16K20F3 turning and screw-cutting equipment , the technical characteristics of which are discussed below, is based on the 16K20 aggregate and is used mainly in small-scale production. Both machines have a unified structural part and a general principle of operation. The installation allows you to process the external and internal surfaces of the workpieces, up to 1000 millimeters long. Numerical software provides additional capabilities and facilitates unit maintenance.
What does it consist of?
Specifications 16K20F3 due to the design and kinematic diagram of the machine. The unit is made in a traditional layout that meets universal standards, and also allows the production of a wide range of operations.
Hardware components:
- The skeleton (bed).
- Frame.
- Caliper carriage.
- Rotary tool holder.
- Rear and spindle headstock.
- Automatic transmission box.
- Guide elements.
- Electromagnetic couplings.
- Cross and longitudinal drives.
- Hydraulic booster.
Principle of operation
The machine 16K20F3, the technical characteristics of which allow you to select up to 9 shaft speeds, works as follows:
- The metal part is mounted in a spindle driven by a V-belt transmission from an electric motor.
- Processing speed is adjusted using an automatic gearbox and spindle assembly.
- The automatic transmission is equipped with six electromagnetic couplings, the combined inclusion of which allows you to select the desired speed.
- To increase or decrease revolutions, spindle head gears are used. They are controlled manually, adjust up to 12 positions.
- The carriage of the unit is adapted for longitudinal movement using an electromagnetic drive.
- The transverse shift of the caliper and tool holder is made through the drive, gear and spindle.
- The rotary tool holder can be mounted in six positions with a change in the machining angles and the horizontal axis of rotation of the plane. In addition, the support of the transverse caliper is involved in these manipulations.
- A tool head is positioned on the tool holder, designed to use no more than six cutters that process the workpiece according to a given program.
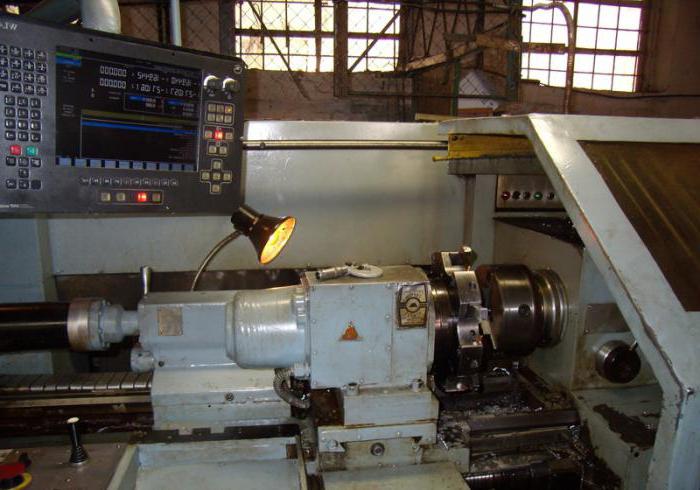
Hydraulic drive
This lathe assembly 16K20F3, the technical characteristics confirm this, provides all the basic processes associated with the functioning of working elements. The hydraulic drive consists of the following parts:
- Power steering couples.
- Regulating pump.
- Drive.
- Reservoir with oil.
- Control equipment.
Marking
The 16K20F3 turning unit, the technical characteristics of which will be discussed later, is marked. Its decoding is as follows:
- Index "1" - turning.
- 6 - screw cutting.
- K - production.
- 20 - a measure of height in the center in centimeters.
- F3 - CNC equipment.
Equipment of this category has a standard power in the range of 10-11 kW, the accuracy class corresponds to GOST 8-82-P.
CNC machines 16K20F3: technical specifications
Parameters of the equipment in question:
- Dimensions - 3.7 / 2.2 / 1.65 m.
- Weight - 400 kg.
- Number of speeds –22.
- The diameter of the hole is 53 mm.
- Pinoli Center - Morse 5.
- The operating range is from 12.5 to 2000 rpm, depending on the selected speed.
- The step size is 0.01-40 mm.
- Cutter height - 25 mm.
- Longitudinal / transverse strokes - 5000/7500 mm / min.
Description
The lathe 16K20FZ, the technical characteristics of which are indicated above, is equipped with a cast-iron bed undergoing grinding, which ensures a long period of operation. As the main drive, an 11 kW electric motor is used. It guarantees a torque of up to 800 Nm. This allows you to adjust the processing of the workpiece with maximum accuracy to the required dimensions.
The spindle of the unit has a hole with a diameter of 55 mm with the possibility of fixing the pin parts of various diameters. Special turrets are used for special operations, greatly expanding the capabilities of turning equipment. This unit is most susceptible to wear, since the planetary gearbox is deformed in the form of chipping teeth or destruction of the eccentric. Regular monitoring of the state of mechanisms and timely preventive maintenance will help to avoid such consequences. Lubrication of parts is carried out when the equipment is turned on, it is directed to various elements. Program control in automatic mode determines the cycle of supply of the lubricant mixture to the components of the equipment. You can start this operation manually. In this case, the programmed cycle is not violated.
Versatility
Technical characteristics of the 16K20F3 turning screw cutting machine allow it to be used for the following operations:
- Drilling holes of various diameters.
- Processing blanks from the end parts.
- Countersinks.
- Threaded thread.
- Bores and surface finishes of conical and shaped type.
Special limiters act as protection for screw-cutting pairs, which help prevent premature failure of mechanisms. The modernization of the units under consideration consists in equipping with CNC sets of domestic and foreign production with replaceable electrical equipment systems. Re-equipment makes it possible to increase power by 2-3 times, depending on the condition of the units. All these solutions increase the productivity of the equipment, reduce the mode of transformation of the workpieces. It is desirable to carry out modernization simultaneously with the overhaul.
What gives an improvement?
Screw-cutting lathe 16K20F3, the technical characteristics of which can be improved by modernization in three ways:
- By complete modernization.
- Improving components and working tools.
- Reorganization of traction equipment.
Modernization makes it possible to increase the number of parts processing ranges, as well as the accuracy of manipulations.
To maximize the working life of the equipment, an adaptive control system is used. It allows you to turn off the unit at critical loads, and also contributes to the following indicators:
- Reducing the finish of parts.
- Increase the service life of components.
- To reduce the incidence of equipment failure.
- Increase the overall performance of the equipment.
The technical characteristics of the 16K20F3 CNC lathe allow you to change the load on the spindle. In this case, it is possible to adjust the feed of the tool used, taking into account the type of material of the workpiece. This helps to increase the life of all parts of the unit.
CNC
When using numerical software , workpiece processing operations are performed using predefined programs. They make it possible to correct the information supplied from the operator console, as well as use external memory cassettes. The final data is displayed on a special display, after the analysis of which, you can decide to configure the subsequent process.
Automation of the process is accompanied by 6th, 8th or 12th positions, allowing you to change the diameter of the processing or the horizontal axis of rotation. The working head is equipped with a disk on which three axial and six radial elements can be mounted. In addition, it can be operated with 8-12 blocks for various tools.
To increase the efficiency of the 16K20F3 machine, the technical characteristics and description of which are given above, can be further modernized by changing the kinematic scheme or by installing a modern energy-saving design. Significantly expands the functionality of the unit under consideration CNC complex. Thanks to it, the accuracy and speed of processing of parts, as well as the finishing mode, are improved. CNC machines have a range of longitudinal and transverse movements - 0.005 and 0.01 millimeters, respectively.