Professional operations on the processing of metal and especially wooden billets are becoming closer to the amateur level of their technical performance as technology develops. The design of the working tool is becoming more ergonomic and safe to use, and the tendency to downsize opens up new opportunities for the organization of production processes. A specialized segment of a semi-professional tool for making furniture at home has also been formed, which takes into account the specifics of processing materials with the hands of a layman.
Basic list of woodworking tools
The presence of elementary carpentry tools is a basic condition for organizing furniture production at home. Even a one-time execution of such operations will require the use of impact and cutting devices. Specifically, the main set of tools for making furniture can include:
- Hacksaw. Processing lumber without this tool is not possible. Another thing is that in the conditions of continuous production it is more expedient to have a machine circular saw for such purposes.
- Plane. Also a common carpentry tool, through which you can perform planing operations with different parameters of the removed layer.
- Chisel. In a sense, a kind of planer, but in a simplified form. The user is dealing with a handle and blade, which also removes the top layer of wood from the workpiece.
- Ax. As a rule, tools for the manufacture of furniture are focused on the accuracy of the operations performed, allowing you to adjust the shape of the future product in detail. The ax is an exception, as it performs rough processing of the workpiece. For example, within the framework of the considered workflow, this tool may be required for cutting logs from which it is planned to form a table leg. Depending on the size of the ax, they can create grooves, remove the bark, trim the workpieces, etc.
- Jigsaw. It can be manual or electric, but the nature of the tasks to be solved is the same - to perform extremely accurate and accurate cuts with minimal damage to the edges. The best option for cutting chipboards of different thicknesses.
- Mounting tool. Direct means to perform assembly procedures - a hammer, wrenches, screwdrivers, etc.
Screwdrivers and drills as the basis for assembly operations
In choosing a tool for furniture production, much will depend on the technological stage of the manufacture of the item, its complexity and possible compatibility with other operations. But regardless of the completeness of the production cycle, assembly work will be required, in which the operations of drilling and twisting hardware are used. Accordingly, a screwdriver and a drill will become the basic tools for making home furniture. How to approach the choice of these devices? To begin with, again, the organizational capabilities for equipping the workshop and the operating modes in which the assembly will be carried out are determined. The following issues are resolved:
- Multifunctional or specialized models. Today, devices with the combined functions of a drill and a screwdriver are in fashion. Changing equipment, you can connect one or another mode of operation - including with shock function. But to perform accurate and serial operations, professional carpenters recommend using specialized models without combined functional support.
- Supply system. Again, it makes no sense to follow the fashion trend, choosing battery versions. They are good at working at remote sites without a stable source of energy supply, but more likely furniture production will be organized in a room with access to the network. We can talk about the disadvantages of working with a connected cord, but this drawback is more than covered by the light weight (due to the lack of a power supply) and, by default, the higher power of mains power tools.
- Tape models. A special and relatively new variety of screwdrivers that are used in factories and in private workshops. In fact, this is an automatic screwdriver, in the equipment of which a store with fasteners of a certain format is provided. In the flow mount mode, the operator will not need to be distracted by the installation of the consumable - the system will automatically install it without losing the pace of serial work.
- Additional options and features. For the manufacture of furniture with their own hands, the tool is selected with an emphasis on ergonomics and safety. In this regard, the presence of a reverse stroke, a soft start system, a pipe for connecting a construction vacuum cleaner and electronic torque control will become a desirable set of optional software.
Grinders
Without polishing and grinding operations when finalizing the internal and external surfaces of the lumber, you will also not be able to do. Moreover, the nature of such work differs - in some versions the grinders also perform cutting operations and adjust the texture for certain roughness parameters. The most common varieties of grinding tools for making furniture include the following:
- Angle grinder (angle grinder). One of the most common tools that is used in the domestic field and is also called a grinder. Although angle grinder is mainly intended for rough work with stone and metal, in certain modes with suitable abrasive wheels it can also be used in cleaning wooden surfaces.
- Direct grinder. The device with an elongated body and a collet snap snap in the form of an abrasive head in different sizes. This model can be used for spot grinding and polishing furniture surfaces in corners and other hard-to-reach areas.
- Belt Sander. Unlike the previous model, the design of the tape apparatus has a symmetrical design with a wide working platform, driven by rollers from two ends. An abrasive tape is mounted on them, which in the process of work removes the upper layer of the workpiece. In addition to polishing and grinding, in this way you can remove old paint and other unnecessary coatings.
- Models for polishing. Externally and structurally, such machines resemble angle grinders, however, with smaller dimensions and low power. This furniture making tool is valuable for its disc head made of fur, foam or felt. Also, with the help of abrasive wheels made of felt and wool, mechanical finishing of furniture surfaces is provided.

Furniture Measuring Instrument
In this case, it is not so much about traditional devices and devices for marking. The presence of a pencil with a marker and a tape measure with a ruler is required, but this does not end with a set of measuring tools. In recent years, not only in professional industries, but also in home workshops, the basic list of the necessary tools for making furniture includes electronic levels, angle meters, inclinometers and rangefinders. Of course, not in each case all these means of controlling the dimensional and spatial parameters will be involved, but the full cycle of furniture manufacturing involves their use.
For practical craftsmen who still do not plan to organize a full-length production line, it is worthwhile to limit themselves to the acquisition of a multifunctional laser level goniometer. The value of this tool lies not only in the ability to control the geometric parameters of the assembled product, but also in facilitating the installation procedure.
Particular attention should be paid to the requirements for tools for the manufacture of upholstered furniture, since this technological process will require the organization of a cutting and sewing zone. In this part of the work, you will also need a meter with scissors and sewing accessories with associated accessories. And this is not to mention the need for a sewing machine and other elements of textile production.
Massive furniture manufacturing equipment
Tables and chairs are made from solid wood, but more serious equipment such as milling machines and trimming machines are needed for such work.
For thicknessing and jointing in large factory halls, two different processing tools are used, but for the organization of a small workshop, the combined thicknessing and jointing unit is optimal. When choosing a machine, it will be important to calculate the planing width in advance - for example, up to 400 mm.
Gently remove defects from the array will help cross cutting. What tools for making furniture will cope with this task? It is advisable to focus on the trimming machine. Consider in advance the processing configuration and the approximate dimensions of the part to which the equipment will be applied. For example, table miter saws cut workpieces across, but with the possibility of changing the angle of cut to 45 degrees. Such models are used for final processing, the accuracy of which is ensured by the clamps of the workpiece, the guides and the scale for measuring the position of the saw blade.
Working with a single piece involves not only laborious cutting operations. It may well require delicate cutting to give the surface a certain texture. In other words, elements of decorative refinement are being implemented as part of the general process of making wooden furniture. The tool for such works is mainly associated with manual carpentry and carpentry processing tools, but for solid wood with a large amount of removal of excess mass, this method will not work. A version of a lathe with a rotating thrust and lead four-prong center will help to delicate turning or cutting. It is for home use that you should prefer a desktop type model, but with the ability to fine-tune the torque and angles of mechanical impact.
Tool for the manufacture of cabinet furniture
As prefabricated elements for hull structures, MDF and chipboard are usually used, that is, an emphasis on processing operations will be required in relation to pressed wood lamellas of varying degrees of rigidity. As already mentioned, jigsaws (especially electric ones) and some models of detachable manual machines allow you to cope with the accurate cutting of workpieces that are difficult to process. But if you need a tool for the manufacture of furniture from chipboard or other similar material in large volumes, then it is better to turn to small-sized machines. Today, there are many variations of format-cutting machines of low power (about 2-4 kW), which can be installed on a workbench in a garage. The main attention in the choice is given to the parameters of the saw unit - the thickness of the cut and the possibilities of tilting the disc. The rest will depend on individual workflow requirements.
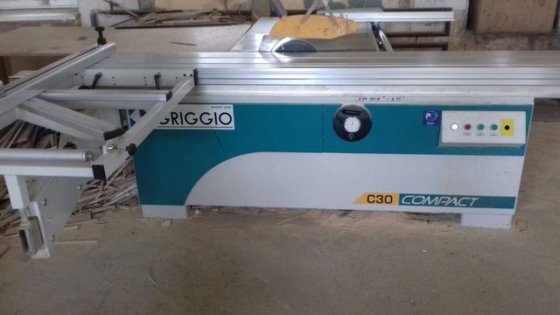
Also, do not forget about the possibilities of a curved cut. If solid homogeneous boards can be corrected with a hand tool after an unsuccessful figured cut with a hacksaw or saw, then chipping in a chipboard can ruin the workpiece. What tool is needed for the manufacture of furniture with elements of curvilinear cutting? Such a saw cut is realized qualitatively by band saw installations, which are desirable to select for the dimensions of the target part. It is important not to forget that the standard maximum for the same chipboard in thickness is 36 mm, so with an average cut depth of 80 cm, you can work with any workpiece. The problem is only in the limitations of the batch cut practiced today, when several parts are cut into one pass at the same time. What is more important, these are the characteristics of the saw blade (tape). Especially for chipboard processing, it is recommended to use equipment with a width of up to 26 mm, since an increase in this parameter will provoke the formation of chips.
Tool for processing edges in the manufacture of furniture
One can’t do without careful processing of furniture elements around the edges if it is planned to achieve the quality of the factory level. What tools for making furniture are used in this case? The edge banding machine is optimal, with which you can easily glue the surfaces with veneer, melamine, polyvinyl chloride and other decorative accessories. Some models of such equipment also perform the processing of the basis of the material, if its current condition is not suitable for further design.
In the manufacture of hull structures, the tasks of preparing holes for dowels and other fasteners and hardware are often encountered. They can be performed with a hand tool, but to ensure high geometric quality it is better to use a small drilling and filler installation, provided with guides and fixing units. The holes can be made in different formats and at different angles, which will not allow you to perform any electric drill with the same degree of accuracy when working with your own hands. Tools for the manufacture of furniture with large sections and facades require the preparation of appropriate equipment for fastening. Machines with two and three drilling groups will provide high accuracy when forming holes for loops in different configurations and in automatic mode.
Tools for making doll furniture
A completely special area of application of wood material, in which, according to requirements, the priority is not productivity and power, but extremely high accuracy and accuracy. You will have to deal with workpieces of miniature sizes, so initially you should focus on hand tools. Only with the general preparation of parts can the elements of machine processing be used, but the operations of correction and formatting will require a special carpentry set with carvers. Such a tool is used by master architects of art, performing original artwork on wood.
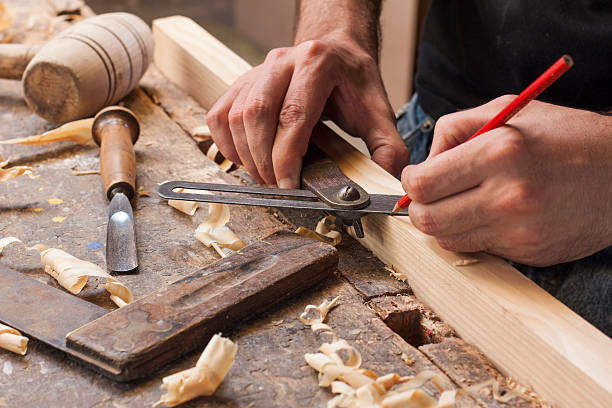
In doll furniture, tasks are not so laborious, but painstaking and also require a large proportion of concentration and attention. What tools are needed to make this type of furniture? It is not always necessary to work with small parts, so it will not be superfluous to prepare a jigsaw. It will allow you to perform the basics not only for furniture elements, but also for houses. It is also worth considering in advance the means of polishing parts and consumables for installation. If full-sized furniture is assembled mainly through hardware, then puppet furniture is assembled with glue. And so that the assembled structure dries faster at the junction points and acquires a sufficient degree of strength, a building hair dryer is used, the hot flows of which accelerate the binder polymerization process.
Auxiliary tools
In any production process, regardless of scale, the level of technological organization will affect the quality of work. This applies to additional devices and auxiliary devices that provide technical infrastructure for performing functional tasks. To understand the need for such an inventory, we should again recall what tools are needed for the manufacture of furniture. These are whole sets of devices for carpentry, marking devices, machine tools, etc. And if the representatives of the latter group are by and large self-sufficient in terms of organizing the work process, then a reliable base - a workbench - is necessary for the use of screwdrivers, jigsaws, hacksaws and screwdrivers. By the way, small-sized bench-type machines also need a stable and stable platform for installation. Another thing is that the fastening equipment and some marking elements along the cutting lines are included in their own design. In addition to the workbench, it will not be out of place to take care of a vise, clamps for clamping, tensioners for tying mating parts, etc. In some cases, thread-cutting equipment is used.It is used as a machine tool in the formation of non-standard threads - internal or external. As such a tool, taps and dies of the required format are used.
Conclusion
. , . , , . , , . , . . , . . , – . ( , ) . .