A circular saw is a steel disk with cutters deposited on its edge and sinuses between them. They may look like solderings from an alloy harder than the substrate, or cut out of the shape of the body itself. The whole series of saw blades is called the ring gear, and the blade is called the blade. The frontal surface of each tooth is the front face, and the back is called the back. The distance between adjacent vertices of the incisors is called a step. In standard saws, the entire ring gear consists of the same pitch and height. As a result of the work, a hand-held circular saw leaves a cut in the wood - a gap limited by three faces.
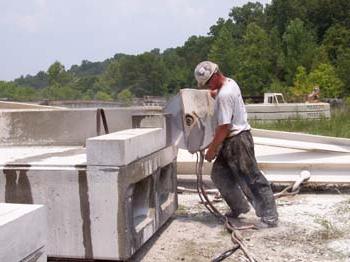
Sharpening a circular saw, as well as fine-tuning its teeth with carbide brazing, is carried out using abrasive (carborundum) wheels. The method can be combined: the first (rough) procedure is performed with abrasives, and the final one with diamond tools. To preserve the carbide alloy of the cutters and the properties of grinding wheels, pre-treatment is carried out due to the length of the blade - along the rear face, and thin - along the front.
Sharpening of the circular saw on the reverse side consists in grinding the steel part of the cutter at an angle α + 6 °. The thin carbide plate procedure uses an angle of α + 2 °, and the finishing of that part of the plate that is adjacent to the blade is an angle of α. The front face is processed by preliminary sharpening along the entire length of the soldering of the plate, and the final one by the front side (subject to the application of the finishing method, which should be carried out with the participation of continuous cooling). However, for diamond grinding wheels based on a bakelite bond, sharpening a saw blade in normal mode may be acceptable.
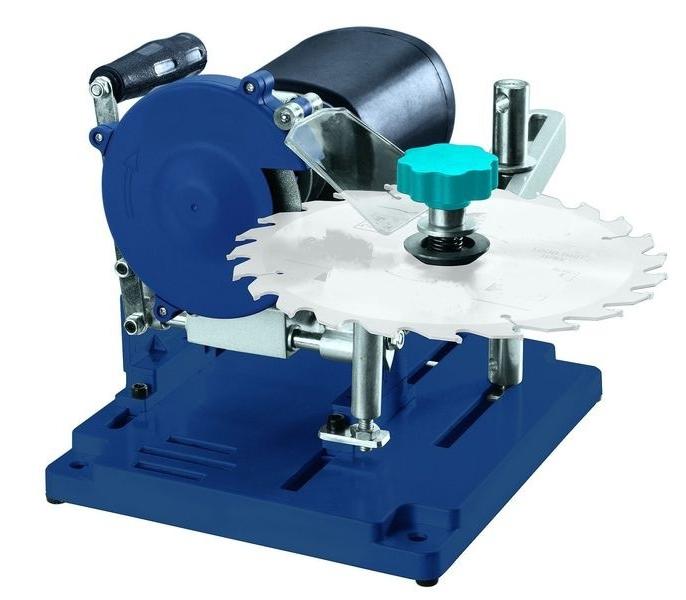
On modern machines that use tools of the combined type (two grains of grains - diamonds with abrasives), grinding is performed with continuous cooling in one pass with the removal of the allowance of 0.25 mm. Carbide saws exist where double-sided blades are used. Rearranging, they work on both sides, then they are allowed for processing in order to make new paintings. This sharpening of the circular saw significantly simplifies the maintenance of the tool house due to the centralization and enlargement of the enterprises used.
If the back face of the tooth is made flat and sharpening is done along it in parallel layers, during the wear of the cutter, its back angle is sharpened, and with a certain number of regrindings, it risks becoming unacceptably small.
Of course, you can treat the tooth along the plane of the back strip, which will keep it tilted. But such a measure will lead to a reduction in the angle of sharpening with a deliberate loss of accuracy of the cutter. To ensure a constant inclination, the back face is processed according to one of three options for laying the curves: using the Archimedean spiral method, through a logarithmic spiral, or along a circular arc emanating from a displaced center. In the last method, the widely used Interskol circular saw is sharpened.
To maintain normal sharpening conditions of those sections along the contour of the tooth blade that are in the plane of rotation of the blade or are located close to it, arrange the angle of the lateral clearance through the oblique side turning of the rear wall of the cutter (as with a conventional planing saw).