieties of building foundation construction. It is necessary to remove the old coating layer. Grinding concrete floors is one of the most common surface leveling methods. Preliminary processing of the base is thus carried out on the third to fifth day after pouring. The final grinding of the floor is done after the mortar has completely hardened. During the process, contaminants and defects are eliminated (cracks, ripples, chips, nicks, local influxes). If the screed is new, then polishing the floor allows you to remove lime milk from the surface. If the base is old, the upper damaged layer is removed during processing. After completion of work adhesion increases and the entire surface is "refreshed". It should be noted that strong wave differences in the screed floor polishing does not eliminate. In fact, the equipment moves along the surface, repeating its profile. Eliminate high-altitude differences can only be re-filling the base.
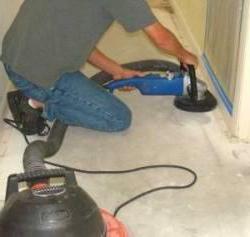
Types of processing
Sanding the floor can be done dry or wet. Depending on this, the cost of work will be established. However, in either case, one equipment is used. The tool must have the ability to cope with stone and concrete surfaces.
Wet method
Such polishing is used for floors coated with marble chips or mosaics. The technology in this case involves the use of abrasive elements. The result is an almost perfect base. The surface is no different from polished. In the wet grinding process, water pumps are used.
Dry way
For concrete screed, experts recommend using this option. It must be said that dry grinding requires more time than wet grinding. In addition, a large amount of dust rises from the surface during operation. However, it is still better than wet cement slurry covering the eyes. With dry grinding, visibility is better, which allows you to fix errors almost immediately. An industrial vacuum cleaner can be used to eliminate dust .
Tools and equipment
Do-it-yourself sanding of the floor can be carried out by devices that are sold in any hardware store. Most of the instruments presented on the shelves are of European production. Among domestic products worthy options for today are few. Some masters grind the floor with a grinder. However, as practice shows, treating the surface with this tool is quite problematic. But, according to experts, a grinder will be enough for grinding in a living room. In this case, it is impractical to purchase expensive equipment. In addition, a grinder can be reached in hard-to-reach places, which is impossible to do with a large machine. For surface treatment, a diamond bowl, an abrasive disk, two nozzles are required.
The cost of work
Processing in this way is carried out not only on the screed. Polishing of a wooden floor is also quite common . When laying parquet, for example, this stage is an integral part of the installation. Prices for services today are different:
- Grinding a wooden floor, the area of ββwhich is not less than 20 m2, in any condition of the surface with the subsequent application of three layers of varnish - 250 r / m2.
- Improved processing quality. In this case, 2 types of tools are used, at the end of work the surface is covered with three layers of varnish - 500 r / m2.
- Grinding floors with an area of ββless than 20 m2 - 300 r / m2.
- Removing the paint layer with subsequent application of varnish (or without it) - 400 r / m2.
- Grinding with a small abrasive. In this case, the surface is not varnished, but is prepared for laying any kind of coating - 180 r / m2.
- Processing for painting - 140 r / m2.
- Grinding of concrete or sand concrete floor with brand strength not more than M300 - 80 r / m2.
- Surface treatment with polymer coating. In this case, the material is completely eliminated and leveling is carried out - 110 r / m2.
- Grinding a concrete base with a brand strength of more than M300 - from 90 r / m2.