An antifrosty additive in concrete is a dry mixture or solution of chemicals that are characterized by a rather long shelf life. The main purpose of such an additive is to provide concreting work in the winter.
New complex antifrosty additives, in addition to adjusting the processes of building strength of concrete mortar, regulate a number of its rheological properties. As a result of lowering the temperature, setting time is reduced, the process of hardening of cement stone is accelerated, and its graded strength is increased by 2 classes.
Classification
Antifrosty additives to the solution (concrete) on a chemical basis can be divided into three main groups:
- Antifreeze.
- Sulphates.
- Antifrosty winter additives accelerators.
Let's consider them in more detail.
Antifreeze
This anti-frost additive in concrete reduces the freezing point of the liquid, accelerates or slightly inhibits the setting of the mortar. In this case, antifreeze does not completely change the rate of formation of structures.
Sulphates
Sulfate of iron, aluminum or other metals is an anti-frost component, the addition of which will ensure the fastest formation of a dense solution. The set of strength is also positively affected by the active generation of heat, which is accompanied by the interaction of concrete with hydration products. Such an additive cannot be used to lower the freezing temperature, since it completely binds to sparingly soluble compounds.
Antifrosty winter accelerator additives
Antifreeze additives in a solution (concrete) of this type increase the solubility of the silicate components of cement, resulting in the formation of double or basic salts with hydration products. Most of them simultaneously reduce the freezing temperature.
Varieties
- Potash is a strong antifreeze additive in concrete, accelerating the hardening process. In order to prevent a decrease in strength, potash is recommended to be combined with sulfite-yeast mash, sodium tetraborate or other retarders. The concentration in the mixture should not exceed 30%.
- Sodium nitrite is a fire hazardous poisonous antifrosty additive in concrete. In case of combined use with lignosulfonates, the formation of poisonous gases is possible. The dosage should be determined empirically and be in the range of 0.1-0.42 l / kg of cement mortar at ambient temperature from 0 to -25 ÂșC.
- Sodium formate is an antifrosty accelerator. It is used to improve plasticizing, water-reducing properties. It is recommended to be used together with naphthalene lignosulfonate. This antifrosty additive to concrete, the consumption of the mass of cement on average has 2-6%.
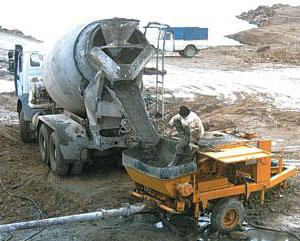
In order to organize concrete work in the winter period of time, in addition to the above, you can choose an antifrosty additive based on sodium formate for alcohol, urea, ammonia water or calcium chloride.
Benefits
- Plasticizes and stabilizes finished cement mixtures.
- Allows you to perform concrete work in the winter time.
- Helps to increase the durability of the mixture during the operation of the building.
- Improves the final frost resistance of the solution.
- Reduces shrinkage deformation.
- Reduces water release and delamination.
- Reduces installation costs.
- Excludes corrosion of internal reinforcing mesh.
The use of anti-frost additives in concrete as a whole will lead to significant savings.
disadvantages
- Some additives are considered poisonous.
- In order to reliably provide strength characteristics, cement consumption is increased.
- Sometimes the regulated power of a concrete brand falls.
Recommendations for use
The antifreeze additive is introduced into the concrete solution together with water, preferably with the last third of the liquid. It is undesirable to introduce the product into a dry mixture. After the additive has been introduced into the solution, it is necessary to wait a certain time to ensure its uniform distribution.
It is very important to adhere to the requirements for installation work in the winter:
- During snowfall, special shelters must be completed.
- Recommended solution temperature at the mixer outlet: +15 ÂșC to +25 ÂșC.
- To prepare the mixture, it is advisable to take heated water.
- Filler heating should be done immediately before use.
In order to obtain a mortar with the required strength characteristics, it is recommended to observe the concrete care requirements in the winter season in accordance with SNIP 3.03.01. It is advisable to take measures to achieve a strength of at least 20% of the design by the time the solution is cooled to the temperature at which the dosage calculation was performed.
Antifreeze additives in concrete: technical characteristics
Color | Gray |
Solution viability | At least 3 hours |
Bulk weight | 1300-1400 kg / m 3 |
Aggregate size | No more than 0.3 mm |
Use temperature | From +5 ÂșC to +30 ÂșC |
Compression density at the age of 28 days | Not less than 10 MPa |
Adhesive strength | Not less than 0.5 MPa |
Optimal application layer | 2-4 mm |
Consumption | 26-37 kg / m 3 masonry |
Frost resistance brand | F 50 |
Dosage
The dosage of antifreeze additives should be selected for each specific case by conducting tests in production and laboratory conditions. It depends on the following:
- Concrete care conditions .
- The temperature of the solution at the outlet of the concrete mixer.
- Ambient temperature.
- The material and chemical-mineralogical composition of the solution and the rate of curing.
- Brand strength cement.
When storing or using a large volume of the additive for a long time, it is recommended to periodically homogenize the solution by stirring or sparging with compressed air. Dosing should be performed with an accuracy of ± 2%.
Hardening temperature | Consumption of antifrosty additives for a warm solution in terms of dry consistency | Consumption of antifrosty additives for cold solution in terms of dry texture |
up to -5 ÂșC | 0.8-1% by weight of the solution | 1-1.2% by weight of the solution |
-5 ÂșC to -10 ÂșC | 1-1.2% by weight of the solution | 1.2-1.4% by weight of the solution |
-10 ÂșC to -15 ÂșC | 1.2-1.5% by weight of the solution | 1.4-1.8% by weight of the solution |
-15 ÂșC to -20 ÂșC | 1.5-1.8% by weight of the solution | 1.8-2.5% by weight of the solution |
-20 ÂșC to -25 ÂșC | 1.8-2.2% by weight of the solution | 2.5-3.5% by weight of the solution |
DIY antifrosty concrete additive
It is worth paying attention that the most preferred option will be to purchase a ready-made additive in concrete mortar in any specialized store. They are not so expensive, have a low consumption and at the same time provide a significant improvement in solution properties in winter with minimal negative consequences.
With a small front of work and an air temperature of at least 10 ÂșC, this method will be optimal.
However, it happens that a self-made frost-resistant additive in concrete is the only option. In this situation, one should pay attention to chlorides (salts). Chloride salts can significantly reduce the freezing point of a solution, reduce setting time and reduce cement consumption. But such an antifrosty additive in concrete (expert reviews confirm this) can only be used for unreinforced structures.
Precautionary measures
When working with a substance of this type, it is recommended to use protective gloves.
If exposed to exposed skin, wash off with soap and water. Anti-frost additive in the eyes is not allowed. In such a case, it is necessary to immediately rinse off the product with a large volume of water and consult a doctor.
The additive is disposed of in accordance with local regulations, and it is strictly forbidden to pour it into the sewers, ponds and soil.