Nowadays, the creation of a high-quality acoustic environment is no longer limited to concert halls and theaters. The appearance of shopping and entertainment centers, the office structure of the open space, and qualitatively new medical, educational and cinema complexes expanded the scope of sound-absorbing materials. To create a comfortable environment in the decoration of rooms, acoustic panels for walls and ceilings are increasingly being used. Their use allows to reduce the level of reflection, increase speech intelligibility, and normalize sound pressure.
Acoustic materials
The effect of the use of acoustic panels is achieved by using sound-absorbing materials in them. They can be both natural and artificial origin. Traditionally, materials based on wood, textile or gypsum were used in the decoration of halls. Currently, acoustic panels for walls are made of gypsum, wood, mineral wool, fiberglass, polyurethane foam and melamine.
Types of wall acoustic panels
Depending on the material used , sound-absorbing panels for walls can be divided into the following types:
- Wood fiber, cellulose. On a cement or gypsum binder, slabs of typical sizes that are multiples of 600 mm and a thickness of up to 25 mm are molded. Such panels can be painted in any desired color.
- Basalt cotton wool. Basalt wool slabs have high sound absorption and fire safety. May have a microrelief, structural or smooth surface.
- Drywall. Perforated sheet material is characterized by low reflectivity. May have a different pattern of perforation. The material is easily painted.
- Gypsum. Embossed slabs of this material, the so-called 3D panels, are environmentally friendly and non-combustible. Available in various formats, thicknesses and patterns. The panels are installed on a "wet" technology, without the use of frame systems and guides. They can be painted in any color.
- Fiberglass. In the manufacture of acoustic panels using high density material coated with fiberglass or dyed. Piece parts are mounted on walls using special profiles. The size of the plates is determined by the manufacturer, for example, acoustic panels for the walls of "Ekofon" have a size of 2700 x 1200 mm, 40 mm thick.
- Polyurethane foam. Plates of this foam material are easily mounted with glue directly on the surface of the walls. The thickness of the material used is from 20 to 100 mm with dimensions of 1000 x 1000 mm. Graphite color with a different relief pattern is standardly produced.
- Melamine. Sound-absorbing panels for walls from this synthetic material are produced in sizes that are multiples of 600 mm, with a thickness of 20 to 100 mm. The base color of the material is light gray, any color is allowed.
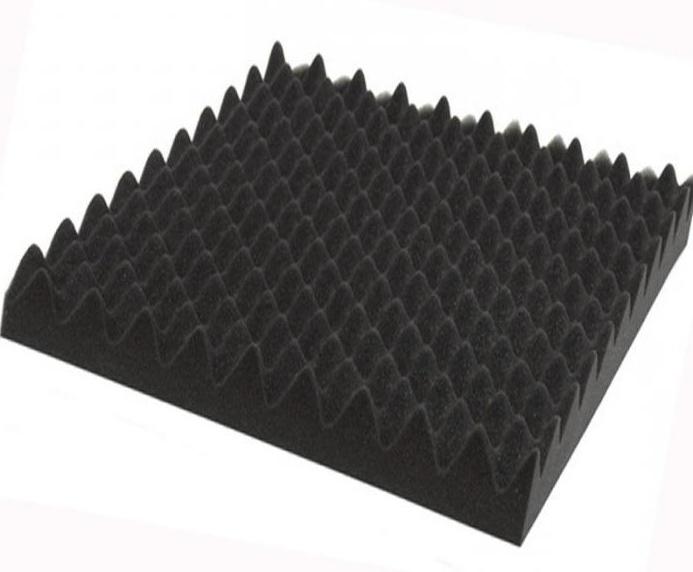
Main characteristics
- Sound absorption coefficient. It characterizes the ability of the panel to absorb sound waves. The value can have a value from 0 to 1. Zero corresponds to the total reflection of sound, 1 - to complete absorption. An open window with an area of ββ1 sq. m
- Light reflectance It is indicated as a percentage, 0% corresponds to total absorption of light, 100% to full reflection. On average, acoustic panels have a reflectance value of 60-80%. It is most important to consider this characteristic for ceiling tiles.
- Moisture resistance. This value indicates the resistance of the material to water. Given that acoustic materials have a porous structure, they are largely susceptible to moisture. This parameter is especially important for ceiling tiles.
- Thermal conductivity. It characterizes the ability of a material to conduct heat. Due to its porous structure, according to this indicator, acoustic panels for walls are a good heat insulator.
Ceiling Acoustic Panels
In modern interiors, ceiling decoration with sound-absorbing materials is increasingly common. Acoustic ceilings, as a rule, are mounted according to the frame scheme (for example, Armstrong slabs), which allows you to hide the laid communications behind them. In this case, frame systems can be open or hidden. The ceiling panels are additionally weighted to reduce the load on the structural members. Therefore, for the manufacture of ceiling acoustic plates, either natural fibrous materials or artificial fiberglass are used. The geometric dimensions of such elements, as a rule, are performed in multiples of 600 mm, for example, as the popular Armstrong plates, but can reach lengths up to 2400 mm. The thickness of the panels is from 12 to 40 mm. The surface of acoustic ceiling tiles can be both structural and rough. The panels are paintable, but are usually delivered in white.
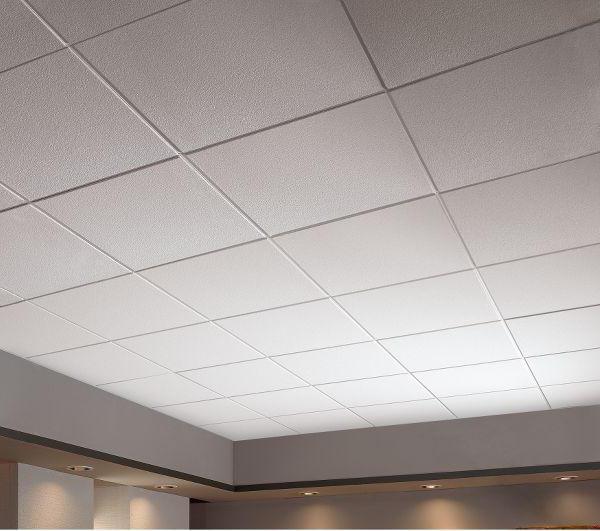
Most often, acoustic plates Armstrong, type Baikal, are used in interior decoration. Specifications are listed below:
- Sound absorption - 0.45.
- Moisture resistance - 90%.
- Light reflection - 85%.
- Thermal conductivity - 0.052 W / (m x deg).
- Geometric dimensions - 600 x 600 x 12 mm.
- Fire-fighting characteristics - G1, B1, D1, T1.
Acoustic selection
The determining parameter of choice is sound absorption. Its value is determined by acoustic calculation, and if it is difficult to perform, then choose a material with a maximum sound absorption value. When choosing acoustic panels for walls, especially exterior ones, it is advisable to use products with the lowest possible thermal conductivity. This will reduce heating costs.
For ceiling panels, it is important to pay attention to light reflection: the higher it is, the brighter it will be in the room and the lower the cost of electric lighting. Also, moisture resistance is significant for ceiling tiles, its low value can lead to sagging.
Fire fighting properties
Since soundproofing products are used in residential or public buildings, including in rooms with a large stay of people, it is important to consider the fire-fighting characteristics of the materials. The main ones are:
- Combustibility
- Flammability.
- Smoke generating ability.
- Toxicity.