The worm gear system consists of two components - the wheel and the worm itself. It is necessary in order to get rotation and transfer it between the intersecting shafts (from one to the second), while reducing the speed and number of revolutions. The wheel works in conjunction with a worm, which can have left or right thread, as well as single or multi-start.
Basic data
The worm is a threaded screw that transfers its rotation to a helical wheel with arched teeth, causing it to rotate.
The teeth and turns of the screw are coupled. The axis of the shafts of the worm wheel intersect at right angles, the screws intersect in the same plane and are mutually perpendicular.
The possibility of self-braking allows movement only from the worm to the wheel, otherwise braking may begin and a stop will occur.
A cutting tooth screw is a worm cutter that is used in a worm wheel. Such cutters have different classifications (processing, number of visits, etc.).
Varieties
The classification of worm gears is divided into two types: globoid gear worm gears and cylindrical. The globoid version requires focused precision manufacturing and increased attention to cooling, and when worn out, it reacts very subtly to the displacement of the screw along the axis. The cylindrical appearance has circular cylinders on the surfaces of the wheel and the worm (initial and dividing).
The thread of the worms can have trapezoidal thread in the axial section (the most popular type is Archimedes), the same profile, but in the normal section (convolute), involute (with the same thread in the axial section) or with a concave profile for maximum contact with the wheel.
Advantages and benefits
The benefits include:
- quiet and smooth ride due to a special coupling;
- reliable work;
- small size and compact design;
- the possibility of reduction (obtaining large gear ratios) using one step;
- self-braking or stopper, the absence of a possible reverse stroke;
- ease of use and manufacture of worm wheels;
- low cost relative to other gears (cylindrical).
As for cylindrical gears, with which worm structures are often compared, their advantages include a high efficiency, weak perceptible heating and slight backlash of the output shaft. They are also reliable and have high performance, there is no independent stopper.
disadvantages
The main disadvantages of the worm wheel include reduced power and limitations on its transmission, a decrease in the efficiency, as a result of which the transfer of heavy loads is impossible. Also, for the manufacture of some parts, strict accuracy must be observed, the use of expensive and rare materials, special lubricants, and with quick wear or stuck quality adjustments are important. The minuses may include an increase in housing temperature and heating at the clutch, an increase in the backlash of the output shaft when the gearbox wears out.
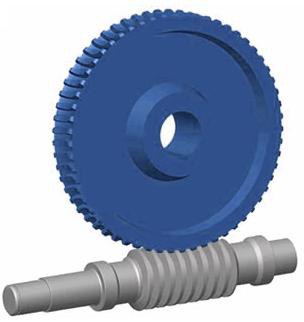
Periodically, it becomes necessary to reverse the output shaft without resorting to starting the gearbox. In this situation, locking, which is considered a virtue of this type, becomes its disadvantage.
Despite all the flaws in the form of increased heat and lack of power transmission, this transmission option is used in cases where there are no significant shock-type loads. This is a budget and relatively cheap option, which is used in engineering, mixers, conveyors and conveyors.
Worm gears are compared to cylindrical gears, which also have a number of disadvantages. They have a low gear ratio with a single stage.
Scope of application
Worm gears are used as a gearbox in order to reduce the number of revolutions. Such an element is used for cars and other vehicles, in various machine tools and cranes, machines, when lifting goods.
The use of worm gear wheels in cases where at low cost it is necessary to reduce rotation and accelerate torque is relevant. The worm in each of these options sets the movement, the wheel reacts.
Product design
As you know, a worm wheel is a transmission consisting of two links: a driven and a leading one, which operate in a coupler. The main one is a screw in the form of a screw, which sets the motion for the second element - a helical wheel. It is on its teeth that the turns located on the screw slide.
Together, this is a gear-screw system. Most often, worm wheels are composite, this affects the cost, lowering it.
The worm is the leading one, and most often the reverse transmission is not feasible, since
this may cause the gearbox to brake. The teeth of the worm are longitudinally circular turns.
Archimedean screws are the most common type of worms in mechanical engineering. This option is in demand and easy to manufacture.
The standard options for worm wheels in mechanical engineering include bimetallic, bandaged and bolted structures. The first is often found in mass production.
Materials used
For the manufacture of the worm wheel, specialized anti-friction materials are used that prevent jamming and jamming, contribute to long-term operation and wear resistance, and affect the coefficient of friction, reducing and decreasing it.
In the event that all materials are selected correctly, the efficiency is increased, and friction does not cause additional costs.
Various materials and alloys are used for the links: steel for the screw, paying particular attention to the material grade and its hardening. Most often, the screw is one-piece, joint with the shaft. Packed options are occasionally found.
In the manufacture of wheels used bronze, as well as alloys of tin and nickel, aluminum and iron. Perhaps the use of cast iron, brass for the ring gear. Often the wheel has a steel or cast iron hub. Cast wheels using a centrifugal method.
Forms and types
Screws are divided into left and right, depending on the location and direction of the turns. In the first case, the screw is unscrewed, performing a clockwise movement. In the second case, moving in the same direction, the screw is screwed in. These changes can be noticed when tracking the movement from the end of the screw.
The screw may have one or many turns (ridges), which, depending on the number, are placed on a helical line located on the dividing cylinder. This characterizes the number of screw runs.
The worm can be located above, below or to the side of the wheel, thus changing the shape of the transmission.
The shaft of the worm wheel may be horizontal or vertical.
The surface and thread profile of the screw can also vary, and several transmission options are possible, each of which has its own cutting method (with convolute, involute, Archimedean screw).
In addition, differences are possible in the worm wheels, depending on the shape of the surface of the screw on which its thread is formed (cylindrical or globoid screw). In the second case, the transfer has a higher efficiency, but is not easy to create and release, the hallmark of the formation is the arc of a circle. In the first embodiment, the distinguishing feature is a straight line that forms a dividing surface.
The worm wheel is the main part of the worm gear, which includes the wheel and screw. These two links are a worm pair, which interacts with each other according to the principle of helical. Gearboxes are made on its basis. The product has a low efficiency, but is simple to manufacture and use.
We examined what a worm wheel is, highlighted the main advantages and disadvantages, indicated production materials and the scope of application.