The quality and reliability of the finished brickwork depends directly on which mortar you choose and how you realize the thickness of the joint in the brickwork - longitudinal and vertical. This value must be laid at the very beginning, carefully monitor each row and check by measuring the height of the plot every 5-6 levels.
If you deviate from the recommended parameters, you will have a significant cost overrun, fragile connections between the blocks will appear, which will affect the rapid destruction of the building in the future. The decrease in strength is due to the fact that there is an additional compression load, as well as bending. Moreover, there is an uneven removal of moisture from the connecting mixtures, which is not allowed. So, the thickness of the seam in masonry is a very important parameter.
What are the standard requirements?
On average, the recommended value of the thickness of the seam of brickwork according to SNiP is 10 mm. More accurate parameters can be selected based on the type of bricks that you use, as well as on the type of structures. With significant deviations to the smaller side, the workers will not be able to compensate for possible irregularities in the ceramic products used, and the estimated number of blocks may not be enough. If the thickness of the seam in the brickwork is greater than the recommended parameters, then as a result the construction will be less durable than necessary.
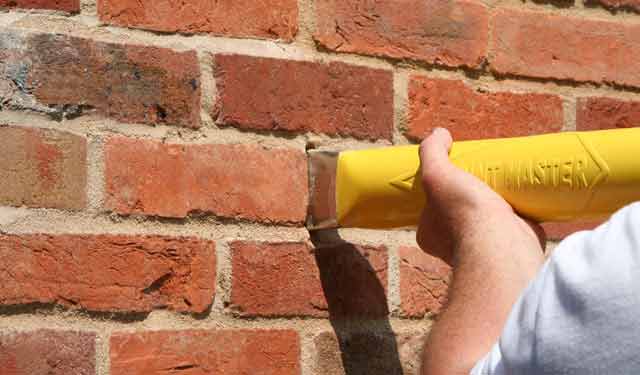
The parameters specified in the standard are considered relevant if you use ordinary components to build a supporting system. In masonry, the thickness of the horizontal joint should be approximately 12 mm, and the vertical - 10 mm. The permissible limit for the longitudinal rows will be from 10 to 15 mm, and the transverse seams vary from 8 to 12 mm. Deviation from the declared project parameters is not allowed. It is very important to carefully monitor and verify the quality at all stages of work.
What affects the thickness and uniformity of the seam?
Employee training. Due to the increased requirements regarding the reliability of the design of a small piece unit, work should be trusted only by qualified narrow-profile specialists. Itβs best to hire experienced crews.
The stiffness of the solution and the selected method of preparation. If you place the elements tightly, then you need to use a thick high-percentage mixture based on cement and sand. The maximum allowable thickness of the seam of the brickwork in this case will be 12 mm. If you use more liquid and plastic compositions, then lay the product as close as possible. The distance between adjacent elements should not exceed 8-10 mm.
The climate is very influential
Climatic conditions, as well as the further operation of the building is of particular importance. If you perform work in the winter and use solutions with special antifrosty additives or with heating, then the seams between the bricks should be minimized. The same can be said about the walls that are being built in the northern latitudes. This helps reduce the effects of low temperature. After all, the masonry will be monolithic.
Shape and size accuracy
Compared with aerated concrete blocks, which are placed on a layer of building glue of 2-3 cm, brick is much more difficult to lay, because you constantly need to adjust the deviation from standard values. If you use cheap and unequal elements, the masons will have to adjust the thickness of the mortar in the brickwork in separate rows by several millimeters in order to fit the entire wall to the project plan.
This factor is crucial. Careful adjustment of a product that has an irregular shape or size can only be done by a professional team. In case of large deviations, the strength of the structures as a result will be reduced to 25%.
Reinforcement is unlikely to help in such a situation. In order to reduce risks, the material must be carefully checked even when purchased. In addition to the thickness of the mortar, the reliability of masonry is greatly affected by the strength grade of bricks, the proportion of voids and resistance to severe frosts. The effect of the thickness of the joints in the brickwork is very high. This parameter must be considered together with geometric accuracy.
Tolerances
The specified rule is relevant for various small-sized components, as well as for facing and silicate. A slight increase in the thickness of the masonry seam of masonry is considered acceptable if you work with double varieties, however, in general, during the construction of load-bearing structures and face masonry, the interlayer must be maintained within 10 mm for the vertical seam and 12 mm for the longitudinal one.
An exception can be called a furnace for high temperature furnaces and similar designs of refractories. In such cases, it is necessary to settle a 5 mm special solution.
A separate group is a tile with a rectangular shape. It is necessary to mount it, observing the recommended standards of embroidery, which in turn depends on the texture and type of cut of the products, as well as requirements regarding protection against moisture.
Recommendations for laying various types of bricks
Bearing walls and a basement on the site, which is often exposed to moisture, need to be erected from solid ceramic bricks. Most often they are single type. An effective scheme in this case will be two-row. After all, it makes it possible to evenly distribute the weight load. The final thickness will be 25 cm. Products are best installed after a thorough check of evenness, as well as after waterproofing the base. It is advisable to inspect them for damage in order to eliminate errors. The first row must be placed without using the solution in dry form, and all non-format blocks must be removed.
The thickness of the vertical joint in the masonry of the lower layer can be 20 mm, however, all further layers must be laid, taking into account the design data. A small amount of the composition must be applied to the bumpy side of the brick, after which it is slightly pressed to the previously installed blocks.
The excess mixture in the longitudinal direction must be removed with a trowel. Perform smooth movements from the bottom up. When making horizontal rows, be careful, because there is a risk of smearing the mixture along the surface. This is especially important if you are working with face bricks. Get a uniform thickness without a large overspending will help you a special template. If you do not have experience, then you need to use the template not only in the longitudinal, but also in the transverse directions.
It all starts in the corner
The construction of any structure must begin from the corner with further consolidation of the order. This is a special bar to control the level. Walls that need to be plastered or insulated, need to be erected with a setting. You will sink the solution 15 mm deep into the face of your masonry.
After you check the level and, if necessary, make a careful adjustment, the elements can no longer be moved until the start of setting. After making several rows, we recommend taking a short break.
The quality of thermal insulation is a decisive factor.
A multi-row heat-insulating system must be removed using porous ceramics, which has a sufficiently high grade of strength. General standards for the thickness of the seam in masonry and its difference do not change. However, due to the fact that there are voids, prepare for the fact that it will be necessary to increase the flow rate of the solution.
The change will also affect its composition in order to exclude bridges of cold, to the standard mixture that mixes in proportions of 1 to 3, it is necessary to add components that reduce thermal conductivity. It can be expanded clay crumb, foamglass and their other analogues. The scheme for multi-row structures is greatly complicated, so if you doubt your abilities, it is best to hire a team of specialists.
Pressed and silicate ceramic bricks must be laid by analogy with others - from the corner. Closely monitor the level and ensure that each row is exposed dry. Due to the increased requirements regarding decorativeness, the type of seam will also change: it will be concave or convex. Grouting must be done immediately. The second type is most often chosen during facade cladding. After all, such a joint helps to strengthen the protection of the walls from moisture.
Keep an eye on the front tiles
The nuance is the laying of small holes for ventilation in vertical joints. As a rule, this is done on every fourth row. During operation, the front surface must be protected from contact with the solution. If drops nevertheless accidentally fall, then remove them with a dry rag before they catch.
The requirements for masonry and grout mixtures may vary depending on their water saturation. Standard ceramic mixtures must be moistened before installation, clinker ones are laid dry, but only on a special composition, which contains a minimum amount of salt-drawing substances.