Heat Shrink Tubing (TUT) is a thin-walled polymer tube capable of reducing diameter when heated, while maintaining its protective properties. It is used to isolate conductive elements in all types of equipment, performs the functions of corrosion protection in difficult weather conditions and chemical attack, protects the surface from mechanical damage, and is also used for color marking. Reliability, ease of installation, minimal thickening of the insulated surface and a number of other advantages at a relatively low cost made many fans of the classic insulation tape switch to HERE.
Defining indicators HERE
Defining indicators are:
- the size of heat shrink tubes according to the size of the initial section;
- sitting ratio;
- coating thickness after shrinkage;
- the presence of an adhesive base;
- heat resistance;
- dielectric indicators;
- color gamut (for wire brand);
- physico-chemical characteristics of the material.
Materials used for the manufacture of tubular shrink insulators
Currently, a wide range of similar products is being produced from minimum to maximum size of heat shrink tubes, which differ in the properties of the material used. To produce HUT, fluororubber, polyolefins of various structures, polyvinyl chloride and other synthetic derivatives of polyethylene are used. During heating, the size of the heat shrink tube decreases, completely repeating the shape of the surface to be coated, maintaining the geometry during cooling, which ensures a high degree of insulation. Depending on the chemical composition and wall thickness of the material, the sitting temperature varies from +70 to 300 ° C.
Scope of application
The most popular are thin-walled tubes, due to the low price and ease of use. Most TUT prevent the combustion process, which determines the priority of their use at facilities with strict fire safety requirements. To isolate elements operating in conditions of high humidity, heat shrink tubes with an adhesive base applied to the inner surface are used. It is worth highlighting several types of specialized HERE:
- light-accumulating (fluorescent) used in low light conditions;
- high voltage, used in power lines with high voltage;
- with teflon coating, found application in metallurgy and automotive industry;
- tubes with a structural coating (corrugated) to cover the handles of tools.
There is a gradation in the thickness of the tube walls: thick, medium, and thin-walled. The first and second types are usually black in color, they are assigned to the general group with wall thickness during shrinkage in the range of 1.5 - 4.5 mm and a narrowing coefficient from two-fold (2: 1) to six-fold (6: 1). For HERE of this kind, as a rule, an internal adhesive layer is used. Tubes with a thin wall, up to 1 mm after shrinkage, are often made in color (for the possibility of marking contact pairs) or transparent (used for visual inspection of the quality of the connection).
The procedure for installing heat shrink tubes
The shrink process itself is very fleeting. HERE as if "melts" under the influence of a heating element, which can serve as an industrial hair dryer, heat gun or burner. In everyday life, for shrinkage often use ordinary matches or a lighter. With careful use, this, except for soot on the coating, does not harm anything, although using an open source of fire is highly not recommended. For high-quality coating, it is desirable to clean the protected surface, thoroughly degrease and put on the tube over the product to be coated. HERE with a medium and thick wall before this, you need to slightly warm up for greater elasticity. The length of the cut tube should be 5-10% more than the size of the insulated area.
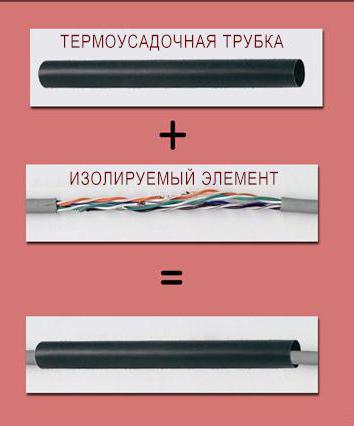
It is highly recommended not to use a coating consisting of several (overlapping) pieces, the HERE surface should not contain nicks and cuts. Direct heating should be carried out by uniform movements from the middle of the seated area to its edges, this is especially important when using HERE on an adhesive basis. Avoid local overheating of the insulator during shrinkage, this reduces the quality of the dielectric and mechanical properties of the material. After heating, the adhesive is baked to the insulated surface, providing excellent waterproofing.
Selection of the necessary HERE
Let us dwell in more detail on how to choose the size of the heat shrink tube, because for home use this particular parameter is crucial. It should be understood that, despite a large number of diameters, you can choose the right one only if you know the shrinkage coefficient. Now the answer to the question of how to choose the size of the shrink tube is obvious. The diameter of HERE before shrinkage must exceed the surface to be coated by at least 10%, and the indicator after heat treatment should be 15-20% less than the diameter of the workpiece. In practice, it should be guided by the condition 80 to 20, when the shrinkage size should be at least 20%, but not more than 80% of the declared compression ratios. If you select a tube that is too large, it will not sit down enough and fit snugly to the wire.
How to determine the size of the heat shrink tube?
There are several types of markings HERE. Sometimes the manufacturer indicates the initial size (diameter before heating) and the shrinkage coefficient, for example 3: 1, but most often products are marked with a larger and smaller diameter through an inclined line (10/5 or 10 mm / 5 mm). Additionally, the color and length of the cut may be indicated. For Russian and Chinese suppliers, the size is indicated in millimeters, and for European and American manufacturers inches are more often used. By the way, this may serve as an indirect sign of the country of origin of HERE.
The higher the compression ratio after heating, the better and therefore more expensive the product. In addition, a thicker wall of the tube will improve the insulating properties and extend its service life. The table below shows the most common size range of heat shrink tubes.
Marking | Initial size mm | Shrink size mm | Diameter of the part to be coated |
Int. diameter | Wall thickness | Int. diameter | Wall thickness | min. mm | max mm |
12 / 6mm | 11.5 | 0.55 | 6.5 | 1 | 7 | 10.5 |
15 / 6mm | 14.5 | 0.7 | 6.5 | 1,5 | 7 | 13.5 |
16 / 8mm | 15,5 | 0.55 | 8.5 | 1 | 9 | 14 |
20 / 8mm | 19.5 | 0.7 | 8.5 | 1,5 | 9 | 18 |
20 / 8mm | 19.5 | 0.95 | 8.5 | 2 | 9 | 18 |
20 / 10mm | 19.5 | 0.75 | 10.5 | 1,5 | eleven | 18 |
20 / 10mm | 19.5 | 1 | 10.5 | 2 | eleven | 18 |
28 / 11mm | 27.5 | 0.7 | 11.5 | 1,5 | 12 | 26 |
28 / 11mm | 27.5 | 0.95 | 11.5 | 2 | 12 | 26 |
33 / 14mm | 32,5 | 0.7 | 14.5 | 1,5 | fifteen | thirty |
33 / 14mm | 32,5 | 0.95 | 14.5 | 2 | fifteen | thirty |
30 / 15mm | 29.5 | 0.75 | 15,5 | 1,5 | 16 | 27 |
30 / 15mm | 29.5 | 1 | 15,5 | 2 | 16 | 27 |
40 / 20mm | 39 | 0.75 | 21.0 | 1,5 | 21 | 37 |
40 / 20mm | 39 | 1 | 21.0 | 2 | 21 | 37 |
50 / 25mm | 49 | 0.75 | 26.0 | 1,5 | 26 | 45 |
50 / 25mm | 49 | 1 | 26.0 | 2 | 26 | 45 |
60 / 30mm | 59 | 0.75 | 31,0 | 1,5 | 31 | 54 |
60 / 30mm | 59 | 1 | 31,0 | 2 | 31 | 54 |
80 / 40mm | 79 | 0.75 | 41.0 | 1,5 | 42 | 72 |
80 / 40mm | 79 | 1 | 41.0 | 2 | 42 | 72 |
Types of shipment and storage HERE
For industrial use, heat shrink tubes are supplied in coils from 10 to 200 m, but packing 50-100 m is most common. In retail, TUT are sold most often as a set, in the form of cuts of different colors and cross-sections, with a longitudinal length of the heat shrink tube 1 m or 1.22 m (4 ft), with adhesive-based tubes never being delivered in bays.
Heat shrink tubes are a progressive and effective insulation method that guarantees excellent results in the most difficult conditions.