In the construction of residential buildings and buildings for other purposes, it is customary to use various materials today, including blocks made of gas, foam, expanded clay concrete and gas silicate. Before using one of the listed materials, it is recommended that you familiarize yourself with the technology of masonry walls.
Work on the laying of expanded clay concrete products
Each master, before starting manipulations before laying the walls, must know how the formation of angles is made, the alignment of products, as well as what the technology is. To begin with, you should shut the solution, and also bring it to the point of work. Most often, the ratio of cement to sand is 1 to 4. For this material, however, everything will depend on what type of masonry cement you plan to use.
Methodology
Masonry walls made of expanded clay blocks with their own hands involves the formation of seams, the width of which should be equal to about 1 centimeter. When installing the first row, you need to carefully monitor the alignment of the products vertically and horizontally, in the future this will allow you to get an even installation. All horizontal and vertical seams must be necessarily coated with a solution so that there are no gaps.
Window hole
Laying near the window opening should be done strictly horizontally and as accurately as possible, this is especially important for an aesthetic look. At the same time, using only the building level to check the correct location of the products will not be enough. It is necessary to prepare a plumb line, which is a home-made device made of thread and a heavy object. This will determine how vertically the product was displayed.
Expert Advice
Under the condition that the laying of the walls of the blocks is done independently, then after the first row is ready, you need to pull a regular cord, which will act as a level for laying the rest of the blocks. The rope should have a good tension, while sagging in the middle should be excluded.
Masonry should start from the corners. Only after this, the master can begin to form walls. It is important to observe the dressing of products with the previous row. The minimum distance between vertically oriented seams in the vicinity of the rows located can be equal to the limit of 10 to 20 centimeters.
Block wall reinforcement
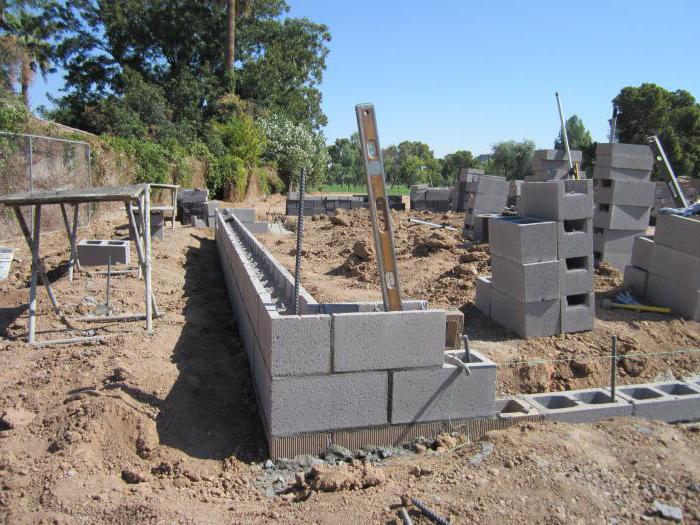
The masonry of the walls of the blocks should involve reinforcement, while reinforcement is used. To do this, stock up on masonry mesh or reinforcement, the diameter of which is from 6 to 10 millimeters. Stack these items every four rows. Some experts recommend the use of fiberglass reinforcement, which allows saving on delivery. Among other things, this material reduces heat loss in the walls. Specialists advise laying internal and external walls at the same time, like partitions, providing bandaging of corners and reinforcement. If this cannot be done for a number of reasons, then for dressing it is necessary to make a strob by releasing a reinforcing mesh in those places where it is then planned to lay the inner wall. On the top of the wall, which is laid out of expanded clay concrete blocks, it is necessary to provide an armored belt of reinforced concrete. It is important to consider that it will have a higher thermal conductivity compared to expanded clay concrete hollow blocks. Therefore, the master should provide a place for insulation of this part of the wall.
Tips for laying expanded clay blocks
If you will be laying walls from blocks, then you do not need to make too thin seams in the case when the size of the products is not maintained. At the same time, the thickness of the seam can reach 10 millimeters, while a thin seam can adversely affect the unevenness of the wall. If you perform the work without assistance, then before laying each next row, it is advisable to lay out the blocks on the previous row so that they do not interfere with applying the solution to the surface. This will significantly speed up the process. Masonry walls from blocks should not imply too strong impacts on products to align their position. If we are talking about hollow products, then you can easily damage them, because they are fragile. When carrying out wall laying work, halves of blocks, perhaps a quarter, will be required. If you do not have experience breaking products, it is best to prepare an angle grinder for cutting.
Silicate masonry

Gas silicate blocks are versatile, with their help you can build internal, external walls, as well as partitions and load-bearing walls. Installation work is prohibited in rainy weather, as the cellular structure of the products will accumulate moisture, and the temperature difference will lead to damage to the masonry. To prepare the solution, it will be necessary to prepare a plastic bucket, a special nozzle on the drill, as well as a manual electric drill. To apply the solution, you will need a trowel, it is desirable that there are several, each of which should have a different width. Laying walls of gas silicate blocks provides for their alignment with other products, for this it is customary to use a building level, a rubber mallet, the last of which can be replaced with a wooden one. To process the blocks, you will need a planer, a tool for making grooves, a soft brush, a saw, a marking square, and drills. In the process of laying, you need a dry adhesive mixture, as well as a cement-sand mortar.
Installation instructions for gas silicate blocks
If you will be laying walls of gas silicate blocks, then before starting work it is necessary to waterproof the surface. To do this, at the place of future location of the first row, you need to lay a layer of roofing material, which is fixed on a cement-sand mixture. The solution layer should be laid on top of the roofing material. The first row of blocks will be located on it. In such a mixture, the ratio of cement and sand should be 1 to 3. This solution can also be used for further masonry, however, the thickness of the seam should not be more than 20 millimeters. The surface of the unit is wetted for better grip if the weather is dry enough. Specialists advise using special adhesives, since if you increase the thickness of the seam, this can cause additional heat loss.
Technology of work
The technique for laying blocks is the same as described above. After the corner products are in place, they must be carefully aligned, and then you can continue to work in accordance with the previously set guides. For external walls, the guides must be installed in advance along the perimeter of the walls, by installing pegs at a distance of 2 meters from each other. A rope is pulled between them. If we are talking about an internal partition, then the construction is carried out from one of the products of the side walls. In this case, it will be necessary to carry out early marking on the surface of the floor and walls with a tape measure and level, refusing to lay waterproofing. After the side block is installed, special glue will need to be applied to the side faces of the products. Roughnesses on a horizontal surface can be eliminated with a grater, and the remaining debris, such as fragments of blocks or dust, must be removed with a soft brush.
Silicate glue preparation
If you use glue with a good level of adhesion, then you can provide a minimum thickness of the seam, which should not be more than 3 millimeters. This can be called an undoubted advantage of this material, since you can improve the thermal insulation characteristics of the finished walls. Among other things, gas silicate glue has a sufficiently high strength, which allows it to be used in other work, for example, when laying foam or aerated concrete, as well as when decorating external and internal walls with tiles. If you will be laying the walls of the blocks with your own hands, then the adhesive composition can be prepared by pouring water into a clean plastic bucket. After this, a dry mixture is added, the composition is well mixed using an electric drill with a nozzle. Mixing should be carried out at low speeds until then, until you can achieve complete uniformity of composition. It is important to correctly observe the ratio of liquid to dry mixture, which should be indicated in the instructions for the product. For different manufacturers, this figure may vary. In order to avoid freezing of the composition in the bucket during the work, it is recommended to prepare a small portion. As soon as you start laying the walls, you can understand how much finished composition you can work out before it hardens. Everything will depend on the speed of the work.
Stacking subsequent rows
In general, the technology of laying walls from blocks of different materials does not differ from each other. Once you finish laying the first row, you can proceed to the second. The adhesive should be applied to a horizontal surface with a trowel. After that, the first block is stacked. The solution is then applied to the side surface of the first product and to the zonal base. The second row should begin to be laid from the corner. However, if in the first row the first corner product started the row with its long side to the right, then in the second row the first block should go the long side to the left. This will give the whole structure strength. The order and technology of laying gas silicate blocks are the same as when working with ordinary brick. However, carrying out these works is much easier due to the low weight and size of the products.
Foam block laying technology
If you will be laying walls from foam concrete blocks, the first row should be laid on a cement-sand mortar, which is applied in a layer of 3 centimeters on a waterproofing surface. Laying the next row should be done no earlier than 3 hours after the completion of work on the first row. In this case, you can use both cement mortar and a special composition. The thickness of the future seam should not be more than 5 millimeters. Walling of concrete blocks is carried out according to the same method. For laying window openings, hollow foam blocks that have a U-shape should be used. They should lay the connected reinforcement, and then pour concrete. The rods are laid in special channels that are cut in blocks. If there are none, then you can use a grinder or wall chaser for this. Before laying the floor slabs, it is necessary to equip a concrete armo-belt, the height of which should be 20 centimeters.
Walling of ceramic blocks is also carried out by a similar technique. You must remember that cement mortar should be prepared in small batches. If you use special glue, then it will be necessary to develop it within 15 minutes after cooking. The optimum temperature for laying foam blocks is a range from +5 to +25 degrees. If the weather is hot outside, it is recommended to moisten the surface of the foam blocks periodically. Wall masonry from aerated concrete blocks must also be carried out using the building level and plumb. This is the only way you can ensure evenness of the walls. Cement or glue is best applied with a special comb, this will make the seams more even and thin. Excess mortar can be disposed of with a conventional construction spatula.
Conclusion
The technology of masonry walls made of expanded clay concrete blocks is no different from the methods described above. In all cases, it is important to take care of exhibiting the products horizontally and vertically, this will ensure reliability and evenness of the future walls.