The end mill is a metal-cutting tool widely used in mechanical engineering, designed for processing various planes, ledges, grooves and shaped surfaces of complex geometry. The main feature of this tool is the ability to simultaneously process two perpendicular planes, due to the presence of teeth on both the cylindrical and the end surface of the cutter.
At its core, a face mill is a multi-blade metal-cutting tool of a cylindrical shape, where each tooth is an independent cutter. Due to its design and high speeds of the machine, a high degree of purity of the surface processed by milling is achieved. When the tool rotates, its teeth (cutters) come into contact with the material alternately.
The end mill when performing a metal-cutting operation is perpendicular to the machined plane of the part. The main cutting load is borne by the cutting side edges located on the outer cylindrical surface, which contributes to their rapid wear. Of course, end mills can be re-sharpened, but after such an operation, their dimensions will invariably differ from the nominal ones.
In this regard, prefabricated cutters with interchangeable cutters made of various grades of high-speed steels and equipped with brazed carbide inserts or cutting elements made of cermet are especially popular. Such cutters and plates are fixed directly to the tool body. A distinctive feature of this type of milling cutter is a fixed installation of the cutting element relative to the tool body. End mills of this design have a constant geometry, determined by the accuracy of the corresponding basic surfaces of the tool body and the configuration of removable non-turning plates.
The main advantages of such a structural solution include increased strength, due to the absence of internal stress of the metal, usually caused by regrinding. This increases the resistance and durability of the cutters by about thirty percent. In addition, such mills equipped with removable plates can significantly save carbide material, since used cutters can be sent to remelting, where tungsten and other expensive elements are extracted.
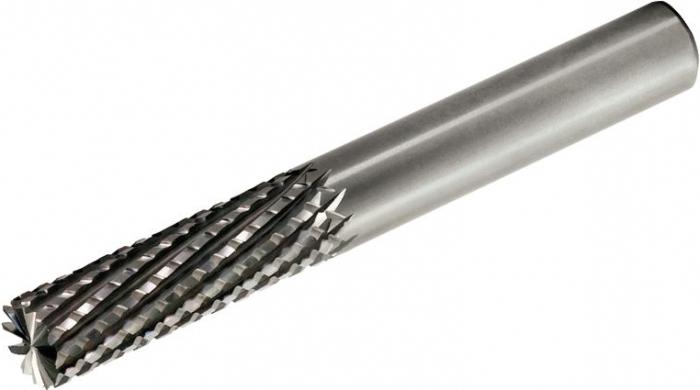
End milling is characterized by higher productivity than cylindrical. Nowadays, most of these operations are carried out precisely with face mills. The tooth geometry also deserves special attention. The cutting surface of each of them has sharpened at a certain angle working edges that pass through the top of the tooth. Distinguish between primary and secondary cutting surfaces. The top of the teeth of the end mill can have either a rectilinear shape or rounded contours. The latter option demonstrates increased wear resistance and less dependence on the degree of runout of the cutting edge. Such cutters are mainly used in roughing and semi-finishing.
For milling operations on the processing of small ledges and flat open planes, an end milling cutter is usually used, equipped with insert knives, which are made from various grades of high-speed steels. Such a model, mounted on the mandrel or the landing end of the machine spindle, usually has a diameter of 40 or more millimeters, which makes it a rather rigid and massive tool.