The use of metals in everyday life began at the beginning of human development. Copper is their first representative. It is available in nature and beautifully processed. During archaeological excavations, household items and various products made from it are often found.
In the process of development, a person learned to combine different metals, producing alloys of greater strength. Tools were made of them, and later used to make weapons. Experiments continue in our time, alloys with specific strength of metals are created, suitable for the construction of modern structures.
Types of loads
The mechanical properties of metals and alloys include those that are able to resist the action of external forces or loads on them. They can be very diverse and in their effect distinguish between:
- static, which slowly increase from zero to a maximum, and then remain constant or slightly change;
- dynamic - arise as a result of an impact and act for a short period.
Types of deformation
Deformation is a modification of the configuration of a solid under the influence of the loads (external forces) applied to it. Deformations, after which the material returns to its previous shape and retains its original dimensions, are considered elastic, otherwise (the shape has changed, the material has lengthened) - plastic or residual. There are several types of deformation:
- Compression. The volume of the body decreases as a result of the action of compressive forces on it. The foundations of boilers and machines experience such deformation.
- Sprain The length of the body increases when forces are applied to its ends, the direction of which coincides with its axis. Cables, drive belts are stretched.
- Shift or cut. In this case, the forces are directed towards each other and under certain conditions a cut occurs. An example is rivets and tie bolts.
- Torsion. A pair of forces, oppositely directed, acts on a body fixed at one end (shafts of engines and machine tools).
- Bend. Change in body curvature when exposed to external forces. Such an action is typical for beams, boom cranes, railway rails.
Determination of metal strength
One of the main requirements that apply to the metal used for the production of metal structures and parts is strength. To determine it, a metal sample is taken and stretched on a testing machine. The standard becomes thinner, the cross-sectional area decreases with a simultaneous increase in its length. At a certain moment, the sample begins to stretch in only one place, forming a βneckβ. And after a while there is a gap in the area of ββthe thinnest place. Extremely viscous metals, brittle ones behave in this way: hard steel and cast iron stretch slightly and they do not form a neck.
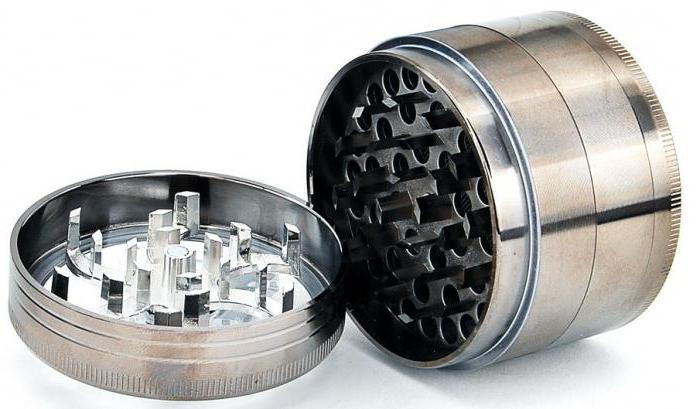
The load on the sample is determined by a special device, which is called a force meter, it is mounted in a testing machine. To calculate the main characteristics of the metal, called the tensile strength of the material, it is necessary to divide the maximum load withstood by the specimen before rupture by the value of the cross-sectional area before stretching. This value is necessary for the designer in order to determine the dimensions of the manufactured part, and the technologist to assign processing modes.
The strongest metals in the world
High-strength metals include the following:
Titanium is used in medicine, military industry, shipbuilding, and aviation.
- Uranus. The most famous and durable metal in the world, is a weak radioactive material. It is found in nature in its pure form and in compounds. It refers to heavy metals, flexible, malleable and relatively ductile. Widely used in manufacturing.
- Tungsten. The calculation of the strength of the metal shows that it is the most durable and refractory metal, not amenable to chemical attack. Well forged, it can be pulled into a thin thread. Used for filament.
- Rhenium. Refractory, has a high density and hardness. Very durable, not subject to temperature changes. Finds application in electronics and technology.
- Osmium. Hard metal, refractory, resistant to mechanical damage and aggressive environments. Used in medicine, used for rocket technology, electronic equipment.
- Iridium. In nature, it is rare in free form, more often in compounds with osmium. It is difficult to machine machining, has high resistance to chemicals and strength. Alloys with metal: titanium, chromium, tungsten, are used for the manufacture of jewelry.
- Beryllium. Highly toxic metal with a relative density, having a light gray color. It is used in ferrous metallurgy, nuclear energy, laser and aerospace engineering. It has high hardness and is used for alloying alloys.
- Chromium. Very hard metal with high strength, white-blue color, is resistant to alkalis and acids. The strength of metal and alloys allows them to be used for the manufacture of medical and chemical equipment, as well as for metal-cutting tools.
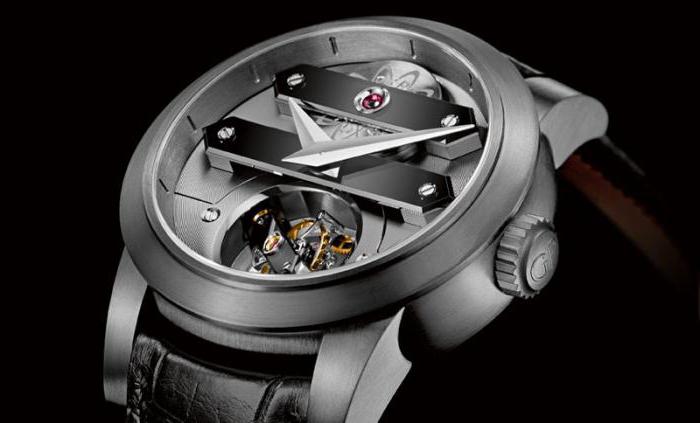
- Tantalum. The metal is silver in color, has high hardness, strength, has refractory and corrosion resistance, is ductile, and is easy to process. Finds application in the creation of nuclear reactors, in metallurgy and chemical industry.
- Ruthenium. Belongs to platinum group metals. It has high strength, hardness, refractoriness, chemical resistance. Contacts, electrodes, sharp tips are made from it.
How to determine the properties of metals?
To test the strength of metals, chemical, physical, and technological methods are used. Hardness determines how materials resist deformation. Resistant metal has greater strength and parts made from it wear out less. To determine the hardness, a ball, a diamond cone or a pyramid is pressed into the metal. The value of hardness is set by the diameter of the print or by the depth of indentation of the object. Stronger metal is less deformed, and the depth of the print will be less.
But tensile samples are tested on tensile testing machines with a smoothly growing load when stretched. The standard may have a circle or square in cross section. To test the metal to withstand loads of shock nature, impact tests are carried out. In the middle of a specially made sample, an incision is made and it is placed opposite the percussion device. Destruction should occur where there is a weak spot. When testing metals for strength, the structure of the material is examined by X-rays, ultrasound and using powerful microscopes, and also etching with chemicals is used.
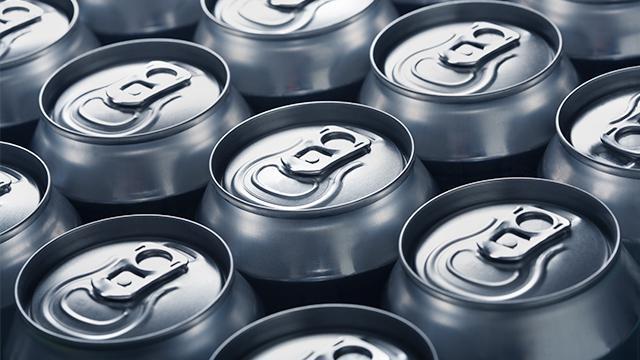
Technological include the simplest types of tests for fracture, ductility, forging, welding. The extrusion test makes it possible to determine whether the sheet material is cold stampable. Using a ball in the metal squeeze the hole until the first crack appears. The depth of the pit until fracture appears and will characterize the ductility of the material. Bending test makes it possible to determine the ability of the sheet material to take the desired shape. This test is used to evaluate weld quality. To assess the quality of the wire, a bend test is used. The pipes are tested for flattening and bending.
Mechanical properties of metals and alloys
The mechanical properties of metal materials include the following:
- Strength. It lies in the ability of a material to resist destruction by external forces. The type of strength depends on how external forces act. It is divided into: compression, tension, torsion, bending, creep, fatigue.
- Plastic. This is the ability of metals and their alloys to change shape under the influence of a load without being destroyed, and to preserve it after the end of the impact. The ductility of a metal material is determined by tension. The more elongation occurs, while reducing the cross section, the more ductile the metal. Materials with good ductility are perfectly processed by pressure: forging, pressing. Plasticity is characterized by two values: relative narrowing and elongation.
- Hardness. Such a quality of the metal lies in the ability to resist the penetration of a foreign body having a more significant hardness into it, and not to receive residual deformations. Wear resistance and strength are the main characteristics of metals and alloys that are closely related to hardness. Materials with such properties are used for the manufacture of tools used for metal processing: cutters, files, drills, taps. Often, the hardness of a material determines its wear resistance. Thus, hard steels wear less during operation than softer grades.
- Impact strength The peculiarity of alloys and metals to resist the influence of loads accompanied by shock. This is one of the important characteristics of the material from which parts experiencing an impact load are made during machine operation: wheel axles, crankshafts.
- Fatigue. This is the state of the metal, which is constantly exposed to loads. Fatigue of the metal material occurs gradually and may result in the destruction of the product. The ability of metals to resist fracture from fatigue is called endurance. This property depends on the nature of the alloy or metal, the state of the surface, the nature of the treatment, and working conditions.
Strength classes and their designations
The normative documents on the mechanical properties of fasteners introduced the concept of metal strength class and established a notation system. Each strength class is indicated by two numbers, between which a dot is placed. The first number means the tensile strength, reduced by 100 times. For example, a strength class of 5.6 means that the tensile strength will be 500. The second number is increased 10 times - this is the ratio of the yield strength to tensile strength , expressed as a percentage (500x0.6 = 300), that is, 30% is the minimum yield strength of tensile strength. All products used for fasteners are classified according to the purpose of use, shape, material used, strength class and coating. According to the purpose of use, they are:
- Shareshare. They are used for agricultural machinery.
- Furniture. They are used in construction and furniture production.
- Road. They fasten metalwork.
- Engineering. Applied in the engineering industry and instrumentation.
The mechanical properties of fasteners depend on the steel from which they are made and the quality of processing.
Specific strength
The specific strength of the material (formula below) is characterized by the ratio of tensile strength to metal density. This value shows the strength of the structure for a given mass. It is of the greatest importance for industries such as aircraft manufacturing, rocket science and spacecraft manufacturing.
In terms of specific strength, titanium alloys are the most durable of all used technical materials.
Titanium alloys double the specific strength of metals related to alloy steels. They are not susceptible to corrosion in air, in acidic and alkaline environments, are not afraid of sea water and have good heat resistance. At high temperatures, their strength is higher than that of alloys with magnesium and aluminum. Due to these properties, their use as a structural material is constantly increasing and is widely used in mechanical engineering. A disadvantage of titanium alloys is their low machinability. This is due to the physical and chemical properties of the material and the special structure of the alloys.
The table above shows the specific strength of metals.
Use of ductility and strength of metals
Very important properties of the metal are ductility and strength. These properties are directly dependent on each other. They do not allow the metal to change shape and prevent macroscopic destruction when exposed to external and internal forces.
Metals with high ductility are gradually destroyed under the influence of the load. At first, a bend appears in them and only then it begins to gradually collapse. Plastic metals easily change shape, so they are widely used for the manufacture of car bodies. The strength and ductility of metals depends on how the forces applied to it are directed and in which direction the rolling was carried out in the manufacture of the material. It was found that during rolling, the metal crystals are elongated in its direction more than in the transverse direction. In sheet steel, strength and ductility are significantly greater in the rolling direction. In the transverse direction, the strength decreases by 30%, and the ductility by 50%, these parameters are even lower in the sheet thickness. For example, the appearance of a break on a steel sheet during welding can be explained by the parallelism of the weld axis and the rolling direction. The plasticity and strength of the material establish the possibility of its use for the manufacture of various parts of machines, structures, tools, devices.
Standard and design resistance of metal
One of the main parameters that characterize the resistance of metals to the effects of force is the regulatory resistance. It is set according to design standards. The calculated resistance is obtained by dividing the normative by the appropriate reliability coefficient for this material. In some cases, the coefficient of working conditions of structures is also taken into account. In calculations of practical importance, the calculated metal resistance is mainly used.
Ways to increase the strength of metal
There are several ways to increase the strength of metals and alloys:
- The creation of alloys and metals having a defect-free structure. There are developments on the manufacture of whiskers (whiskers) several tens of times higher than the strength of ordinary metals.
- Obtaining volumetric and surface hardening by artificial means. During metal forming (forging, drawing, rolling, pressing) a volumetric hardening is formed, and knurling and bead-blasting gives a surface hardening.
- Creating an alloyed metal using elements from the periodic table.
- Purification of metal from impurities present in it. As a result of this, its mechanical properties are improved, crack propagation is significantly reduced.
- The elimination of surface roughness.
Interesting Facts
- Titanium alloys, the specific gravity of which exceeds aluminum by about 70%, is 4 times stronger than them, therefore, in terms of specific strength, alloys containing titanium are more profitable to use for aircraft construction.
- Many aluminum alloys exceed the specific strength of steels containing carbon. Aluminum alloys have high ductility, corrosion resistance, are perfectly processed by pressure and cutting.
- Plastics have higher specific strengths than metals. But due to insufficient rigidity, mechanical strength, aging, increased brittleness and low heat resistance, layered plastics, textolites and getinaks are limited in application, especially in large-sized structures.
- It has been established that in terms of endurance to corrosion and specific strength, ferrous and non-ferrous metals and many of their alloys are inferior to fiberglass.
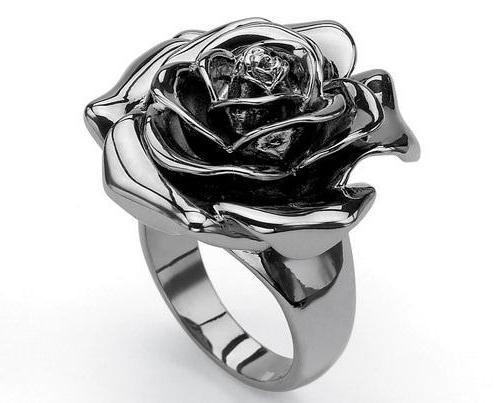
The mechanical properties of metals are the most important factor in their use in practical needs. When designing some kind of structure, part or machine and selecting material, they must consider all the mechanical properties that it possesses.