Perhaps now few people remember the times when in incubators for breeding poultry the required temperature was maintained by simply adjusting the size of the opening of ventilation gaps.
Although with constant monitoring this method was quite effective, it required continuous attention from the person. Therefore, when the first temperature controller for the incubator appeared, it was like a quiet revolution. It was possible not to worry that the temperature would "float", which freed from routine tasks.
Device purpose
The temperature controller for the incubator is based on the principle of feedback, in which one of the controlled values ββindirectly affects the other. When artificially breeding poultry, one of the most important tasks is to maintain the temperature within the established limits. Even slight deviations affect the percentage of hatched livestock.
The temperature regulator for the incubator just performs this function. It controls the operation of the
heating elements in such a way that the temperature is kept constant, regardless of changes in the heating of the surrounding air. Each poultry breeder must learn how to use a temperature controller for an incubator. The connection diagram is extremely simple: a load-source of heat (lamps, heating elements) is connected to the output wires of the device; for others, power is supplied; and a temperature sensor is connected to the third output, from which the device reads the temperature values ββ(usually placed at the level of egg laying).
Principle of operation
Consider how a thermostat for an incubator works . After the device is connected to the network, power is supplied to the heating element (say, an incandescent lamp) through its circuit. Since the lid of the house is closed, a gradual increase in temperature begins.
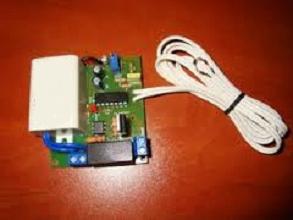
Its value is transferred to the device from a temperature sensor located in the incubator body. In the temperature controller itself, the possibility is realized in one way or another (depending on version) to set the heating limit. When the temperature reaches this threshold value, the device will temporarily turn off the lamps or reduce the intensity of their glow. After cooling down a few degrees (delta), the lamps will be powered again. The task of man is reduced only to setting the upper limit, and the rest will be done by automation. Thus, it does not matter what temperature outside the incubator: if it is low, then the lamps will heat the masonry more intensively, and if it is high, they will often turn off. The result is the same: the temperature inside the incubator is maintained within specified limits. The feedback in this scheme is that the more air is heated, the less the lamps warm, and vice versa.
Digital incubator temperature controller
Depending on the features of the internal circuit, analog and digital thermostats are distinguished. The first are cheaper, but because of the low-current electromechanical relays used in them, they have a shorter service life. In addition, analog controllers typically control the temperature by turning the heating element on / off. In digital relays, it is replaced by a non-contact semiconductor controlled key, which not only provides higher accuracy of temperature maintenance, but also allows you to control heating by limiting the amount of voltage supplied to the heat source. The limit can be set both by turning the handle of the variable resistor, and by pressing the buttons. It is recommended that you use digital solutions.